Automatic Transfer Fabrication Of Special Elevators With Parametric Design Program
Jul 1, 2019
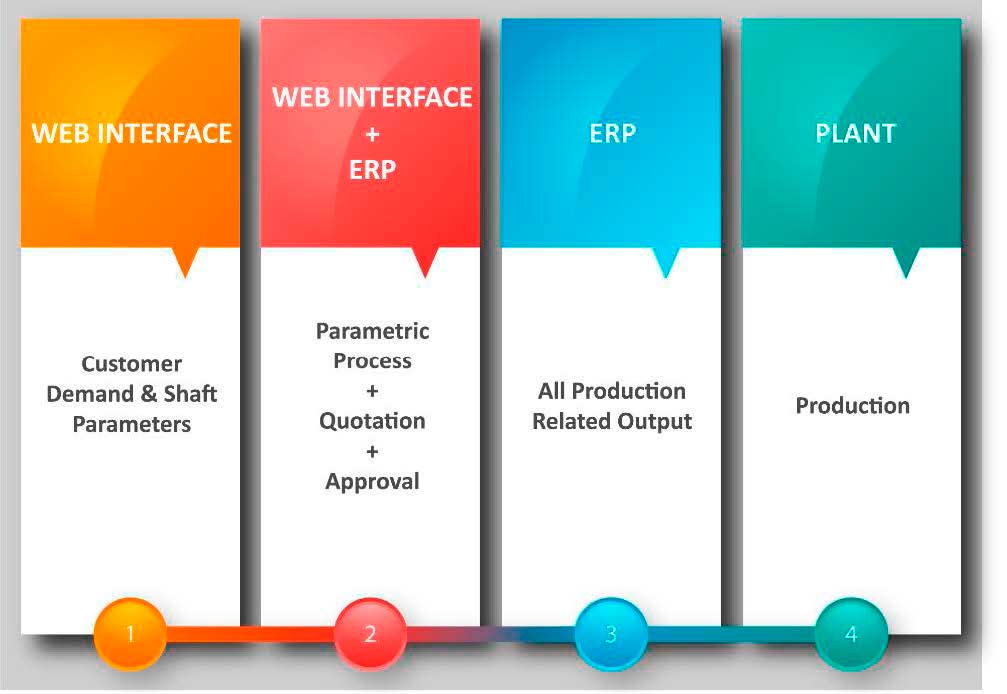
Your author describes how specialized software enhances efficiency and accuracy.
This paper was presented at ELEVCON Berlin 2018, the International Congress on Vertical Transportation Technologies, and first published in IAEE book Elevator Technology 22, edited by A. Lustig. It is a reprint with permission from the International Association of Elevator Engineers (www.elevcon.com).
Designing non-standard projects accurately, on deadline, is a considerable challenge. Furthermore, carrying the project through to production requires excessive manpower and time. It is an error-prone activity. These issues are solved by automatic transfer of elevator designs to production via parametric design software (Autodesk Inventor® and Autodesk Configurator 360TM). With the help of this software, elevators can be designed with any required parameters. Once the design is approved by the customer, it is automatically transferred to production instantly and error free.
Introduction
We live in a fast-paced world. The growing construction industry and increasing number of residential and business developments play major roles in this rapid environment. While this growth is an advantage for the elevator industry, it also creates a bottleneck for manufacturers. Deadlines, safety requirements (which, hopefully, are being adhered to more and more) and various other factors are tightening this bottleneck. We see this parametric system as one of the most reliable and important solutions for coping with tight schedules.
Parametric System — The Process
Once an order for an elevator has been placed, the parameters are transferred from parametric software to enterprise resource planning (ERP) business-process-management software via a web interface.
Customers can select their own parameters and generate whole systems at once. For this process, a login will be required with dedicated customer credentials. The web client is designed to warn and stop the customer from making critical functional errors. The only possible error is a customer entering wrong shaft details such as wrong dimensions.
Web Interface and ERP Software Communication
Following customer entries through the web client, all data is passed to the ERP software. Quotations regarding the desired project are automatically submitted to the customer for evaluation. At that stage, once the customer gives his or her approval, he or she also places the order. With the approval given and order placed, all parameters from the web client are transferred to the factory side.
After approval is given, the web client alerts the factory and makes necessary acknowledgments regarding creation of the new project and customer approval. Now being aware of the new order, the user/operator at the factory starts working on the project just by recalling the parameters.
Autodesk Inventor generates the system with the given parameters as required by the customer. Following the generation, the necessary information flows back to the ERP software.
ERP Software
ERP software now has the data that allows it to create all production-related output, such as purchase orders, production orders and weekly planning schedules. Technical drawings related to production are also exported to ERP for reference.
Production
At this final step, production is ready to receive all necessary information and descriptions to start the manufacturing process. Transfer of related data, such as cutting and bending work orders, is handled, again, by the system itself. System-generated documents are passed/uploaded to related personnel and/or equipment.
For each project, all work-order data is always available and stored in a structured folder tree. This includes the year, week and unique customer preferences. The folder structure is created mutually by the web client and Autodesk Inventor on a term and unique customer reference basis without human interference.
Conclusion
The above processes and tools ensure an error-free production phase and save time and personnel. They also help reserve R&D and engineering staff for more productive and innovative efforts. Keeping up with the technological improvements and complying with standards are other benefits we can derive from the parametric system when it comes to design and manufacturing activities. It is also worth mentioning that a parametric design system will help meet deadlines, as it provides huge efficiencies and saves time. This lends itself to increasing manufacturers’ credibility from the customer perspective.
Liftkeeper
Liftkeeper is an elevator service management system designed specifically for the elevator service industry. Liftkeeper helps companies become organized, digitized, and efficient in dispatching, sales, maintenance, job and route management, billing, purchase orders, and more. Liftkeeper will impress you with its field employee access.
Our service works on any smartphone; iPhone / Android / Windows / tablet / or other smartphone.
Liftkeeper records time tickets on site, takes signatures from customers (utilizing touchscreens), attaches pictures of equipment, vandalism, or broken pushbuttons, and automatically emails a PDF of the site visit report to customers.
In just a few clicks, accomplish everything from proposals to jobs to invoicing. There is no need to re-type anything. Liftkeeper creates invoices from a billable trouble call in seconds—including all the information from each work ticket. Liftkeeper also processes field recommendations into proposals or jobs without ever touching a piece of paper.
The customer portal option gives customers access to their own maintenance and trouble call history. This allows them to retrieve copies of time tickets and picture attachments. Additionally, this provides them the capability to monitor maintenance performance on a map listing each elevator’s maintenance status.
eMCP
eMCP, LLC is a Maintenance Control Program supply company, providing a Code compliant, turnkey, and transparent maintenance method using electronic mobile devices such as smartphones and tablets for recording task completion in near real time. Data is immediately available on dedicated login and password protected web portals for review on any web browser. Currently, eMCP provides MCPs for over 3,000 units in the U.S. and Canada. The premise of eMCP is simple – the work needed to ensure long life and safe operation can be identified and customers will gratefully pay if the work is performed and can be verified. Contractors benefit from fair compensation and a new tool to manage technicians; technicians benefit by having adequate time and direction to complete their work, and owners receive superior maintenance and capital protection.
eMCP is a turnkey Maintenance Control Program solution that is the answer for Contractors being asked by AHJs to provide and show Code compliance, for Consultants who want to make significant changes to the performance of maintenance companies for the units in their care, and Owners who want transparency, accountability, and maximum life of their capital investments.
Get more of Elevator World. Sign up for our free e-newsletter.