Advanced Elevator Maintenance Network during a Major Seismic Disaster
Nov 1, 2012
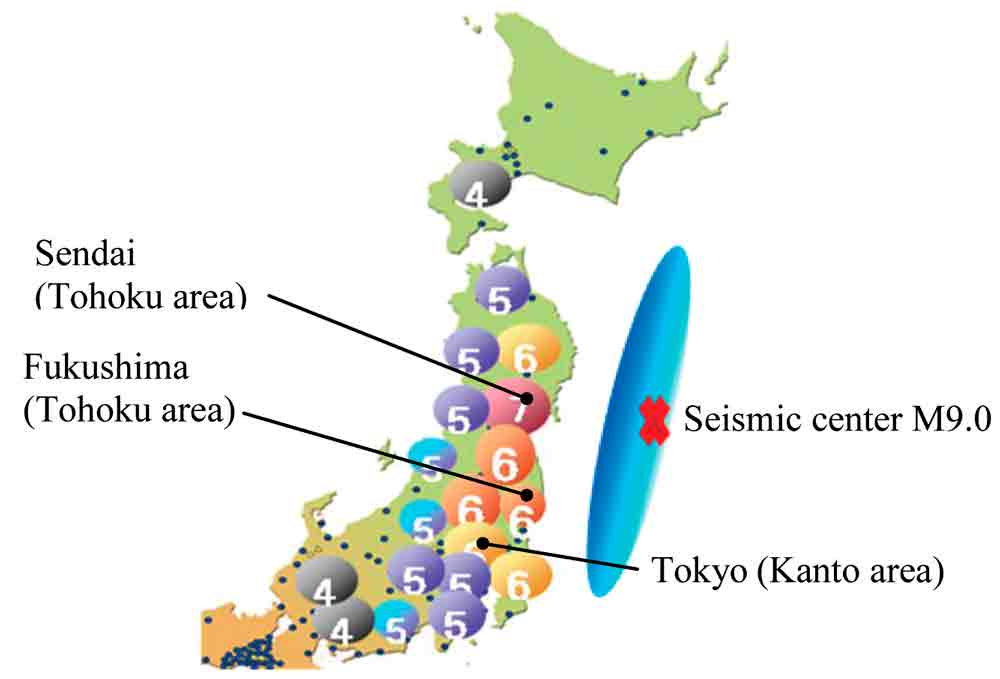
Maintenance network systems that support the restoration of elevators damaged during earthquakes
by Motoyoshi Nakamura, Yasuhiro Shibata and Kouzou Mabuchi – Hitachi Building Systems Co., Ltd., Japan
This paper was presented at
USA 2012, the International Congress on Vertical Transportation Technologies and first published in IAEE book Elevator Technology 19, edited by A. Lustig. It is a reprint with permission from the International Association of Elevator Engineers
(website: www.elevcon.com). This paper is an exact reprint and has not been edited by ELEVATOR WORLD.
Key Words: Seismic design, maintenance network, safety
Abstract
The prompt restoring at the time of an earthquake is an important work for elevator maintenance companies in Japan. To meet this mission, we have built up the powerful maintenance network systems which support the restoring work of the damaged elevators. Our maintenance network functioned well against the Great East Japan Earthquake which occurred at 2:46pm on 11th March, 2011. However, new problems appeared at the same time. Especially, avoidance of entrapment in a car resulting from the planned rolling blackout due to the shortage of electric power is important. The current situation and future work of our elevator maintenance network system are presented.
1. Introduction
Earthquakes are quite common in Japan, which requires countermeasures based on “Seismic Design and Construction Guidelines for Elevators”[1] in order to mitigate the damage to elevators during an earthquake. Elevators are equipped with a feature that safely stops the elevator during an earthquake to prevent property damage and to prevent passengers from becoming trapped inside the elevator car. At the same time, recovering elevators that have stopped because of this safety feature in a safe, prompt manner is a critical task of maintenance companies. Therefore, we have reinforced the recovery system with building the maintenance network including a human network by preparing the “Operation Manual for Major Disasters” in 1996.
The Great East Japan Earthquake of March 11, 2011, had a magnitude of 9.0, one of the largest intensity experienced in the world. The earthquake affected approximately 300,000 elevators stopped[2]. The maintenance network we established contributed to early recovery of the stopped elevators in areas other than regions where the entire social infrastructures were paralyzed. The maintenance network also functioned well against the numerous aftershocks that continued for a long time after the quake. However, new problems appeared. Lack of power initiated by the Fukushima nuclear power plant crisis was the main problem. Many passengers were trapped in elevators during the planned blackout triggered by insufficient power supply after the quake. Therefore, we developed “Remote-control parking service”, and we put the system into service in July 2011.
2. Overview Of Countermeasure Against Earthquake For Elevators In Japan
Earthquakes of intensity 5-lower[3] that may cause a large number of elevators to stop occurred at an average frequency of 8.9 times per year in Japan between 2001 through 2010[4]. For this reason, “Building Standard Law of Japan” and “Seismic Design and Construction Guidelines for Elevators” were revised by the Ministry of Land, Infrastructure, Transport and Tourism editorial supervision in 2009[1], and the establishment of “Operation for earthquake” became mandatory.
2.1 “Operation for Earthquake”
Figure 1 is a flow chart for preventing entrapment or property damage during an earthquake.
3. Development Of “Automatic Diagnosis And Recovery System For Earthquakes”
As shown in Figure 1, activation of the Low-level sensor will stop the elevator in an earthquake, but it requires recovery work by engineers. Therefore, the recovery system with automatic mechanical diagnosis had been developed not to require engineers recovery work on site. The design guidelines for this system were introduced in the 2009 “Seismic Design and Construction Guidelines for Elevators”, which recommended installation of the system[1].
3.1 Sections Diagnosed by “Automatic Diagnosis and Recovery System for Earthquakes”
Our remote diagnosis technology has been cultivated for years and is implemented in the mechanical diagnosis of components likely to be damaged by an earthquake as shown in Figure 2. Rather than using engineers, automatic diagnosis by the remote monitoring terminal enables recovery of the stopped elevators.
3.2 Operation Flow of “Automatic Diagnosis and Recovery System for Earthquakes”
Figure 3 shows the operational flow for “Automatic diagnosis and recovery system for earthquakes”. In the case of buildings with 10 stories at a height of 30 m, the system will complete the diagnosis in approximately 15 minutes and restore normal operation.
4. “Recovery Management System For Earthquake”
“Recovery management system for earthquake” is a system that recognizes the status of elevators in an earthquake and supports patrol plans for restoration and management of recovery.
4.1 Development of “Recovery Management System for Earthquakes”
“Recovery management system for earthquakes” is a system that consolidates information from remote monitoring terminals, contacts from users via phone lines, and restoration state information by maintenance tool from field engineers for recovery management. Task force share this information to enable appropriate support and information distribution to customers. Figure 4 shows the overall configuration of the maintenance network in an earthquake with information on the recovery management system for earthquakes as the core.
4.2 Screen of “Recovery Management System for Earthquake”
The system displays the status and response status of passengers trapped in a car with higher priority for response on top and enables confirmation of the response status for properties that require on-site work at the same time (see Figure 5).
5. System Operation Situation During The Great East Japan Earthquake
Approximately 300,000 elevators stopped and 207 cases of passengers trapped in cars during the Great East Japan Earthquake[2].
5.1 Operation Status of “Automatic Diagnosis and Recovery System for Earthquakes”
The total number of the elevators restored normally by “Automatic diagnosis and recovery systems for earthquakes” during this disaster was a total of 1,600 in March and April. And 65% of elevators which equipped with the system was restored temporarily in theKanto area in April when many middle-scale aftershocks hit. In a certain case, an elevator that recovered temporarily six times during March and April, which contributed to the mitigation of downtime of approximately 30 hours in comparison to recovery by engineers.
5.2 Operation Status of “Recovery Management System for Earthquakes”
Areas hit by a quake intensity of 5-upper[3] or greater was excluded from the collection areas because all seismic sensors were activated. Areas hit by a quake intensity of 5-lower[3] or less will be the focus for priority collection in “Recovery management system for earthquakes”. Therefore, the system was utilized for recovery status management only in the Tohoku area at the beginning of the quake disaster while both the affected status recognition and the recovery status management were used in the Kanto area, where the quake intensity was relatively low. This system operated non-stop for about two months in response to the many aftershocks and contributed to the on-site recovery management.
6. Approach To New Problems
Although we requested that building owners and building facility manager stop using elevators during the planned power blackouts of March as a countermeasure to the lack of power due to the Great East Japan Earthquake, 654 passengers were trapped in cars nationwide[2]. This number is more than triple that due to the earthquake.
While elevators are equipped with an automatic landing device in the event of a power failure as a feature to prevent entrapment in cars during power blackouts, the rate of application is low for old elevators. Also, operation is difficult in situations with daily blackouts, such as the planned rolling blackouts due to concern for insufficient capacity of charged batteries. Therefore, we developed a remote-control parking service that prevents entrapment in elevators by parking the elevators via remote control prior to the start of the planned blackout, and we put the system into service in July 2011.
6.1 Detail of Development of “Remote-Control Parking Service”
The remote-control service parks elevator cars by transmitting control instructions for parking to on-site remote monitoring terminals in areas of blackouts prior to the start of any planned rolling blackout in response to an announcement for a blackout from the electric power company (see Figure 7).
7. Conclusions
“Automatic diagnosis and recovery systems for earthquakes” and “Recovery management system for earthquakes” that we developed contributed to the early restoration of the elevator after the earthquake occurrence. Furthermore, “Remote-control parking service” corresponding to a new problem, such as the planned rolling blackouts, was developed. This improved capacity for responding to wide area disasters allowed us to ensure vertical transportation in buildings, which was needed by the society. This can be considered a result of the continuous organized quake disaster response and of the advances in remote monitoring technology. In the future, we support stable operation of elevators, and we continue to reinforce the maintenance network in order to fulfill the mission of a maintenance company.
8. Appendices
Intensity scale (JMA seismic intensity scale is used in this paper due to lack of international standards. For details of the scale, refer to the appendices.)[3]
Figure 1: Operation for earthquake standard flow chart (overview) Figure 2: Sections diagnosed by the automatic diagnosis and recovery system for earthquakes (machine room less elevator) Figure 3: Automatic diagnosis and recovery system for earthquakes flow chart (overview) Figure 4: Overview of overall configuration of maintenance net-work at earthquake disaster Figure 5: Screen for “Recovery manage-ment system for earthquakes” Figure 7: System configuration and time chart of “Remote-control parking service” Table 1: Operation acceleration setting for each seismic sensor Table 2: Operation acceleration value setting for high-level sensor Figure 6: Distribution of intensity in Earthquake at 14:46 on March 11 Table 4: JMA seismic intensity scale
REFERENCES
[1] Ministry of Land, Infrastructure, Transport and Tourism editorial supervision, Year 2009 “Seismic Design and Construction Guidelines for Elevators”
[2] Japan Elevator Association(JEA), Elevator Kai,No183
[3] Japan Meteorological Agency(JMA),JMA seismic intensity scale and description
[4] Japan Meteorological Agency(JMA),JMA seismic intensity database search
Get more of Elevator World. Sign up for our free e-newsletter.