Otis completes successful modernization in New Jersey.
by Joseph Caperna
The four passenger elevators at 4 Echelon Plaza in Voorhees, New Jersey, were installed by Otis Elevator Co. in 1974. As the need for modernization arose, capital planning for the modernization project began in 2015. The specification for this modernization project was created by Compass Elevator Consulting Group and distributed on April 7, 2020, prior to the bidder conference. This project was awarded to Otis Elevator Co. on December 15, 2020.
The original Otis B-base controls used a motor-generator set and operated an Otis DC geared driving machine with a capacity of 3000 lb. This group of four passenger elevators services all nine floors of the building at a speed of 350 ft/min. Each elevator has nine front openings with center-opening door arrangements. The rise of the two shared hoistways is 119 ft.
Otis provided a modernization plan that would replace the Otis geared machines with Otis Gen2® gearless machines, and replace the Otis B-base controls with Otis GCS controls with regenerative drives. This was a creative solution that would provide the building with better ride quality and unclutter the machine room. The Otis Gen2 modernization presented a unique solution that would provide the customer with a far better product than their current geared traction machines.
All materials for the project were procured during the COVID-19 pandemic, and the Otis procurement team demonstrated the flexibility needed to fulfill all material orders as soon as available. As part of this project, the following components were retained: guide rails (car and counterweight), counterweights, car frames, car safeties (refurbished), car buffers (refurbished), counterweight buffers (refurbished), cab shells, car sills, hoistway sills, hoistway entrances and hoistway door panels. Car capacity and the number of stops were also retained.
There is limited access from the building to the roof, so large materials were craned to the rooftop machine room on two separate dates using a 150-T crane with a 196-ft boom length. These procurement constraints were the first major challenge that the Otis team overcame during the modernization. This project would not have been possible without thorough coordination, constant updates and communication.
To accommodate the steel for the new Gen2 gearless machines, the existing penetration for the hoist cables needed to be widened by over 12 in. The new penetration width for the Otis Coated Steel Belts (CSB) exceeded the availability of the building steel and a professional engineer was needed to certify the new supporting structure. The Otis project foreman ensured that new penetrations and machine supports enabled perfectly plumb drops to the sheaves on top of each car and counterweight.
This successful machine replacement required critical and creative thinking from all members of the Otis elevator modernization team. This work was critical to providing the customer with a product that exceeded their expectations.
Another challenge that the Otis field technicians overcame was separating the existing Otis equipment from the group and maintaining two running elevators throughout the modernization. The Otis foreman separated the group interconnections and disconnected two of the four elevators from the group. This was very challenging, as the existing equipment was originally installed in 1974.
The foreman also directed the removal of all existing equipment. During this time, technicians performed additional maintenance on the existing Otis B-base equipment to ensure that it continued to run until the first two elevators were commissioned.
The Otis team’s dedication extended beyond the mechanical and electrical components of the elevator. Otis technicians also installed all four cab interiors — which were manufactured by SnapCab® — to ensure quality. The new cab interiors feature multiple stainless-steel surfaces and needed to be installed almost perfectly so as not to show panel gaps or irregularities. The resulting interiors were installed correctly and exceeded customer expectations.
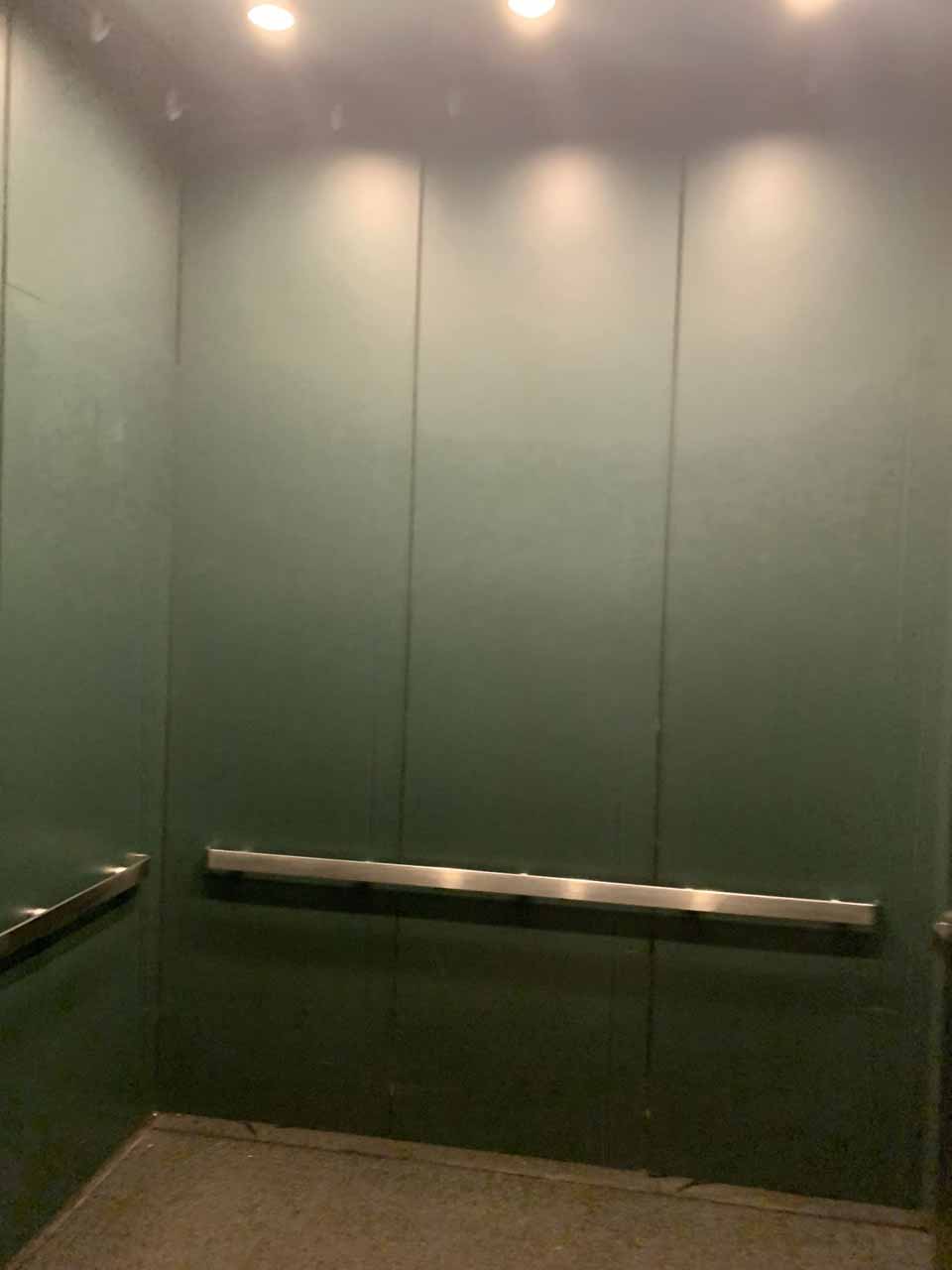
Another achievement was the completion of the code-required building work that went along with the elevator modernization. This was a turn-key project, and Otis served as the prime contractor in charge of all subcontractors. Several subcontractors performed work on the building fire system, HVAC, hoistway electrical and other finished surfaces. Coordinating this work to coincide with the elevator modernization was a substantial task. Synchronizing all required work required technical expertise and constant communication between all parties involved. The Otis team accepted this challenge and conducted several subcontractor walkthroughs.
Despite the planning efforts, the new building fire panel was delayed and would not be able to be installed before the first acceptance test. The Otis team worked with a subcontractor to find a solution that would meet all code requirements and not delay the project: The fire service subcontractor worked with the project foreman to redesign the existing fire panel to meet all code requirements for the state of New Jersey.
Before the elevators could be turned over, the Otis foreman made final adjustments and completed quality control checks. This is the most important part of the modernization process, as it ensures that the elevators continue to run perfectly after the technicians depart the jobsite.
The Otis foreman started this process by performing several measurements on the elevator system. His work went above and beyond, as he weighed the hoistway doors to ensure that the kinetic energy generated when closing them was recorded. The foreman’s other work included more traditional tasks, such as rebalancing the cab and counterweight for ideal operation, verifying that guide rails remained plumb, verifying that hoistway sills remained plumb and ensuring that zero faults were registered before turnover.
Otis worked with Compass Elevator Consulting Group throughout this project from the bid process until the final acceptance of the last elevator and completion of the punch list. All parties involved shared a professionally courteous relationship and were willing to do what was needed to help others. This professionalism was instrumental in delivering a final product that exceeded the customer’s expectations.
Otis Project Team Members
- Modernization Sales Representative Joseph Ritz
- Modernization Superintendent Brian McNulty
- Foreman Michael Eaton
- Apprentice Michael Assenza
Get more of Elevator World. Sign up for our free e-newsletter.