Safety on Shell Installs
Jul 1, 2025
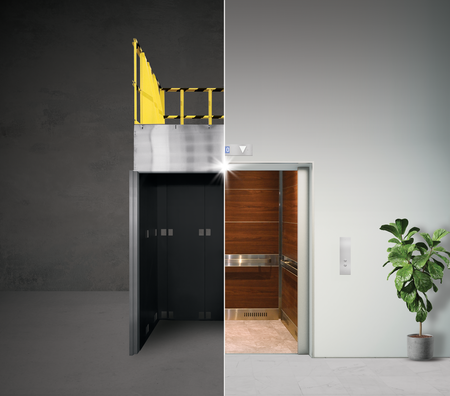
Moving beyond tradition
submitted by MAD Elevator
When elevator professionals think of shell installs, what often comes to mind are stories of heavy, awkward panels, long hours on-site and improvised tools to fasten unreachable bolts. The traditional cab shell installation process — often spanning 12 to 16h — has remained largely unchanged for decades. While it’s tempting to accept this as the industry standard, such practices pose safety, efficiency and consistency challenges — especially in an evolving sector where time, cost and labor shortages are under increasing scrutiny.
Installing a shell should not require hours on your knees or tools taped to broom handles. Yet, this remains the reality on many job sites, where mechanics must navigate cramped hoistways, heavy lifting without support and frequent workarounds for misaligned or missing parts. These aren’t just inconveniences: They’re potential safety hazards that impact installers’ well-being and increase liability for elevator contractors.
One of the most overlooked risks comes from the need to access the canopy during installation. Traditional shell designs often require mechanics to climb on top of the canopy to secure wall panels or railings, sometimes before the structure is even fully stabilized. This can create dangerous working conditions, particularly in modernizations where space is tighter and site constraints are less predictable. A safer approach allows the shell to be assembled entirely from the inside of the platform, with canopy access required only after the structure is secure.
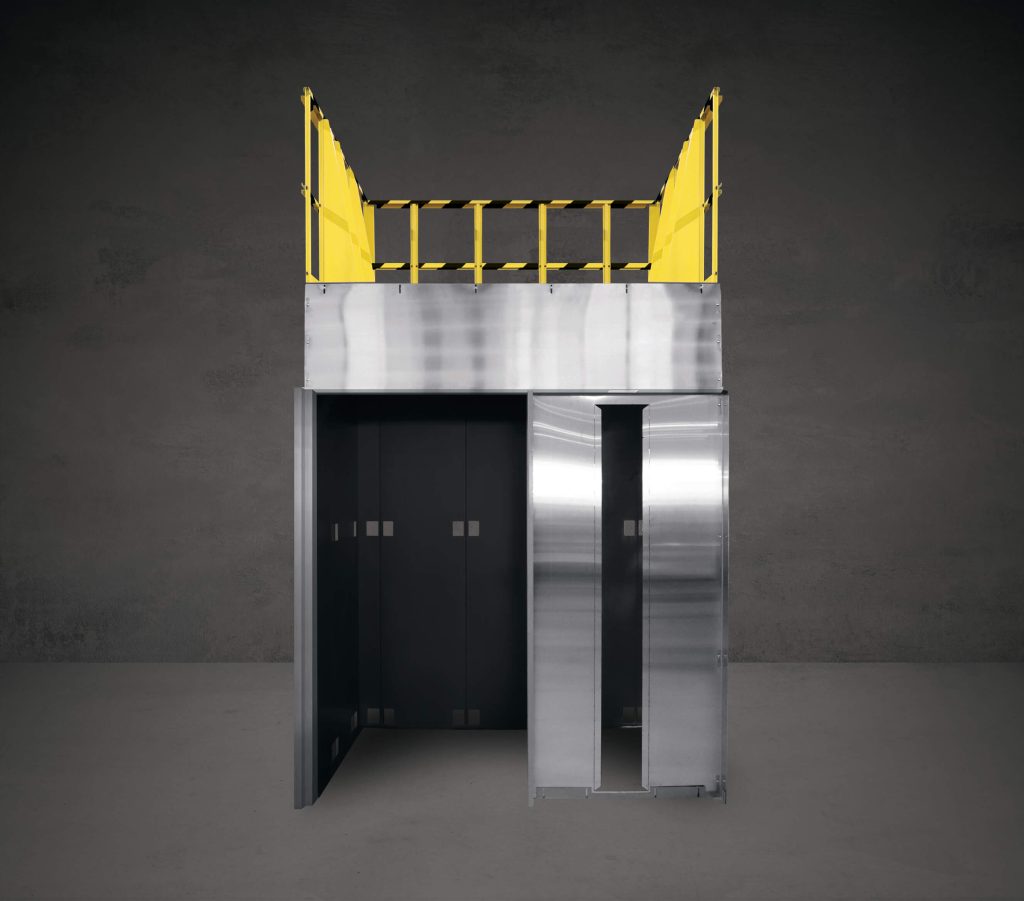
Shell Design: Not One-Size-Fits-All
Shell design has historically taken a one-size-fits-all approach. While this made sense in a slower-paced, less-regulated era, it no longer meets the demands of modern job sites. Today’s installers face tighter deadlines, more complex environments and greater emphasis on code compliance. Newer approaches focus not on reinventing the shell, but on reengineering the process behind it — from modular design and reduced fastening requirements to integrated safety components and clearer documentation.
It’s also important to recognize the difference between new construction and modernization projects. In new builds, there’s more flexibility to work with ideal dimensions and open access. In modernization, installers are working within an existing hoistway, often with limited space, older components and inconsistent conditions. A shell that works well in one context might pose serious challenges in another, so adaptable, well-labeled systems are key to maintaining safety in both scenarios.
Code Compliance as a Safety Foundation
At the core of any safe install is code compliance. ASME A17.1-2019 outlines clear standards for shell and car top structural performance, including load-bearing requirements for railings, kickplates and canopies. For example:
- Top rails must resist 200 lb/ft in any direction with no more than a 3-in. deflection and no permanent deformation (2.10.2.4).
- Shell walls must withstand 75 lb/ft horizontally without permanent deformation (2.14.1.3).
- The car enclosure top must support up to 300 lb on a 24 in. X 24 in. area (2.14.1.6.1).
- Clearance, ventilation, fire rating and visibility standards also apply to hatches, lighting and materials.
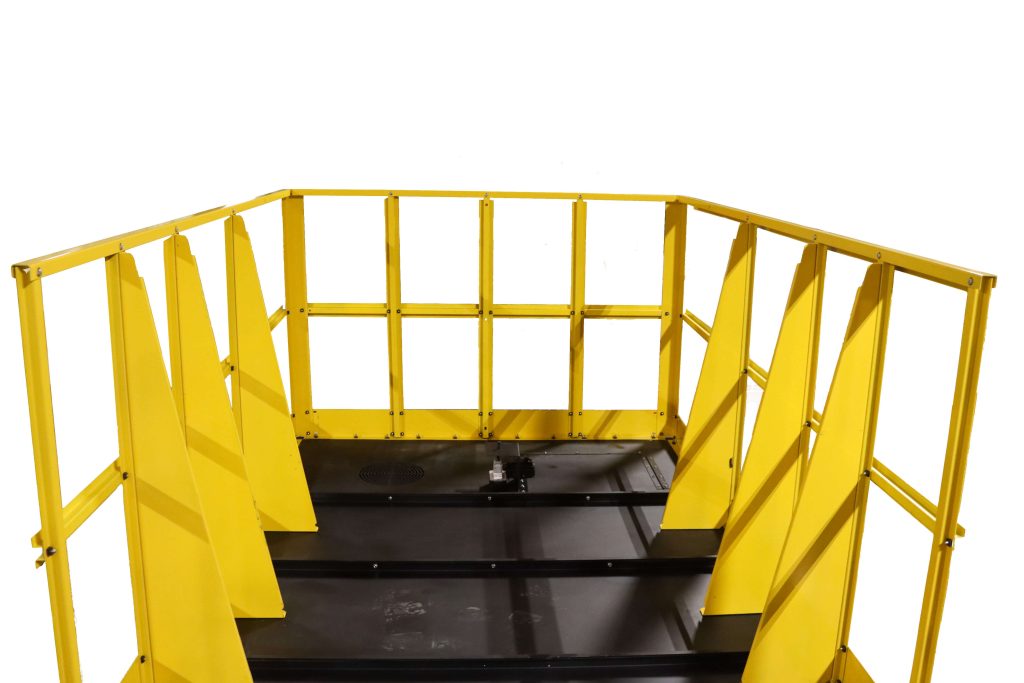
While most shell systems technically meet these requirements, compliance alone doesn’t guarantee safe or easy installs. The process and environment matter just as much. Installers need to know they can work safely from inside the platform without having to reach behind wall panels or climb onto unsecured surfaces. They also need clear labeling, intuitive instructions and parts that fit together with minimal adjustment.
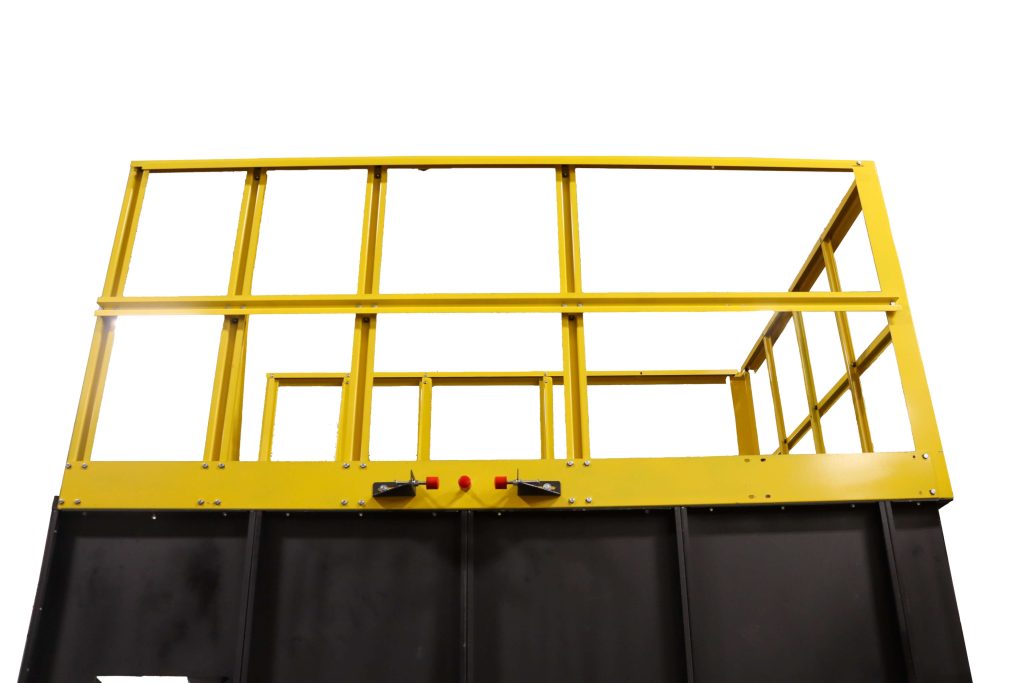
Building Toward Safer Installs
Progress in this area involves a combination of engineering foresight and practical field knowledge. Shell designs that use lighter, modular panels reduce physical strain on installers. Quick connect systems and pre-mounted car top rail kits eliminate the need for improvised modifications on-site. Organized hardware kits ensure no critical components are missing and that every bolt and bracket is accounted for.
Equally important is quality control before a shell leaves the factory. When verification and pre-assembly are baked into production process, the risk of misaligned holes, missing parts or unclear configurations is dramatically reduced. This, in turn, minimizes time spent improvising on-site — time when safety is most at risk.
In recent years, the elevator industry has begun to shift its expectations. Speed is important, but not at the expense of safety. Thankfully, the two aren’t mutually exclusive. When a cab shell can be reliably installed in 4 h without compromising code or safety, everyone benefits — from the installer to the end user.
As the industry continues to evolve, safety and code compliance must remain at the core of shell install practices.
Putting Safety and Compliance First
As the industry continues to evolve, safety and code compliance must remain at the core of shell install practices. For elevator contractors, consultants and mechanics, the ability to confidently evaluate whether a shell system meets ASME A17.1 requirements is essential — not just for passing inspection, but for protecting workers and ensuring consistent outcomes across job sites.
By focusing on safe design principles, simplified installation and verifiable compliance, we reduce the risk of costly change orders or safety incidents. Whether you’re evaluating a new shell product or refining your own install process, keeping code and safety front and center is the surest path to long-term success. With a structured approach to shell installs — supported by robust documentation and thoughtful engineering — the goal isn’t just fast installation: It’s safe, compliant and repeatable installation that gives contractors peace of mind and keeps mechanics out of harm’s way.
Get more of Elevator World. Sign up for our free e-newsletter.