A Prototype Robot Named “Heidi”
Jul 1, 2020
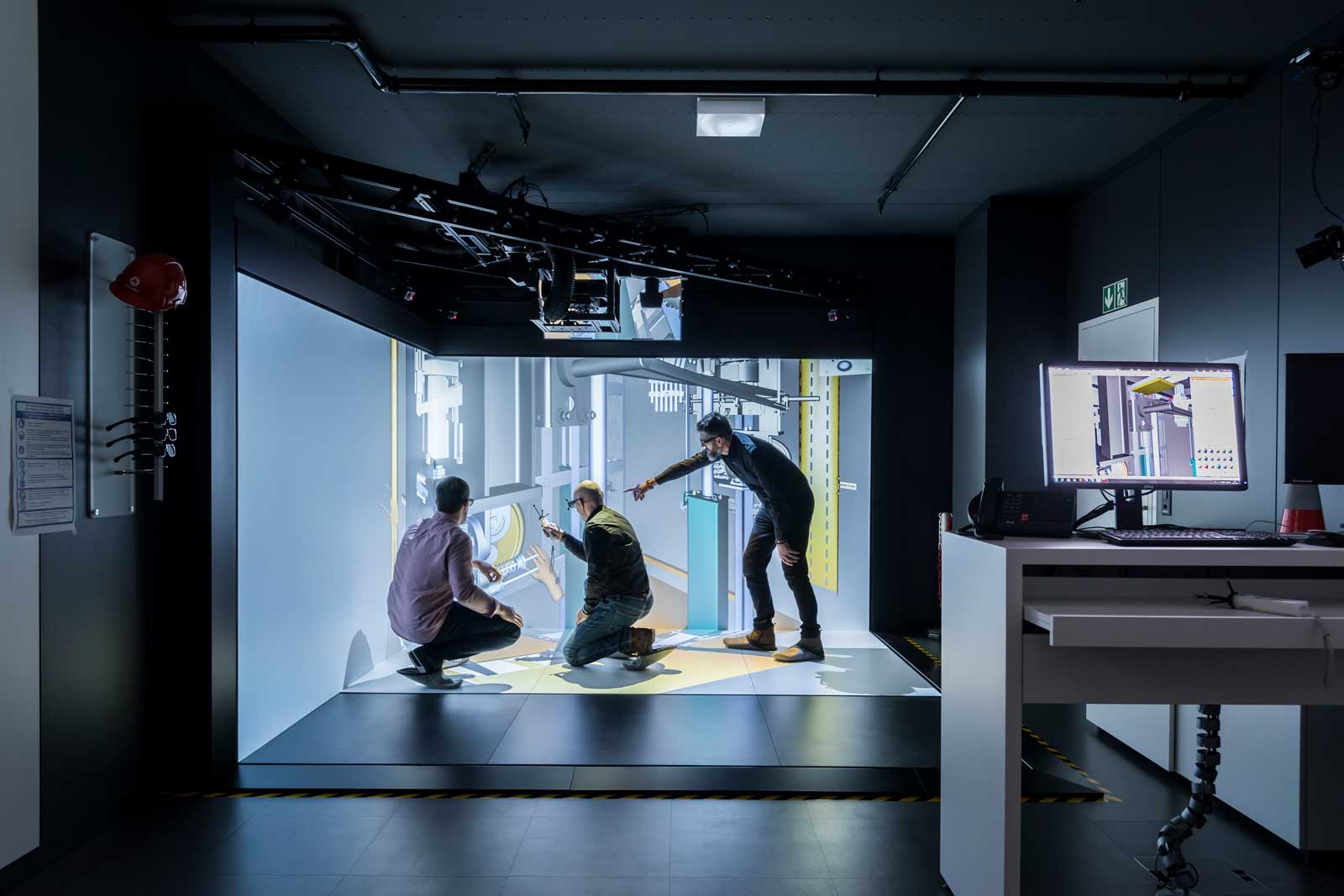
Your author learns about new technologies at Schindler.
photos courtesy of Schindler
Your author (USB) recently spoke to Christian Studer (CS) of Schindler in Switzerland about R&D at Schindler and the future of elevator technology.
USB: Please introduce yourself.
CS: I am a civil engineer with a PhD in Mechanical Engineering. I have worked for Schindler at the Ebikon headquarters, near Lucerne in Switzerland, for 12 years. I head the New Technologies department, which is part of R&D. The small group works on an interdisciplinary basis. All engineering disciplines — including software, electrical engineering, mechanical engineering, materials, robotics and artificial intelligence — are represented.
USB: What does your department do?
CS: We collect new ideas within the team and corporation, as well as from our customers and startups. We also collect ideas from universities, filtering them by megatopic, with the goal of gradually turning these ideas into long-term new or better products. For example, we maintain intensive contacts with our key accounts. We ask them, “What’s on your mind?” If the team is on the road with open eyes and ears, solutions can be found everywhere. At Ebikon, we do so-called “seed planting,” the first stage of the process in which we prove feasibility. Stage 2 is “growing,” which means developing new products or improving existing ones. Stage 3 is called “harvesting.” That involves optimizing the quality of products or production processes. Stages 2 and 3 are also carried out at other Schindler locations around the world.
USB: Could you provide a recent example?
CS: In the course of automation, we investigated the relevance of robots in elevator construction. From this, we developed our robot installation system, Schindler R.I.S.E (Robotic Installation System for Elevators). The system is for 3-m-X-2.5-m, medium-sized shafts in taller buildings. The robot has a scalable working diameter of up to 3 m and weighs almost 1 mT. We are currently building a small industrial series being tested by select customers and for business feasibility. It is too early to talk about specific figures. By the way, the project team named the first prototype of the Schindler R.I.S.E robot “Heidi.”
USB: How did you come up with the idea of using robots?
CS: Some time ago, there was an exchange between Schindler and (public-research university) ETH Zurich on robots and their relevance for elevator installations, and this was passed on to my team.
USB: How did you proceed?
CS: Robots are familiar to us, as they are used in our factories. We wanted to show the industry new potential for using robots in elevator installation. It started with the basic discussion and determination of how a robot might move in an elevator shaft. Technologies like rolling or suction robotics, as well as more adventurous ones like flying drones, were evaluated. An important criterion was the availability of a technology. An advantage is, of course, increased work safety. Another advantage of robots is they deliver constant quality of work without getting tired. This supports the elevator constructor during the installation phase. New, innovative approaches are needed in the construction industry. One approach is prefabrication and modularization. Another is robotics.
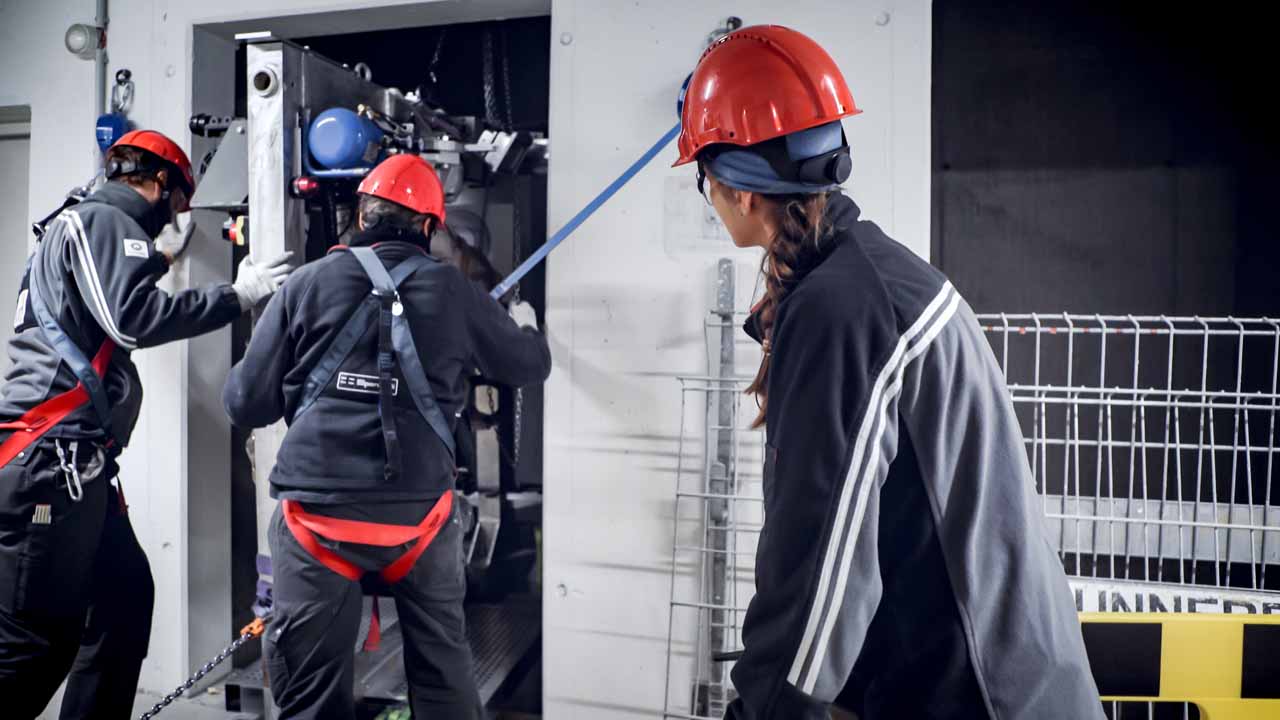
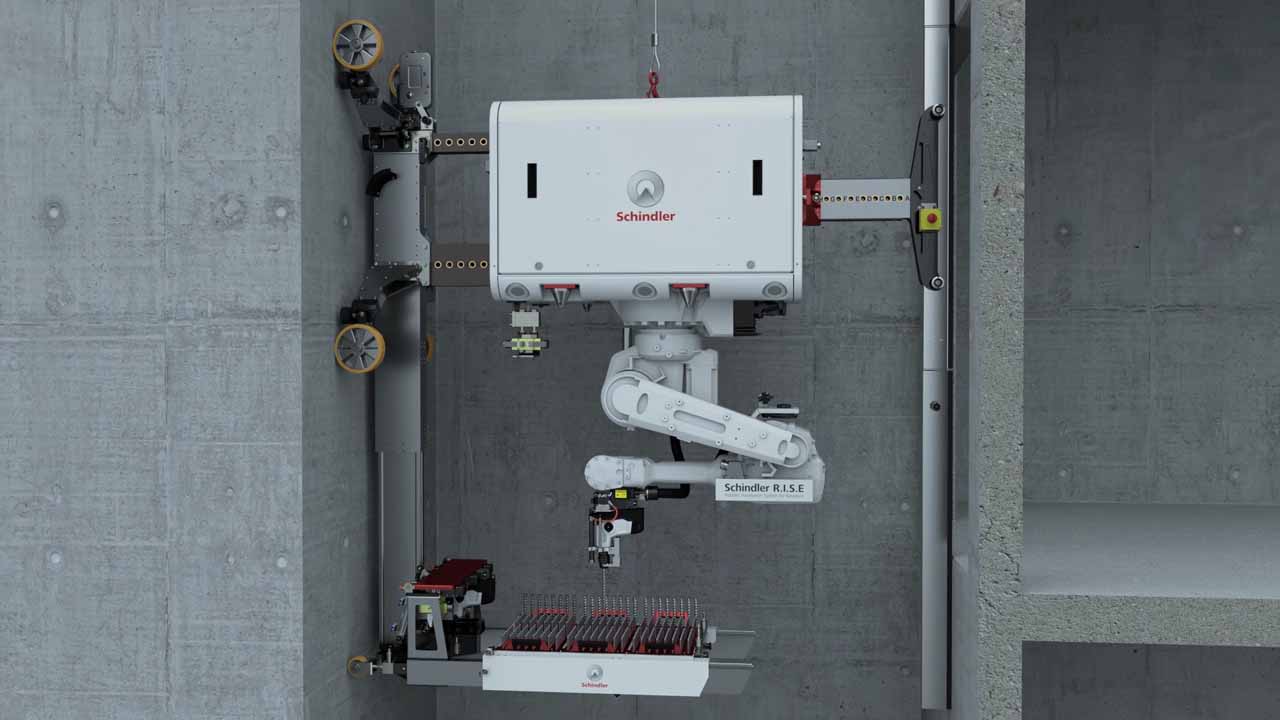
USB: What has been the outcome?
CS: The robot hangs from a winch in the machine room and climbs the shaft walls. It controls itself — for example to a 5-m-high, stable working position — and measures, among other things, its position in the shaft. It scans the walls for reinforcement bars. From this, it calculates the drilling position and drills holes for the anchor bolts of the rail fixings. Then, the installers only need to insert the rail mountings, which, in addition to enhancing project speed, increases work safety and improves installation quality. Drilling holes in the shaft walls is a dirty job, and our installers are happy to pass this on to a robot.
USB: Is more to come?
CS: Oh, yes. Our robot allows a direct connection between digital planning data and onsite construction. Today, we have all the digital planning data in the computer, but the elevator installer has to meter this data manually at the construction site. By applying the digital planning data directly to the construction site, the robot closes this gap. Furthermore, the elevator installation data are logged. In the not-too-distant future, we will insert them via building information modeling into completely digital buildings. This allows documentation during the construction phase and ensures tracking later, such as during modernization.
USB: What are examples of some of Schindler’s other innovations?
CS: Over the years, we have built a few firsts. The machine-room-less elevator, in which the motor was moved from a machine room to the shaft, was a big step. Today, we go even further and eliminate any roof superstructure by creating a“virtual space” to reduce the headroom height while maintaining employee safety. The use of belts as drives has led to smaller deflection radii and pulleys. Also, a global destination-dispatch system, PORT, originated from our company.
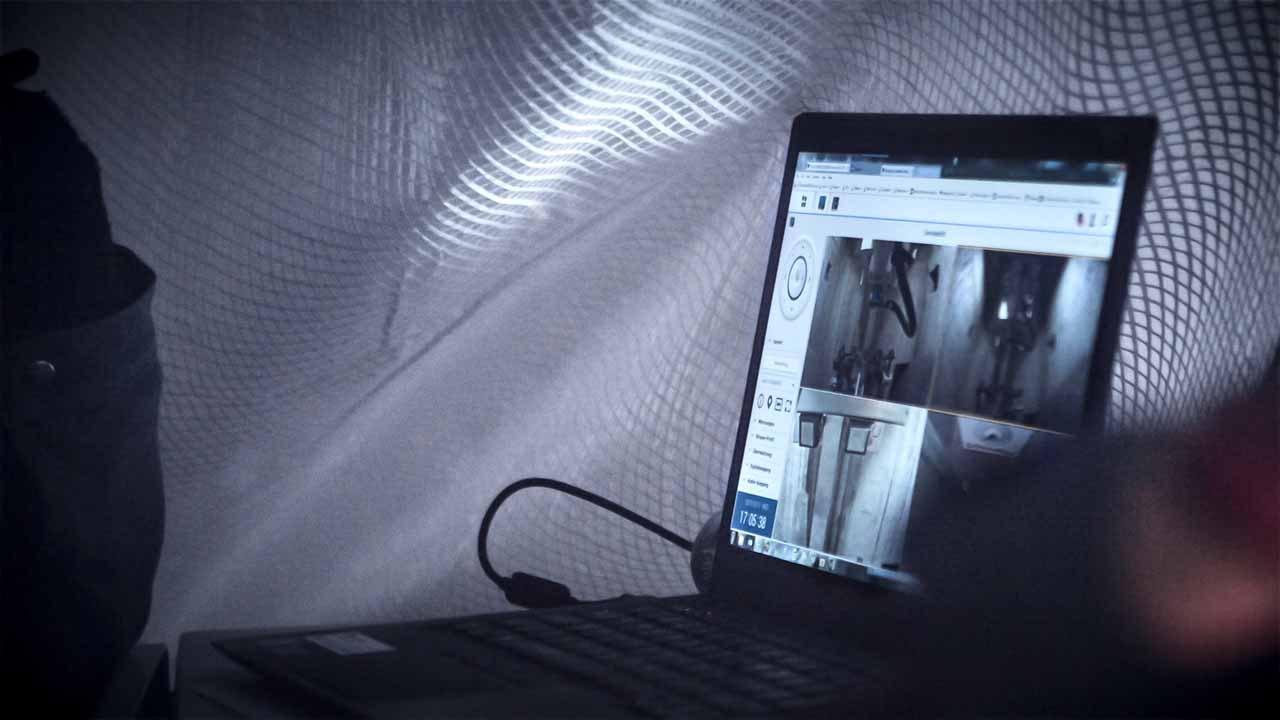
USB: On which resources can you draw?
CS: Here at Ebikon, we have our own test towers, laboratories and 3D printers for prototyping. The apprentice workshop regularly works with us to produce prototypes. Of course, we also have virtual systems, such as a “virtual cave,” the walls and floor on which an elevator shaft can be projected to anticipate, for example, the accessibility or mountability of a screw with the help of specialty glasses. And, should we miss something onsite, there are four other major R&D locations: in Shanghai; Pune, India; Randolph, New Jersey; and São Paulo, Brazil. In a globally interconnected project team, almost anything is possible.
USB: What is Schindler currently working on?
CS: Not surprisingly, the focus remains on digitalization. For example, we are investing in the simulation of elevator modules. Instead of physical tests, elevator modules or components are linked to simulation environments in so-called hardware-in-the-loop to test various configurations. Many more variants can be run through in a shorter period at low cost, which leads to even better quality.
USB: So, after the ActionBoard, Cube, AdScreen, Door Show and Smart Mirror, can we expect new features for Schindler Ahead?
CS: The connectivity of elevators will increase, and our range of associated digital services will be continuously expanded. More data will be collected, monitored and evaluated for, above all, predictive maintenance. We will also continue to expand PORT technology, as can already be seen to some extent in the OMNITURM in Frankfurt, Germany. This transit-management system tracks how people move around the building and learns traffic patterns in the process. It will recognize individual users and know their destinations. It will guide users efficiently and comfortably from the entrance to their offices by providing them with more information on the way. Using MyPORT, users will control their journey via smartphone. A further step will be the inclusion of the building doors, which will trigger the elevator call. Another application is video terminals, where you can not only call the elevator, but also talk to your visitors waiting downstairs at the building entrance.
USB: How does Schindler balance digitalization with safety and security?
CS: The topic is addressed every day and is at the highest priority level. Elevators must not be allowed to be “hacked.” Personal data must be protected. In every one of our ideas, we always assume that the question of safety and security is solved or could be solved. The implementation is then carried out at a later stage during product development.
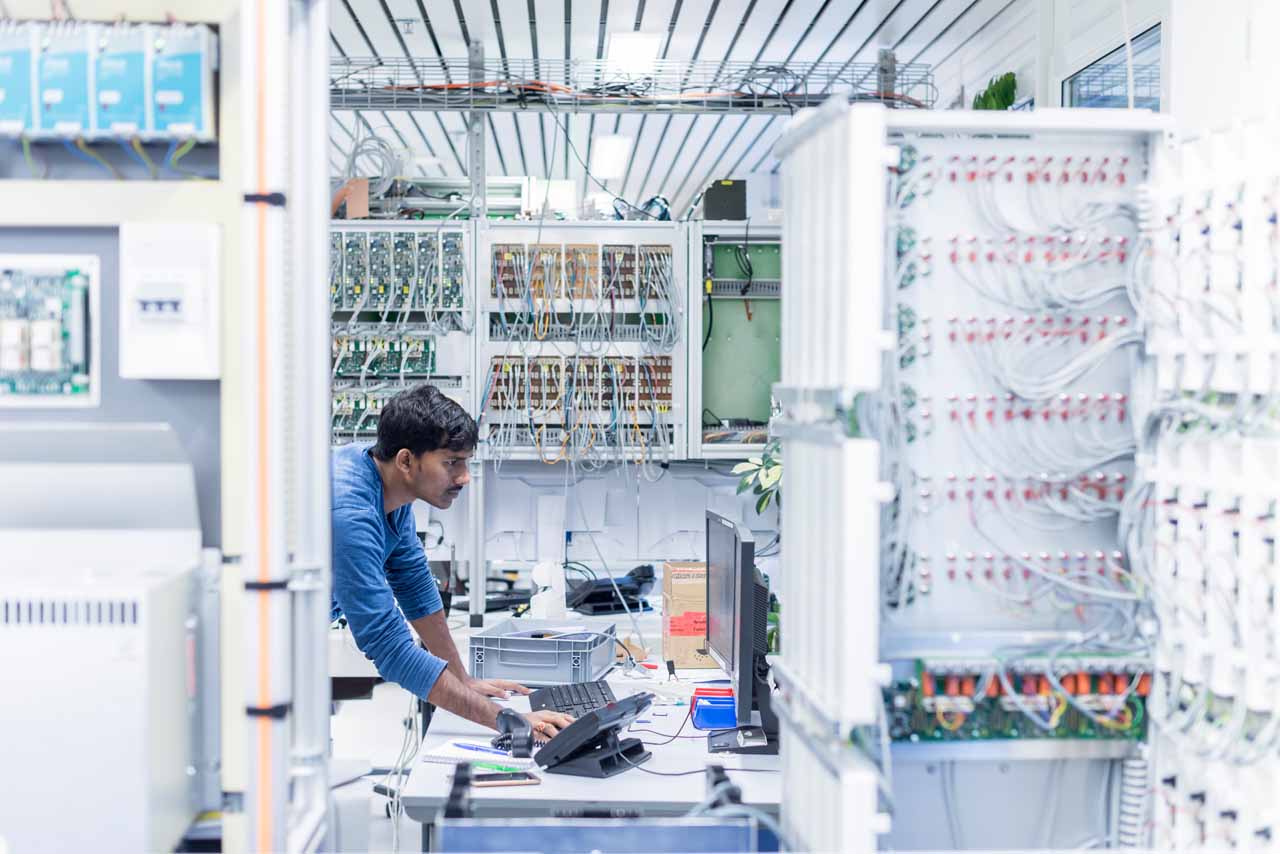
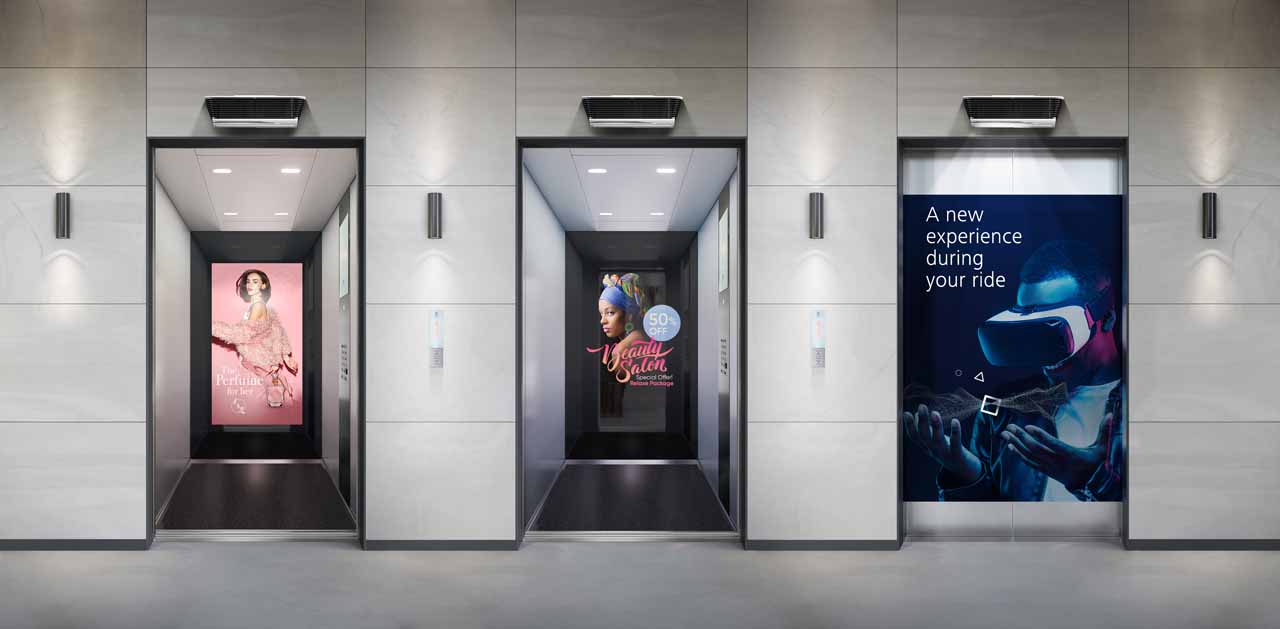
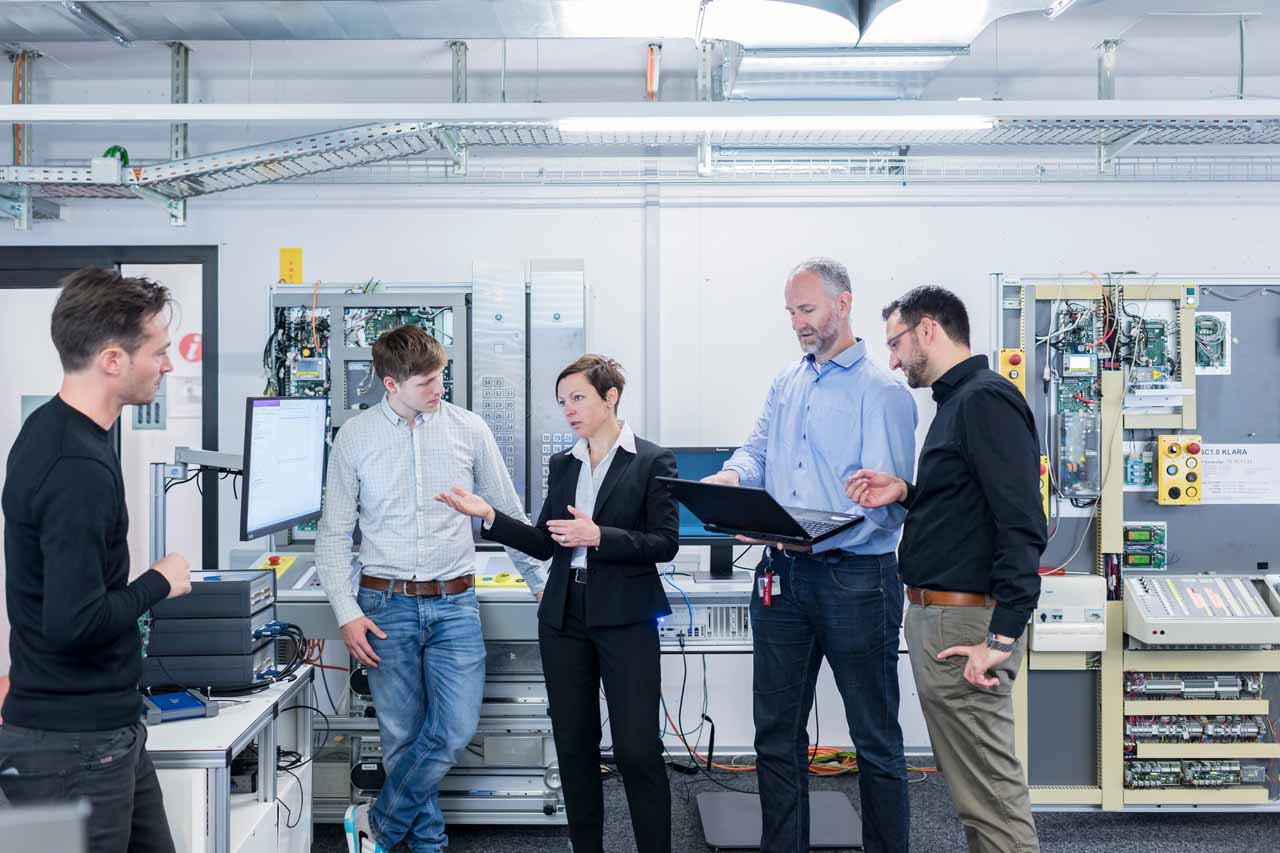
USB: What influence does sustainability have on R&D?
CS: This is a big issue with Schindler. Even though we have already made extreme optimizations in this respect in recent years, we will reduce elevators’ energy consumption even more. New materials beyond steel and new production methods will be used. The quality and, thus, long life of systems and components, is a core concern for us. All in all, we would
like to achieve a better CO² footprint.
USB: What has the effect of COVID-19 been on daily operations?
CS: This is a very special, unprecedented situation for Schindler, as it is for any other company. My team is currently working from home offices, which doesn’t make much of a difference, since we have long been digitally networking with each other worldwide. I see this as an opportunity to drive digitalization more widely and, above all, more quickly, both internally and in our products. Our infrastructure continues to function.
USB: Please complete the sentence: “I have a dream. . .”
CS: I sleep very well! But, seriously, urbanization is a worldwide trend. In 2030, 2.5 billion people will be living in megacities. I’m very concerned about how people can live there in a way that is both worth living and sustainable. Cities must not stink; they must not be dirty. There must not be congestion of cars or people. Mobility in buildings and districts must be provided. As an engineer, I would like to make a radical contribution to making these cities green and efficient. If one day my grandchildren will say to me, “You did a good job.” Then, I will be satisfied.
Get more of Elevator World. Sign up for our free e-newsletter.