Simplifying Shell Installation for MODs
Jul 6, 2023
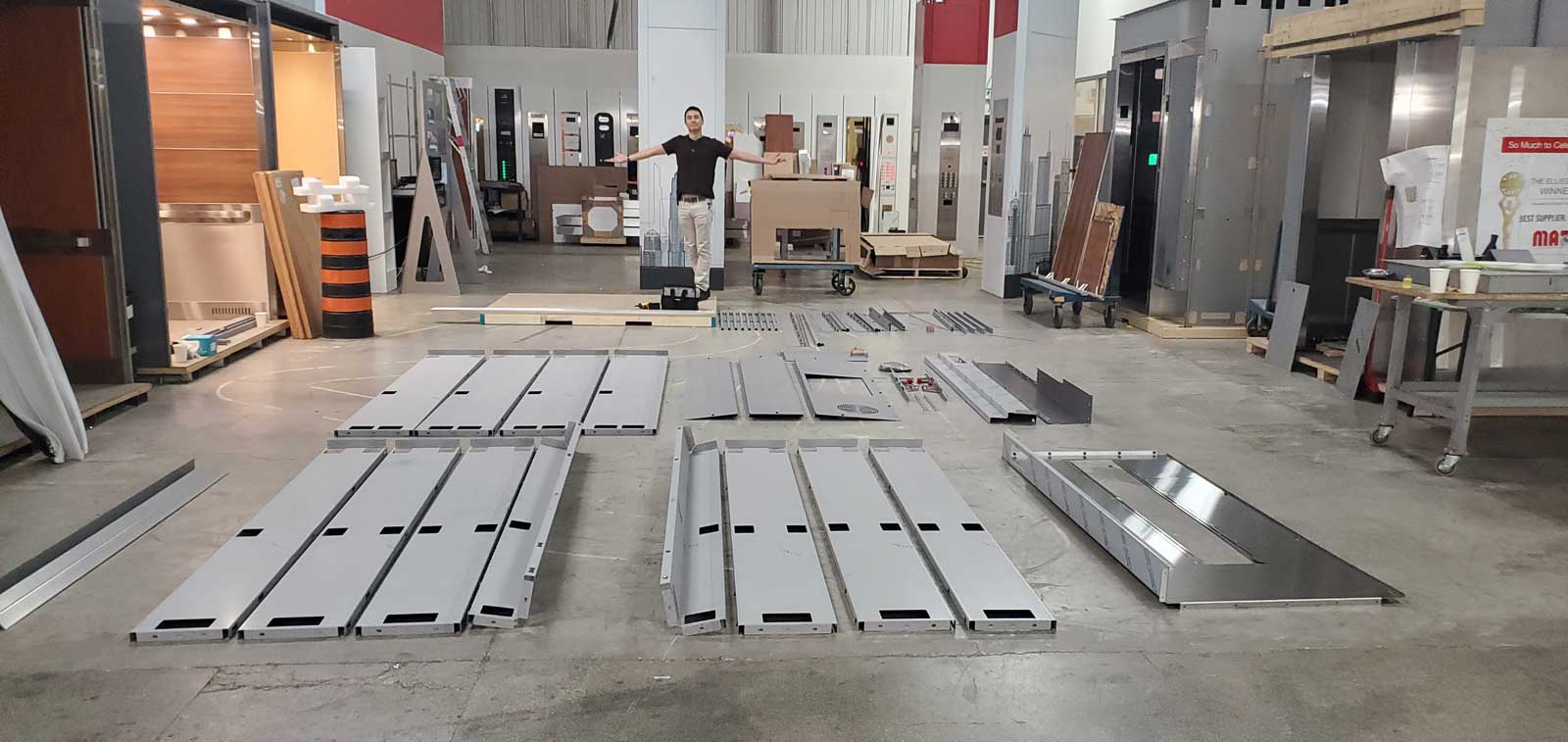
In this Product Spotlight, MAD Elevator shares the design process behind its quick-to-install F1 Shell solution.
by Jonathan Adair
At MAD Elevator Inc., our design philosophy has always been centered around real-world problem solving. The status quo is not important. The problems our customers face — and the optimal solution to those problems — means everything to us.
Like most shell vendors used for modernizations (MOD), MAD was offering a shell product that followed industry traditions like assembly from behind-the-wall panels and large one- or two-piece canopies that needed to be hoisted into place. MAD observed that in the new construction space, many innovative designs were being deployed in shells that made installation easier and faster. Why not reconsider shell designs for the MOD space?
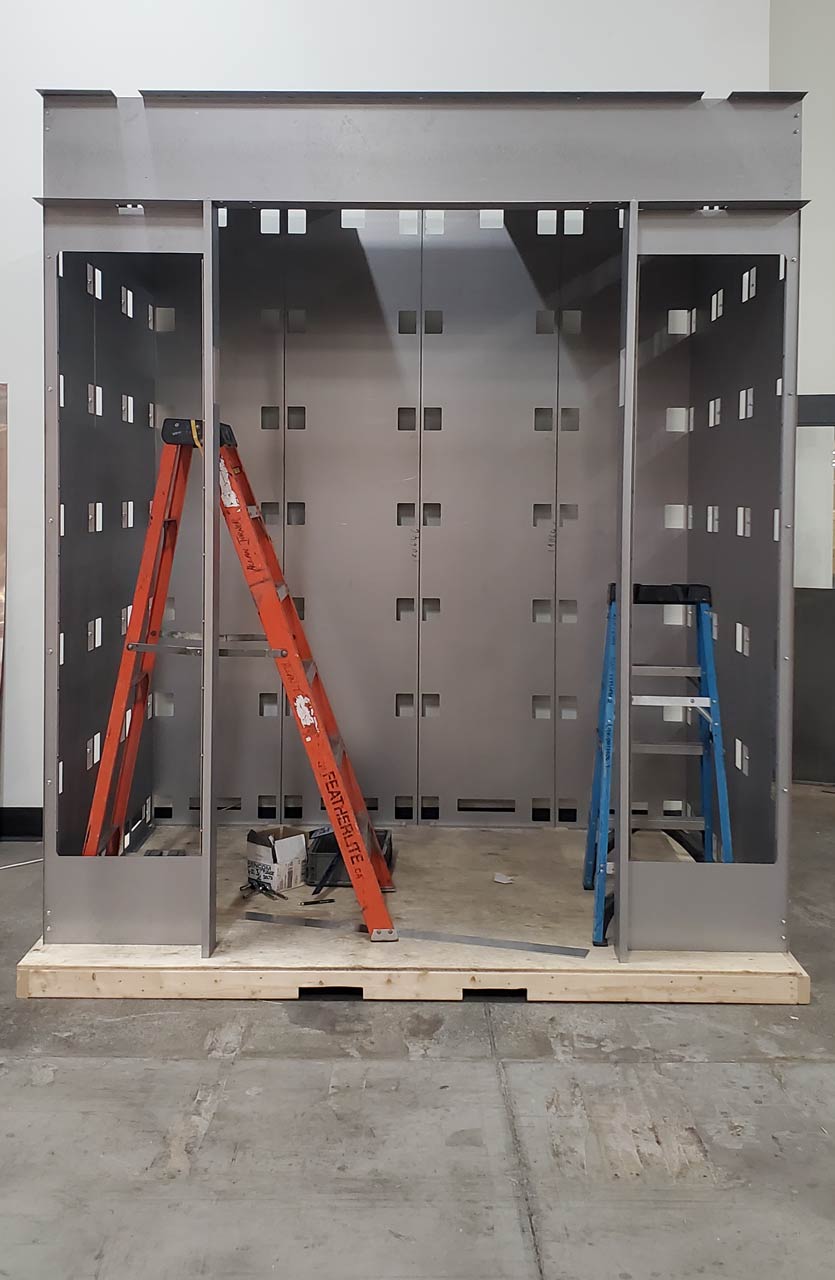
The first task was to discuss the problems mechanics face with standard shells, and who better to ask than the mechanics themselves? In general, the problems they faced were:
- Accessing the back of the shell wall panels. This can be difficult if there is not very much room between the back of the shell and the shaft, meaning whole shell walls had to be assembled and then put into place before they were connected on the platform. We heard horror stories of how mechanics had to attach ratchets to broom sticks to try to put bolts into panels to join them from above. That consumed a lot of mechanics’ very valuable time.
- Having to move large canopy sections onto the platform and hoist them into place. This method required the mechanics to hoist the canopy into place, build the non-access walls and front underneath it and then drop the canopy on top of those structures. A mechanic would then have to start attaching fasteners through the hatch or move the elevator so that some fasteners could be installed from the hall entrance above. The rest of the fasteners would have to be attached from on top of the canopy that was not yet fully secured.
- The relationship between the car fronts, the shell sidewalls and the sills. Sometimes parts of the front sit on the sill, and sometimes they don’t. Also, the height of the sill relative to the platform was not always the same. Of course, like everybody else over the years, we have seen every possible combination of design.
- The layout of equipment in the area above the canopy is highly variable, making the task of installing car top rails challenging. We were told there was an obstacle that required modification of the products in almost every case. Nothing ever goes according to plan!
With this feedback in mind, the MAD team developed a set of design guidelines that would help mechanics deal with the noted problems. The guidelines were as follows:
- It must be possible to install the entire shell from the platform or on top of the canopy. There should never be a requirement to be behind the shell in order to install it.
- There should be no piece of the shell that is too large for one mechanic to lift and manipulate by themselves comfortably.
- The car top rail should be integrated into the design so the need for customization is minimized.
- Of course, time is always against us, so we wanted to make a design that was as fast to install as possible.
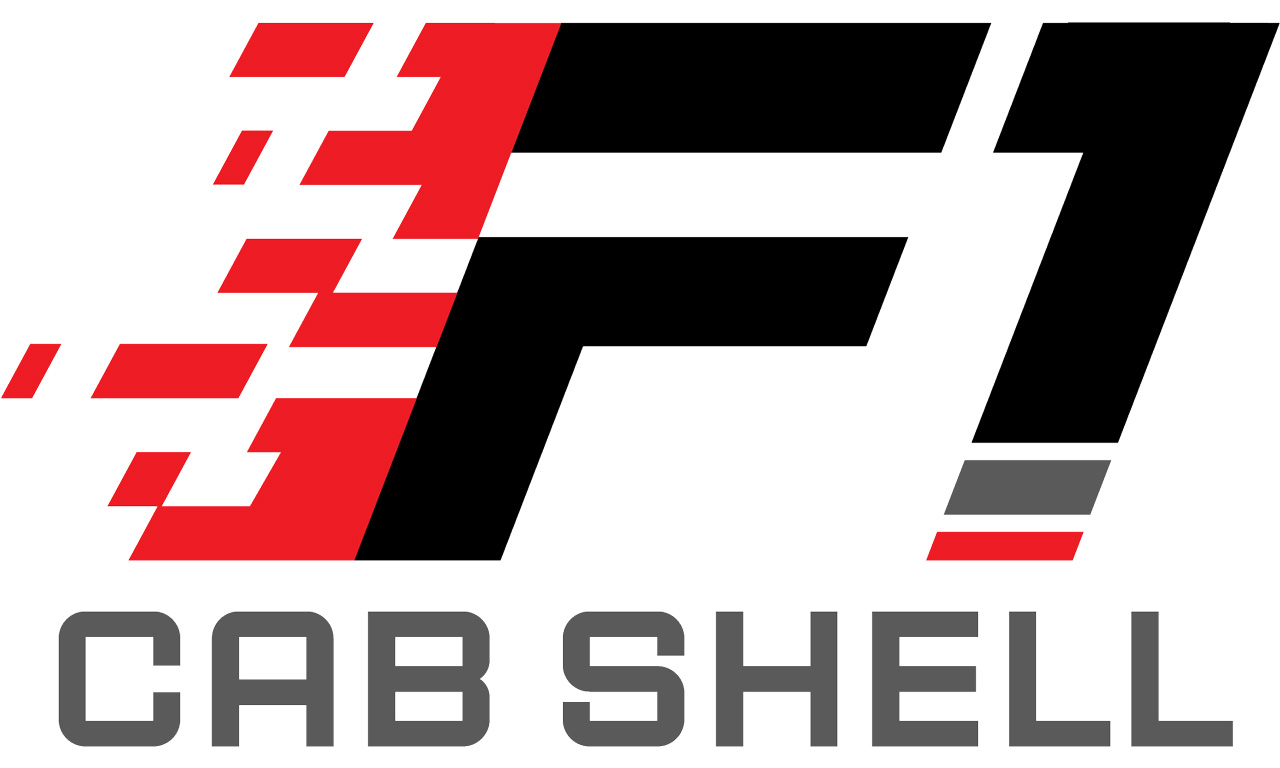
With those principles in mind, we set out to build a better mouse trap. The first and most obvious problem was how to develop a design with components that were a maximum of 25 in. wide so they could be lifted easily. We added access holes in the shell non-access wall panels so that they could be attached together from the platform. We also added access holes at the top of the non-access wall panels so that they could be used to attach canopy panels together from the platform. Thinking we were pretty clever, we built our first prototype. We made a shell that had four panels on the rear wall and three on each side wall. The shell would have inside dimensions of 75 in. deep x 96 in. wide x 114 in. high and would be the maximum design size for standard 5 ft x 10 ft materials.
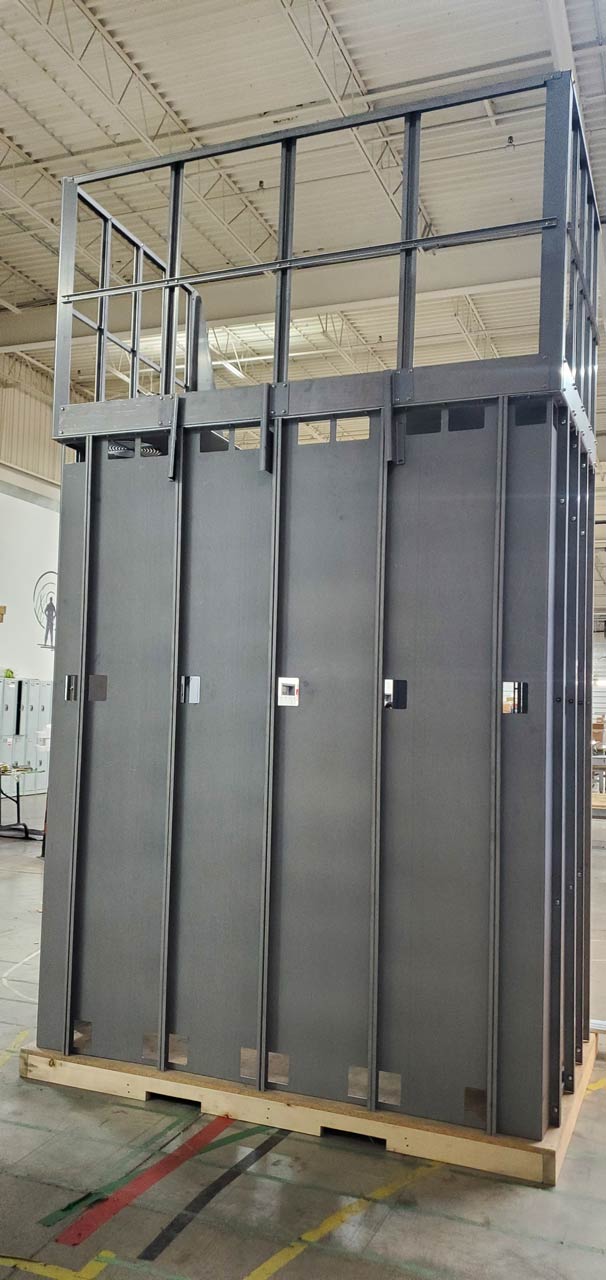
That’s a Lot of Bolts!
Next, it was time to put it together. Our goal of assembly from the platform or on top of the canopy worked out well. We were also able to secure the canopy in place before we had to go on top to add the final fasteners. After all the parts were secured together with the minimal fasteners required to hold them together, we set about installing the remaining fasteners. There were numerous fasteners, and it took a long time to put them into place. Using tools on both sides of the fasteners was slow and frustrating. Finally, we realized that there was a fair bit of work involved in lining up the front face of panels so they had a smooth interior surface with no offsets that would interfere with the interiors. Three more guidelines were needed:
- The design had to use minimal fasteners — the fewer the better.
- The panels had to self-align when installed. We wanted perfectly smooth walls.
- The fasteners in the design had to be installed with one hand and one tool.
Back to the Drawing Board
To solve these problems, the MAD team developed a quick-connect system. This system used slots in the panels shaped like dumbbells and knobs that would insert into the slots at the top or bottom, allowing the panel to slide into place. This solution worked out well and allowed us to reduce the number of fasteners needed by more than 75%. The knobs were tapered so the panels self-centered when they were joined together. We used cage nuts, which would be inserted into parts before shipping so that mechanics would only have to install a bolt from one side, and bolts with grooved flanges so that lock washers would not be needed.
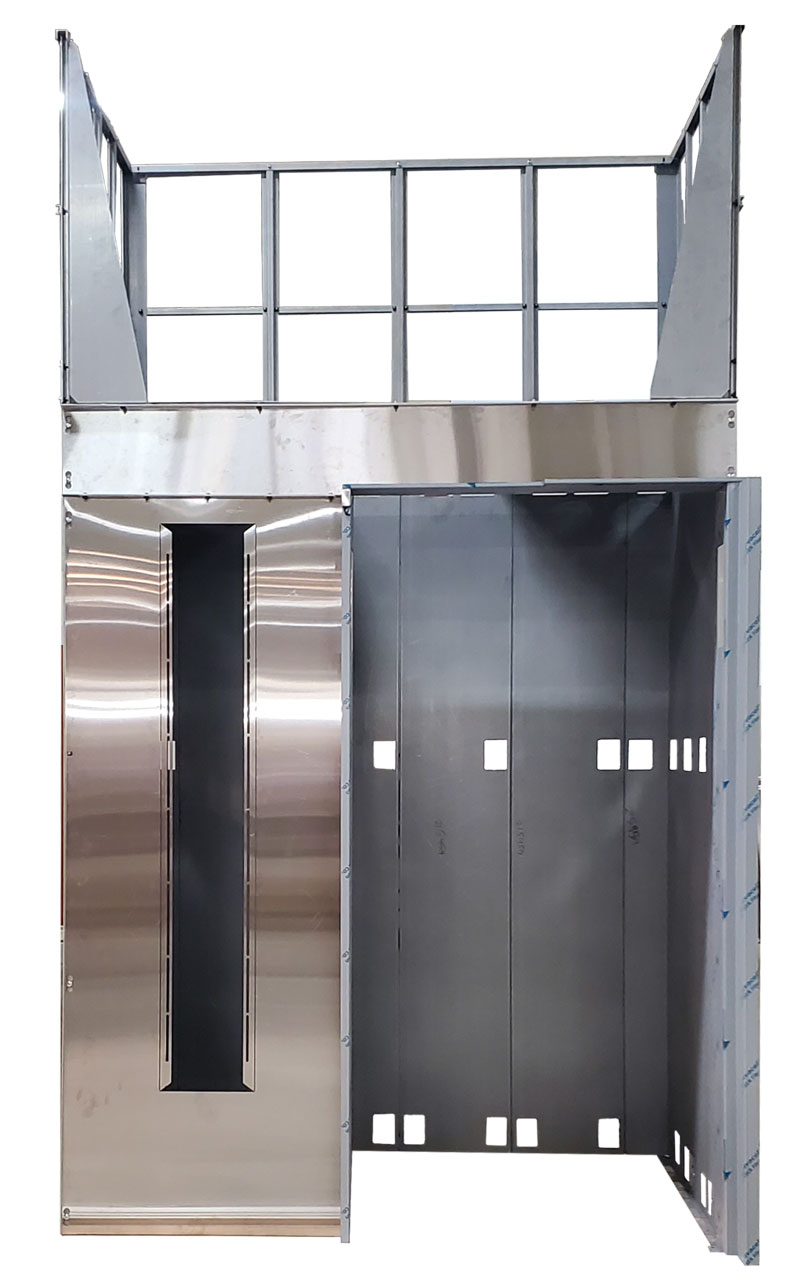
Prototype Two
The next prototype was assembled very quickly. The quick connect system worked as planned, giving us fast assembly and perfect panel alignment. Everything was great until we jointed the corners of the non-access walls. We discovered it was easy to join panels with quick connects when they were lined up on the same plane. However, it was difficult to do this in the corners where the side wall and rear wall panels were set at 90° to each other. We also found that once the walls were assembled, it was difficult to square the panels on the platform, as they were heavy once assembled. We introduced two new design guidelines:
- All panel joints had to be on the same plane.
- The design should promote self-squaring where possible.
This problem was solved by making premade corner panels. The premade corners were formed square, making the task of aligning the shell easier. Because the 90° corner was a single piece, all panel joints were on the same plane, therefore, installation in the corners would be much easier.
Prototype Three
Prototype three assembled very quickly and easily, adhering to all of the design guidelines developed to that point.
The next task was to design integrated car top rails that were very flexible to accommodate obstacles such as cross head locations and bracing. The MAD design team decided to integrate the toe guards with wall panels and canopies. To do this, the car top rail toe guards were bolted through the side walls of the shell, through the canopy and into cage nuts in the toe guards. We needed to be able to attach the canopy and sidewalls before the toe guards so it would be safe to send a mechanic on top of a canopy to install the car top rails. This problem was solved by attaching the canopy sections to the shell walls in only one location on each side of the canopy panel and at four locations on the back panel. The canopy flanges were jointed together to make the canopy strong and safe. The toe guards were modified with holes over the attach points used to join the side walls and canopy and placed over the exiting fasteners. The remaining bolts were inserted to secure the toe guards to the canopy from the platform. The rest of the car top rails and the isolators were attached to the toe guards. This allowed easy integration of all components right out of the box.
In the end, we had a solution that met all the design criteria developed through consultations with mechanics. Our final accomplishment was to incorporate all the engineering into our 3D automated engineering environment, which allows us to create drawings in a matter of minutes.
We call our solution the F1 Shell or Fast One.
- Fast pricing within 24 h
- Fast engineering within 24 h
- Fast manufacturing within four weeks
- Fast installation: Unpack the shell and install in 4 h or less
Get more of Elevator World. Sign up for our free e-newsletter.