Pre-Engineered Elevator Cab System
Jul 1, 2025
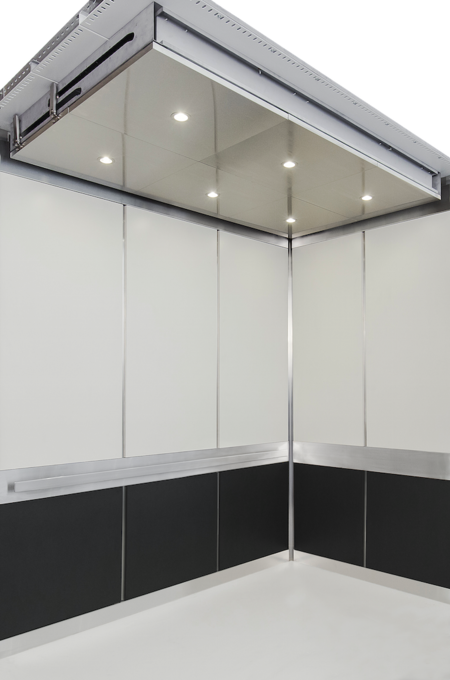
In this Product Spotlight, the simplification of cab interior design is discussed.
submitted by Bill Swenson
When planning an elevator modernization, most companies typically focus on the operational aspects of the equipment. New technologies and products are usually designed to make elevators more reliable, safer and faster. Many elevator companies have expertise in these areas. They are trained in the mechanical and electrical aspects of the equipment. However, when it comes to aesthetics, many will bring in outside contractors to perform this work for them. This is mainly due to the complexities of finish upgrades, scheduling and coordination. But pre-engineered cab solutions take the complexity out of cab renovations. Eleclip is a patented pre-engineered solution that eliminates the complexity and risks associated with cab upgrades.
Pre-engineered solutions are designed as a system that works with various types of existing cab shells. They come in various panel arrangements and finishes. Installations require minimal measurements and can be installed in less than one day. There are several factors to consider when updating the finishes on existing elevators:
- Weight
- Code-compliant materials
- Proper attachment
- Durability
- Ease of installation
The weight of materials is a critical factor when considering cab finishes. Regardless of the type of operation, weight affects performance, reliability and safety. Installers need to consider how much weight will be removed and how much will be re-installed. Any variance should be evaluated to determine the impact on the equipment and the measures that need to be taken to mitigate weight changes. New materials and installation methods are now available to reduce the weight of installed materials while keeping the same appearance.
Any new materials installed must be evaluated to confirm code compliance. Flame spread and smoke development of materials are critical factors in selecting materials to be installed in the elevator.
Common materials used in cab finishes include metals, woods, glass and plastics. All must be evaluated in terms of compliance, as well as the means of installation. In addition, the lighting must be evaluated to confirm it complies with minimum lighting requirements. New ceilings should be designed to permit access to the existing escape hatch, regardless of location.
Most original cab installations have materials that are fastened before the cab is erected. Since cab renovations utilize the existing shell and canopy, finishes typically must be applied from inside the cab. This can create issues with alignment, proper attachment and critical measurements. Pre-engineered systems utilize technologies that provide flexibility and ease to installation. The Eleclip system is designed with a fastening clip as part of the installation reveals. By installing the reveals in predetermined locations, one must only clip on the panels and lock them into place, all from inside of the cab with minimal effort and concealed attachment. In addition, replacement of the panels in the future, if needed, can be done quickly and easily.
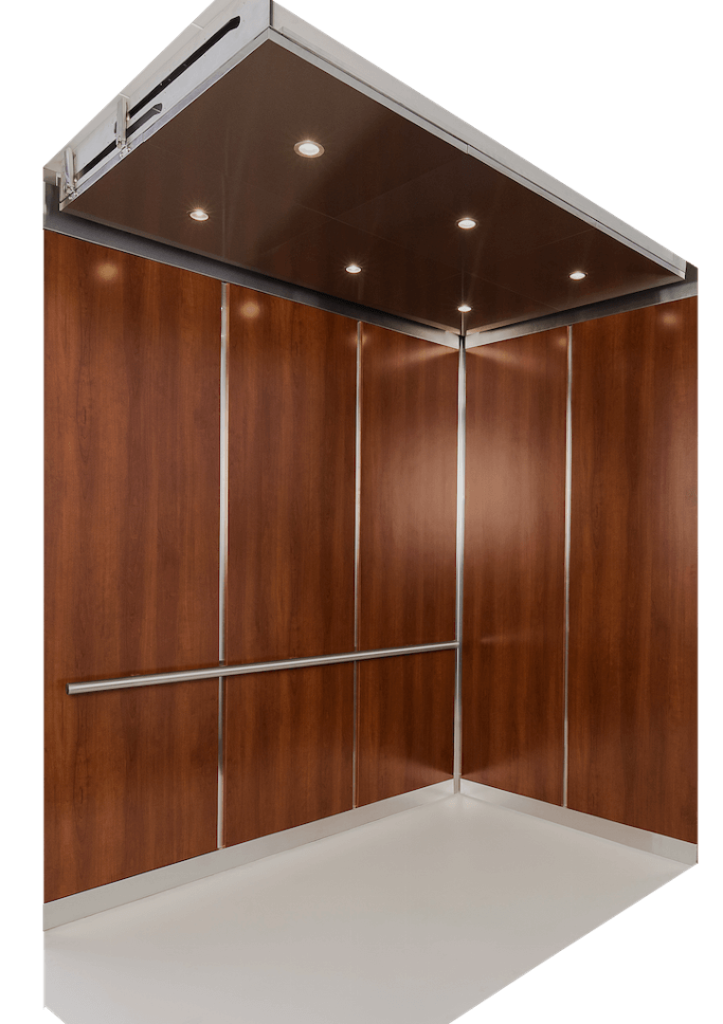
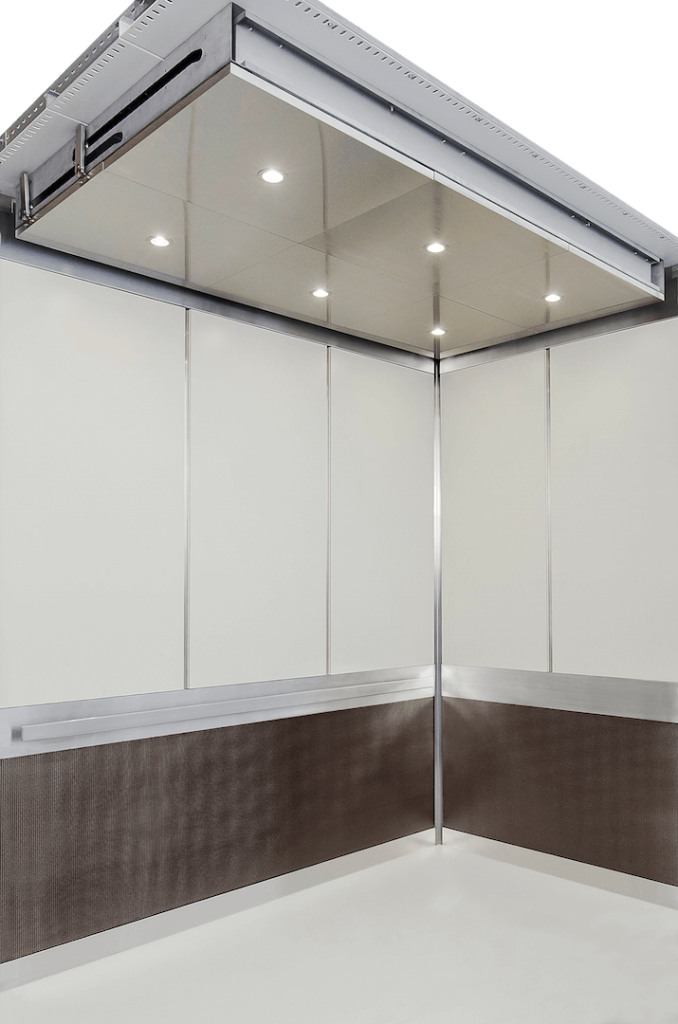
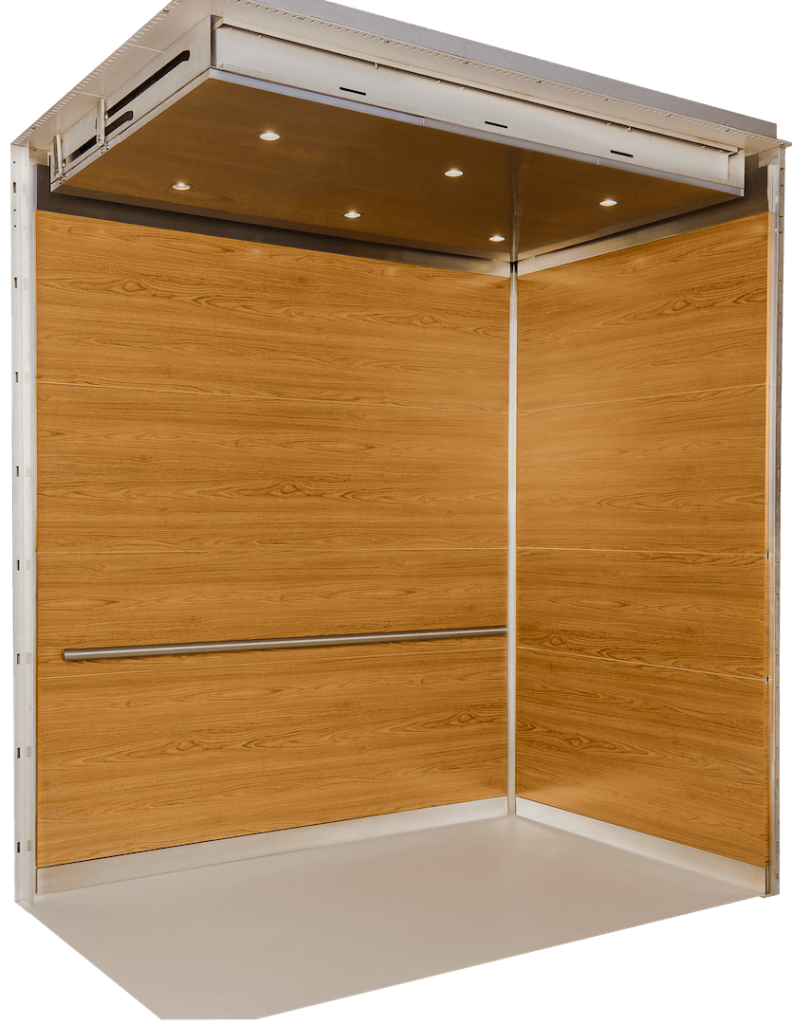
The most common finish found in elevators is typically a code-compliant wood panel faced in plastic laminate. Varying arrangements and laminates create different designs. With pre-engineered interiors such as Eleclip, different materials can be used to meet the needs of the application. Metals can be cleanly applied to lightweight substrates or wood. Utilizing V-groove technology, these panels can now have clean edges and sharp lines. Composite materials can also be utilized, as well as stone and glass. Different combinations of panel arrangements, finishes and reveals can create a multitude of designs.
By far, the most critical component to elevator installation and maintenance companies is ease of ordering and installation. The ordering and approval process should require minimal field measurements and allow for some variance. Critical factors include locations of any coved bases, cove lighting, escape hatch location and fixture locations. A simple survey form is key to ensuring all items are accounted for prior to starting the renovation.
The installation typically starts with removing any existing finishes that can be removed. These include drop ceilings, handrails, wall panels, bases and lights. Once this has been completed, the cab measurements should be verified in regard to the approved drawings.
Pre-engineered systems such as Eleclip utilize a fixed base to locate the applied reveals. Each reveal is in a fixed location and has integrated clips for panel attachment. After the reveals are installed, the panels are clipped into place. A single fastener is fixed at the top of the panel for security. The frieze is then locked into place to cover the fastener and extend above the ceiling.
Cab ceilings and lighting have always made cab renovations difficult. While many have existing lay in ceilings with florescent light fixtures, some may have light coves or island ceilings. The Eleclip pre-engineered down light ceiling utilizes a sliding tray ceiling with LED lighting. With the sliding tray ceiling, the frame can be installed easily by two people in minutes. The metal or wood panels are then clipped to the frame and the sliding escape panel is clipped into place. LED lighting can be used as direct or perimeter lighting. With sliding tray ceilings, half of the ceiling is open to allow for access to the escape hatch. Metal sliding tray ceilings are typically half the weight of a wood island ceiling and installed in less than half the time.
The development of pre-engineered interior systems takes the complexity out of cab renovations and provides additional revenue opportunities to installation and service companies. These systems make renovations much easier with minimal risk.
Get more of Elevator World. Sign up for our free e-newsletter.