Quay Quarter Tower
Jan 6, 2023
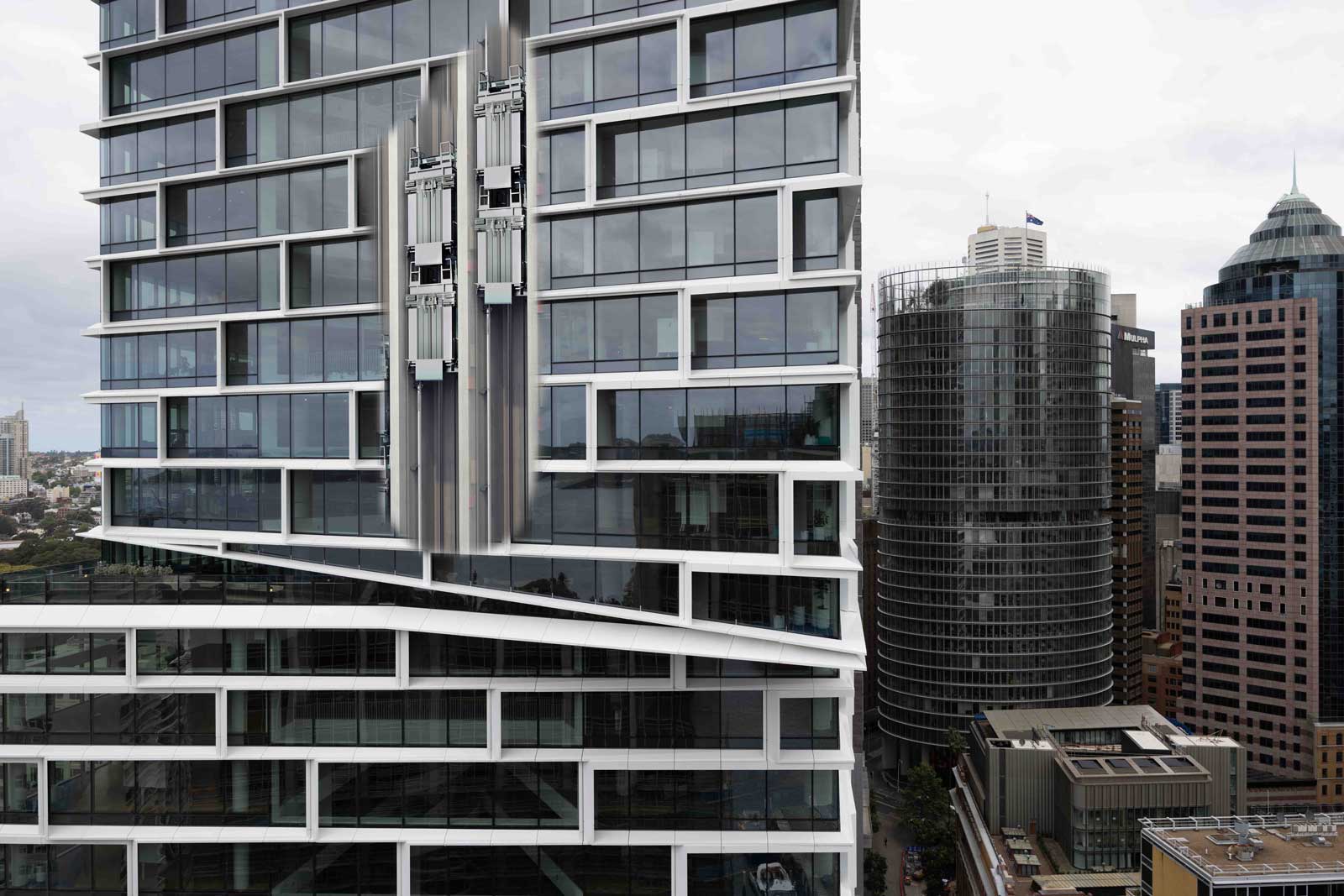
Challenging elevator modernization in a world-first upcycling project where 60% of the existing building was retained for expansion
Elevators, Modernization – Sydney, Australia
submitted by Robert Dean, Schindler Lifts Australia
Project Description and History
Originally built as the AMP Centre in 1976, 50 Bridge Street underwent a redevelopment beginning in 2018 that increased its height, incorporated additional floorspace and modernized the tower’s entire form and design. The building re-opened as the Quay Quarter Tower in 2022 and currently stands 216-m (709-ft) tall with 54 floors.
The tower in its original form consisted of 45 floors. It was used for commercial office space and was made up of concrete, glass and steel. Designed by Peddle Thorp & Walker and built by Mainline, the center’s roof height reached 188 m, making it the tallest building in Sydney at the time of its completion, prior to the completion of the MLC Centre in 1977.
In what is considered a world-first innovation, rather than demolishing and rebuilding the skyscraper, leading Danish architects 3XN upcycled the building, retaining 60% of the existing core structure. The tower has been expanded, improved and recycled to create the new state-of-the-art Quay Quarter Tower with its new façade and building services and doubled floor plate size. The retention of the original building made this project a particularly challenging modernization and installation of the vertical-transportation (VT) system.
The building is designed as a world-first vertical village that redefines the future of work. Offering some of Sydney’s best views, this transformative statement on Sydney’s skyline is focused on promoting human interactions and smart technologies to drive business success. Set to be an enabler of change, it is a zone of diversity, creativity and connectivity that will revolutionize how people work. Quay Quarter Tower sets a new global benchmark in workplace design and innovation.
Client Brief/Specification
This project was always going to be a challenging one for the development team. Quay Quarter Tower redevelopment included a complete redesign of the VT system. The development, which was based on the existing AMP Tower, included increasing the floor plate size (Nett Lettable Area) on all floors and adding floors at the top of the building. The VT design included changing the lifts from traditional, conventional control single-deck lifts to double-deck lifts with an advanced PORT Technology Destination Control system. Eighteen double-deck lifts were installed in both new and existing lift shafts with four single-deck lifts serving the four new floors at the top of the building.
This complex project required extensive design and communication with AMP Capital, Multiplex, 3XN and BVN throughout all phases of the development. Through consistent coordination and collaboration, Schindler was able to deliver a high-performing VT solution to carry tenants around the building with unparalleled ease and speed.
To ensure the premises would achieve its A-grade status for VT services, there were a number of requirements outlined by the client and by the VT consultants:
- Deliver a world-first vertical village that redefines the future of work
- Minimize embodied carbon emissions
- Create an efficient façade
- Implement new, efficient mechanical systems
- Achieve 5.5-star NABERS Energy rating
- Achieve 4-star NABERS Water rating
- Attain PCA “Premium” Grade — Maximize opportunities of views/not look at 33 Alfred St (toward the quay)
- Provide occupancy for 10,000 people
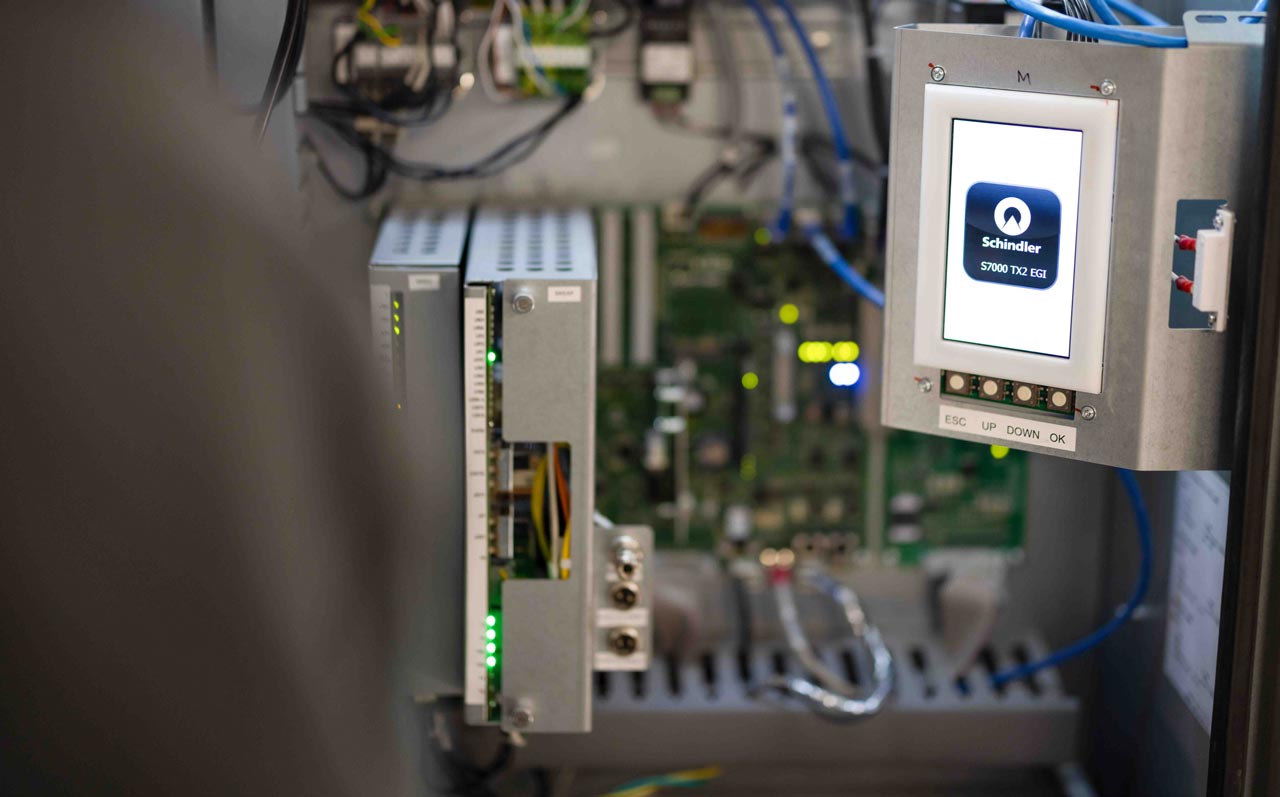
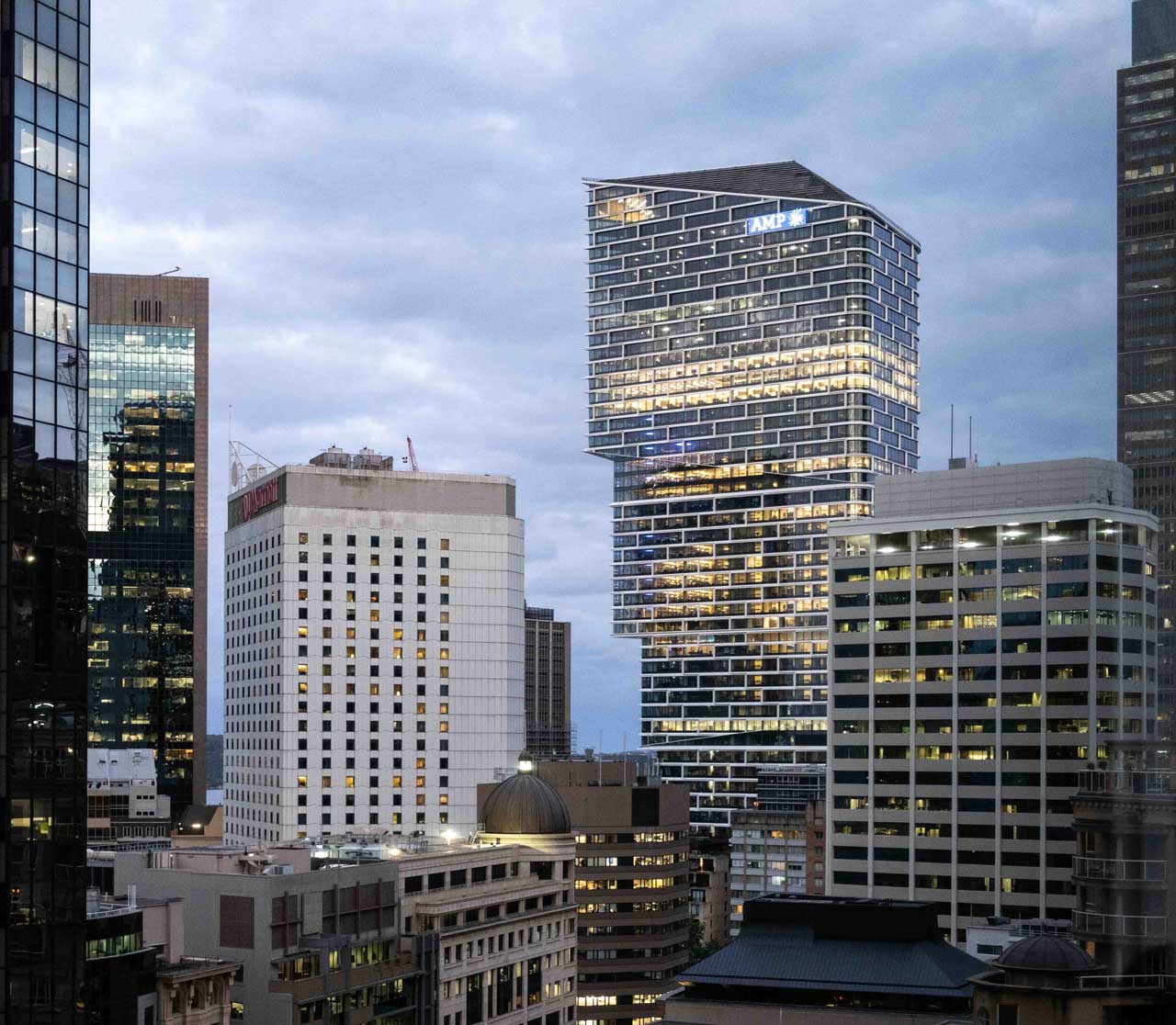
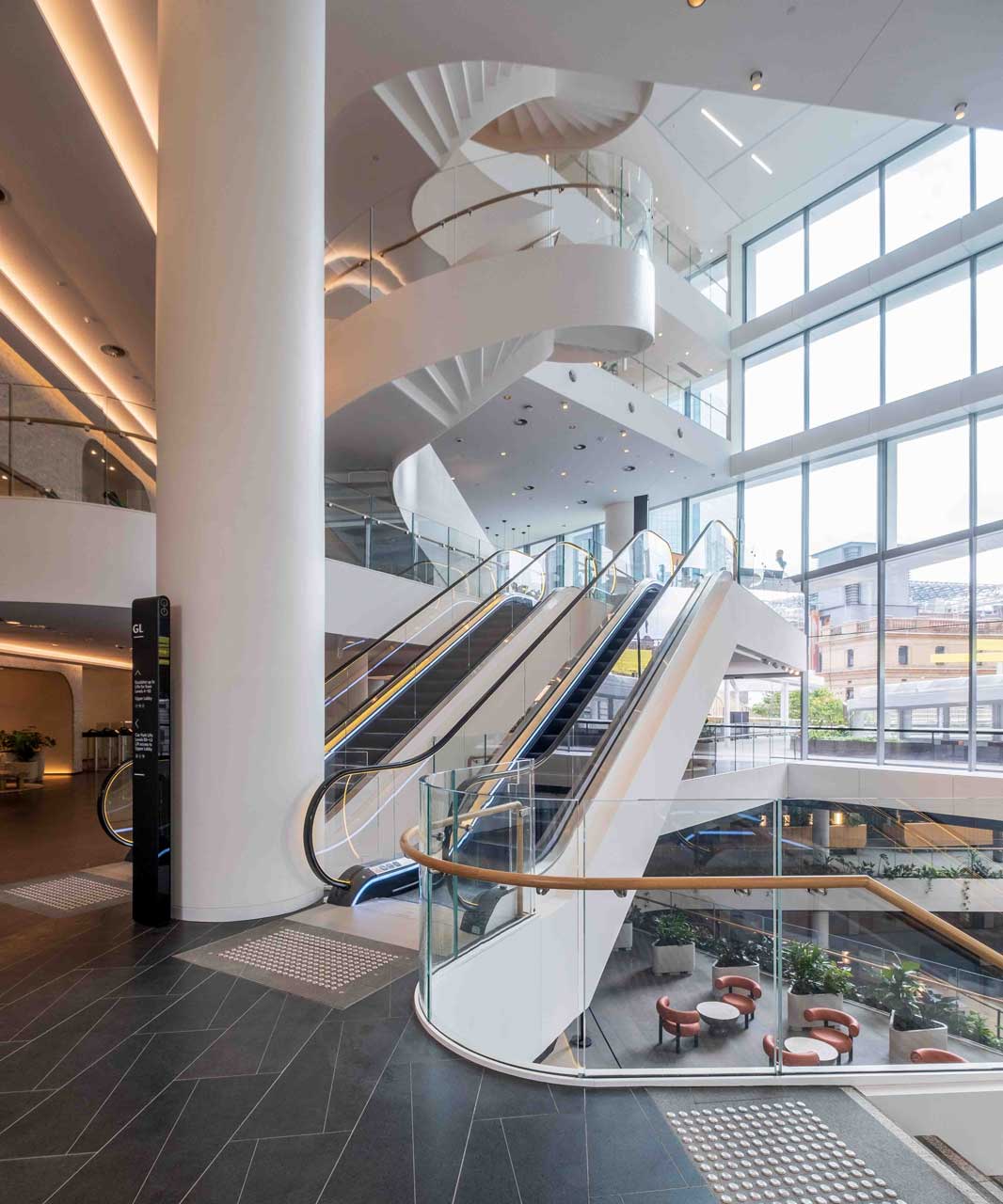
Elevator System Specification
Schindler 7000: Schindler 7000 — The high-rise elevator | Schindler Australia
- 18 x double-deck lifts
- 7 x low rise
- 5 x high rise
- 6 x sky Rise
- 6 x additional 7000s
- 4 x super sky rise
- 2 x goods
Schindler 5500: Schindler 5500 — The modular passenger elevator | Schindler Australia
- 7 x 5500s
- 1 x super sky rise shuttle
- 1 x kitchen
- 1 x retail
- 1 x podium
- 3 x car park
Schindler 9300: Schindler 9300 — The flexible escalator | Schindler Australia
- 10 x 9300s
- 5 pairs servicing the podium, retail and lobby floors
Schindler PORT Technology — Schindler Port Technology — Personal Transit Management | Schindler Group
- Integrated into low, high, sky, super sky, goods and car park lifts
Third-party equipment
- 3 x third-party hoists
- 2 x goods hoist
- 1 x dumbwaiter
Project Highlight — Double-Deck Lift Specification
To significantly increase the passenger capacity of an elevator shaft and improve efficiency in the building, Schindler implemented a double-deck elevator solution, allowing passengers on two consecutive floors to be able to use the elevator simultaneously. Passengers may board the lower deck (which serves only odd-numbered floors) at the basement level, while another passenger may board the upper deck (which serves even-numbered floors) on the ground floor — the car serving even floors is on top of the cab serving odd floors. Using this technology, the elevators take up less building core space than traditional single-use elevators.
Double-deck elevators need fewer hoistways than single-deck cars and create significantly more rentable space, making for a more profitable building. The Schindler 7000 double-deck elevator has evolved from proven Schindler 7000 single-deck technology. The ride is extra-smooth and very efficient.
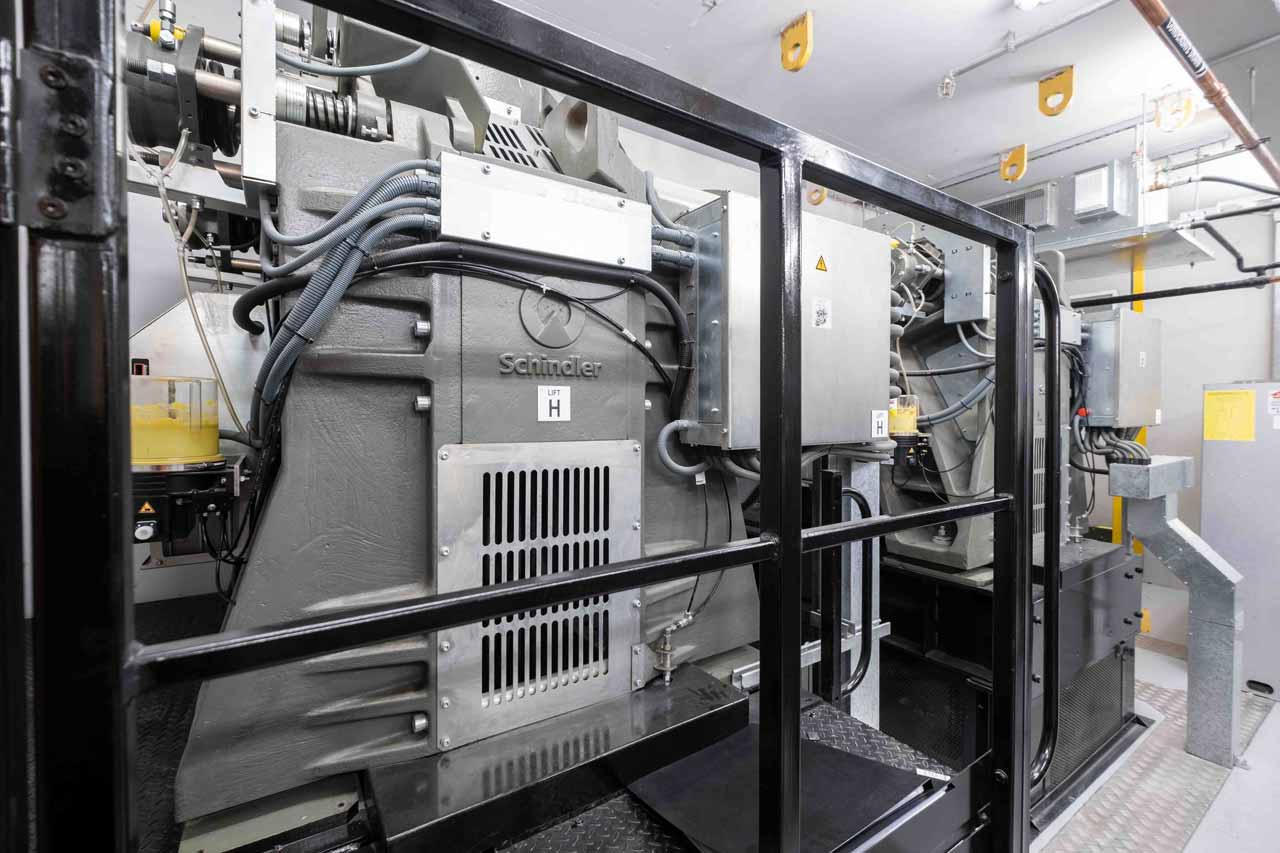
Project Challenges — Double-Deck Lift
The double-deck unit is a remarkable innovation for increasing mobility around a building. This is especially true where the shafts are already defined by existing structure and the floor plans and person count are increasing. What is perhaps most interesting about their use is the most complex and interesting parts are hidden so that when the lifts operate, they appear to be nothing more than a standard elevator. There are, however, several complications that come from installing a second deck onto a car:
- Adjusting the float of the two cars separately so that the ride quality is of a consistent high quality.
- Making sure the two car door operators are perfectly aligned so landing door locks are not clipped.
- Facilitating additional traveling flexes for the extra communications equipment needed to service the two cars.
- Allowing for floors where the inter-floor distance could not be maintained due to structure.
- Working in the crouch zone between the two cars.
- Additional floor hatch in the upper deck and rescue procedures for emergency evacuation.
- There was an extensive level of demolition, working in compacted and narrow existing elevator shafts, confined spaces for material marshalling and decommissioning of existing elevators and removal of obsolete material
- During tender stage, the previous AMP tower was still occupied and functioning, leaving Schindler with limited access to inspect or survey existing elevators and associated structures. The Schindler team had to rely only on very old and dated drawings or surveys. Only when taking possession of shafts and motor rooms, did the challenges of delivering a world-class project become clear.
- 17 elevators were decommissioned, making way for new ones. The front walls of all of the elevators were removed to create space for the new landing doors, which were then recessed into the lobbies, thus creating the required additional shaft depth to allow sizing elevators to A grade.
- The old shafts, a mix of concrete and brick work, created many challenges for the installation and engineering teams in terms of designing and adapting.
- Due to the new traffic calculations and new building layout, what used to be the low rise or high rise made way for sky or super sky elevators and, in the process, additional floors were built at the top of the existing tower. Some motor rooms at the lower levels were then confined to the footprint of existing shaft elevators, posing additional challenges for the design team to house a large portion of gear. A two-tier motor was then adopted.
- Double-deck lifts required equal floor-to-floor distances. New raised floors were provided, which, in turn, resulted in a range of different and diverse door sill arrangements and ways to install new fire-rated landing doors.
- The new construction core was built side by side and linked to the existing one, forming common lobbies. The old AMP Tower was built in the 1970s. Almost 50 years later, concrete structures had compressed and settled in comparison to new and fresh concrete shafts that would also naturally compress and settle over time, calling for many calculations to ensure elevators in the old and new (but common) lobbies would remain level and within the floor tolerances.
- Up in the machine room, the specs of the drives and machines had to be increased considerably to handle the weight of an extended superstructure, two cars and associated loads and the built-up counterweight. This included large PMR710 machines in the sky rise to handle the high-speed heavy loads, twin drives and a two-story machine room to facilitate the large floor space required.
- This project was a first for everyone on the development team and was certainly a learning curve for all agencies.
- Temporary decks needed to be installed in the lift pits to accommodate the building of the double-deck cars. Scaffolding was required to gain access up through the pits and to build the decks at the correct height.
- The different heights of the cars meant that work could only be completed on one car in a bank at a time. It took almost two weeks to complete the build of each double-deck car before being able to move onto the adjacent car, rather than building them simultaneously.
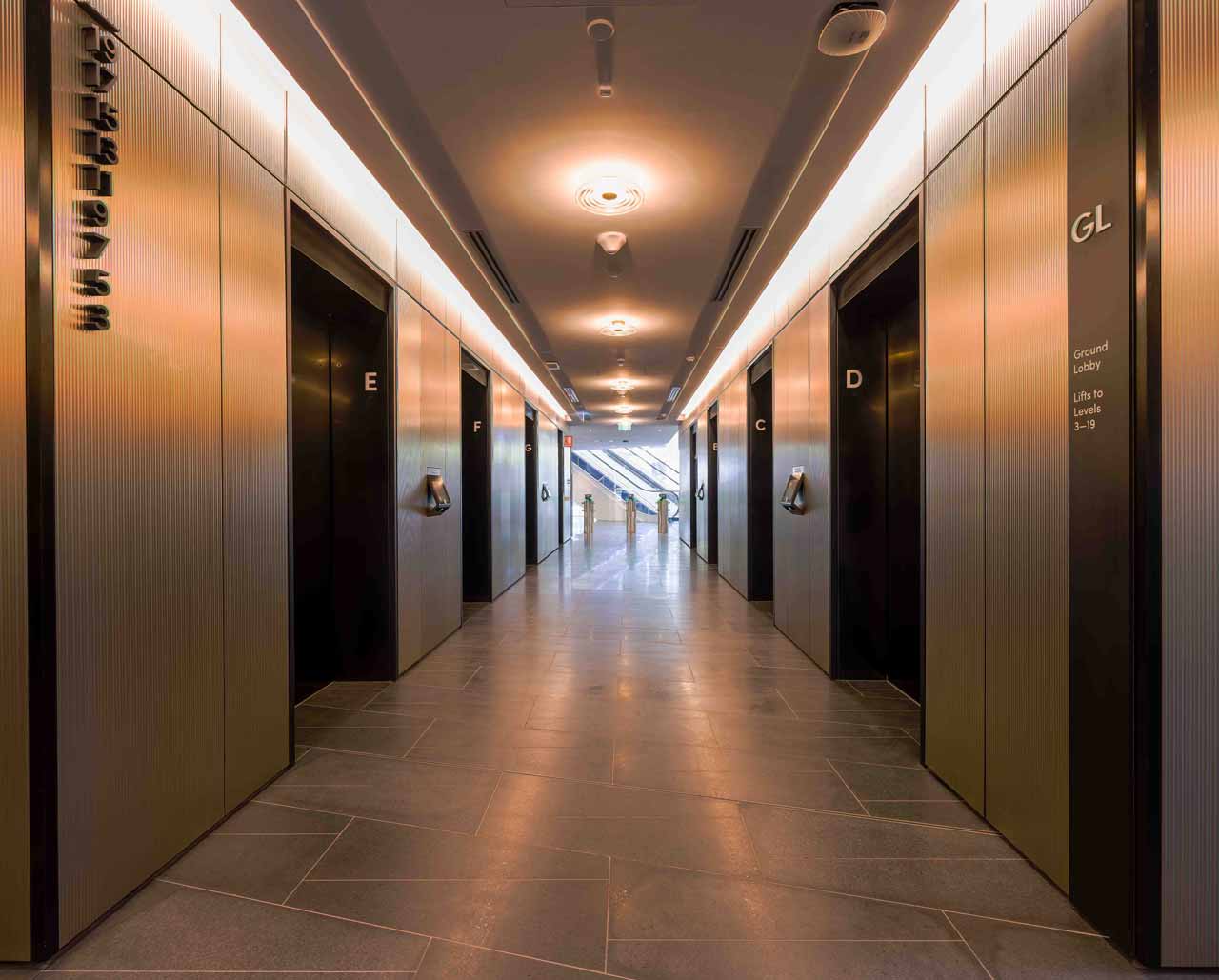
Project Challenges — COVID-19
As with the rest of the world, Sydney and 50 Bridge Street were subject to the effects of COVID–19. The project underwent numerous rapid changes to management strategies to minimize risk to workers, as well as a mandated period of construction shutdown. The Sydney lockdown criteria underwent several changes through the period, and without delving through the entire history, this meant a rapidly changing pool of available staff who could work on the construction site. On top of this, there were numerous staff, sub-contractors and coordinating trades who were forced to isolate. This meant from the middle of 2021 through to practical completion in April 2022, the site team had to be flexible and mobile with their program as skills and people became unavailable. The changing site conditions and spectre of COVID-19 was difficult to work through, but the site team kept morale high with a clear vision of the completed project.
Schindler performed and assisted with critical parts of the site’s COVID-19 management plan. As a solution to social distancing requirements, Schindler was engaged to ready a great deal more builder’s lifts than was originally scoped: Seventeen out of the 24 7000 lifts and four of the seven 5500 lifts were commissioned as builder’s lifts. This was required because as lift construction progressed, lift interiors became available and different parts of the building progressed and the lifts had to be taken in and out of service for the safe transportation of people. As the program and construction continued, a number of these lifts were commissioned for a second time as a builder’s lift before being finally commissioned. Several escalators, too, had to be prepared with protection to serve as accessways for people flow through the lobby floors. The time, coordination and commissioning of resources that went into making this possible were significant, particularly at a time when the team was already at their limits.
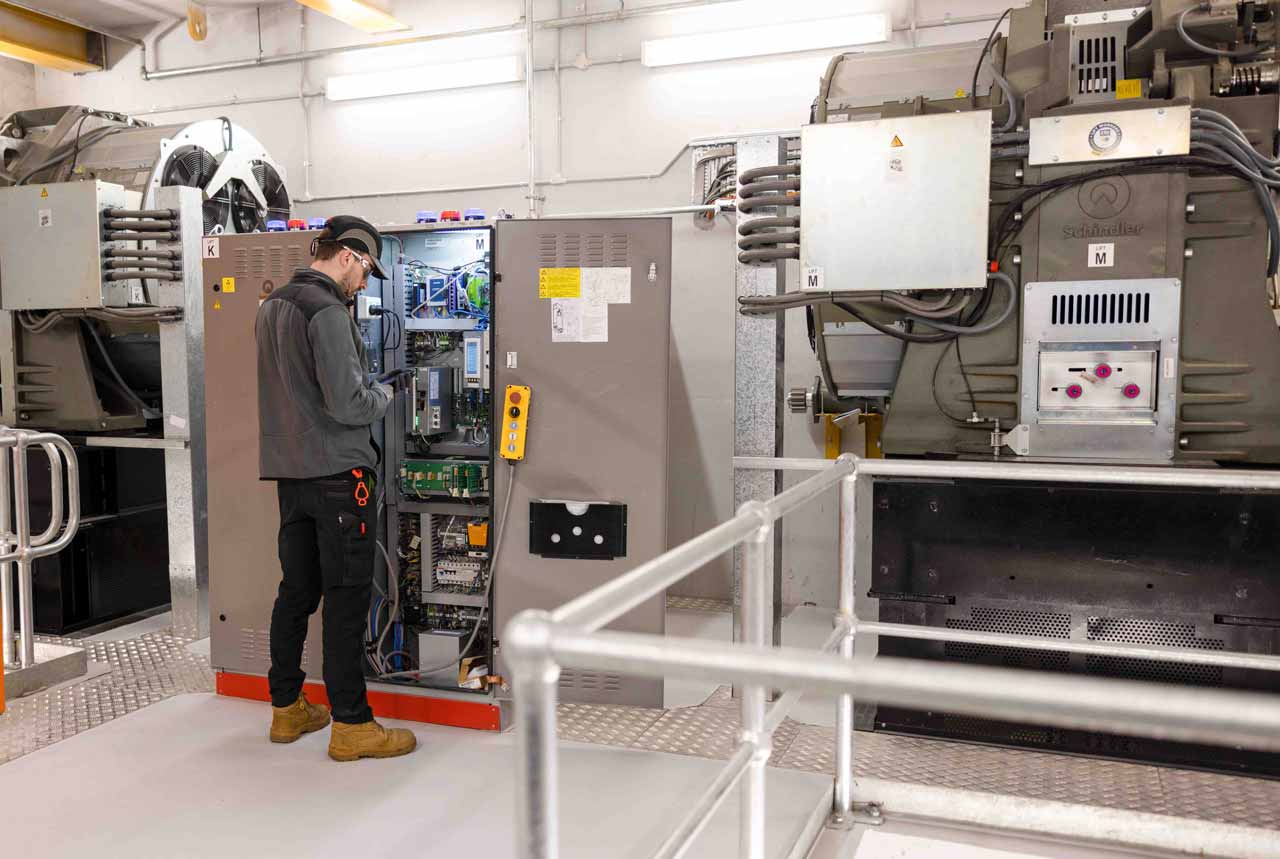
Project Challenges — Installation
- Working in existing shafts with all brand-new equipment. A great deal of custom interface bracketry was required for door frame, sill and header interface to blend in properly with the existing building.
- The site was effectively a demolition site when Schindler first arrived. There was mass strip out and deconstruction going on around the cores and lift lobbies. Strict coordination was required between trades to ensure that material was removed and installed safely. This was especially important, as there was material being moved into and out of the building simultaneously. This also meant there were areas of the building that were unable to be navigated with trolleys to move equipment into the pits for early-stage construction and rail erection. This affected the machine room, as well, where machines had to be delivered disassembled and moved into place piece by piece and then re-assembled.
- Due to the extensive demolition, almost half of the building was removed, creating vast hazardous areas. This required attention and detailed supervision of all field personal. Additional safety concerns revolved around being on a demolition site, particularly associated with the constant loud noise that required ear protection. Often, being confronted with conditions imposed by the demolition work prevented continuous and steady work.
- Floor levels had to be carefully coordinated and maintained so that the double-deck elevators could function correctly. A slight deviation between the inter-floor dimensions could result in trip hazards. In cases where the structure could not accommodate the required change to the finished floor level (FFL), the floors had to be navigated with software adjustments.
- Shafts were not to current standard and various rectification works had to be coordinated.
- Elevators, particularly those between the lower ground and upper ground over the loading dock, had to be carefully sequenced into place as parts of the floors were opened and closed.
- Rail bracket fixation could only occur at each floor intersection at odd spacing and reduced space.
- There was limited ratio between elevator sizes and existing shafts, resulting in a compacted shaft elevator installation.
Credits
Owner: AMP Ltd.
Builder: Multiplex
Architect: 3XN
Consultant: ARUP
Elevator Services Provider: Schindler Lifts Australia (SLA)
Get more of Elevator World. Sign up for our free e-newsletter.