Columbia Elevator Sees Increasing Cab and Entrance Production
Jul 1, 2013
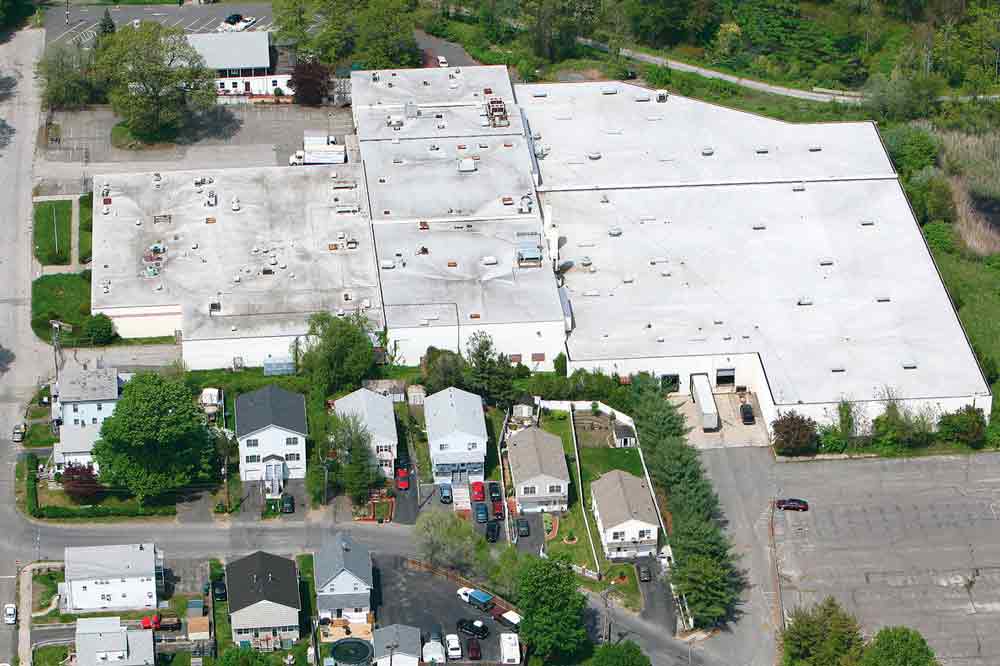
Demand for elevator cabs and entrances is on the rise, both for new equipment and modernization, according to Louis “L.J.” Blaiotta, Jr., president of Columbia Elevator. “In recent years, the trend among building owners has been to freshen their lobbies and elevators, while putting off more extensive renovations until hopefully better times,” Blaiotta said. “Now, we’re seeing the beginnings of change in the marketplace. With the economy starting to turn, and an environment in which states are increasingly receiving federal funds for new construction, we’re seeing more new buildings that require new equipment.” Blaiotta also believes that with new structures, owners of existing buildings are upgrading their elevators to enhance tenant acquisition/retention and property values. “Since we service both sectors, this is proving to be a win/win for us,” Blaiotta added.
This optimism is reflective of an apparent current trend in the elevator industry, and according to Blaiotta:
“We have access to market research showing the total amount of new elevator systems installed per year. In the 2007-2008 period, installations nationwide were at the rate of 26,000-27,000 per year. But, during the next 12-18 months, it dropped by more than half, which had a devastating impact on the industry. Our calculations point to a market bottom in late 2010-early 2011, from which we have seen a slow but steady recovery. In 2012, we saw it rise to about 15,000 systems, and for 2013, it looks as if it will increase modestly, to perhaps 16,000. It is my belief that 18,000-20,000 is where we really should be for sustainable growth, but it is good to see that we’re trending in that direction. However, the more-than 26,000 we saw five years ago was a bubble, something we’re unlikely to see again anytime soon.”
Blaiotta’s optimism is based on other factors:
“As of late, we are seeing jobs that were quoted one, two and even three years ago now turning into firm orders. The type of work is also slowly changing back to what the industry was accustomed to prior to the collapse. We are benefiting from seeing more private sector money flowing back into new construction, compared with mostly public sector, stimulus-related funding that favored the OEMs. Those big companies were much more able to secure the bonding required for the massive publicly funded, job-generating projects in the energy, medical and municipal sectors, for which many of the smaller independent contractors could not effectively compete. Now, we’re seeing many more projects that are easily within the reach of our traditional client base.”
To address this increasing demand, Columbia has been adding several new employees per month and upgrading its flagship Bridgeport, Connecticut, facility. “We’re amidst knocking down interior walls to accommodate incoming new paint-line ovens and other equipment to increase and expedite production,” said Blaiotta. “With this, plus our other manufacturing facilities in Miami, Florida, and Winfield, Kansas, we are positioned to service the increased production and distribution needs being mandated by today’s marketplace.”
On the new-construction side, one of Columbia’s most in-demand products has been its proprietary QuikEnt®II entrance system. Blaiotta says the product has been strategically engineered with three primary considerations in mind: to save on installation labor, provide the utmost in safety and deliver at competitive pricing. Blaiotta continued:
“These entrances stack on top of one another in the shaftway, support their own weight, and, for the greatest flexibility, can be used in hydraulic or traction installations, and in drywall or masonry applications. Plus, as with all Columbia entrances, they are Underwriters Laboratories® (UL) labeled. We’re gratified that QuikEnt has been selected for some of the finest buildings going up today, including, in Manhattan, {New York] 1717 Broadway, World Trade Center Towers 3 and 4, 432 Park Avenue and 56 Leonard Street, and 29 Flatbush Avenue in Brooklyn, the Ritz Carlton in Toronto, 516 North Lake Shore Drive in Chicago, 650 Newport Beach in California, and the Devon Tower in Oklahoma City. Devon is the tallest building west of the Mississippi River and 432 Park Avenue is being marketed as offering the highest habitable space in Manhattan. A residential high rise, the Lake Shore Drive building reflects the recovery of the high-rise housing sector.”
For the cab-interior modification marketplace, Columbia provides its exclusive XChangaCab® (XCC) solution to upgrade the aesthetics of an elevator interior with minimal downtime and no compromise in safety and code compliance. These, too, are UL labeled, as are all Columbia cabs (ELEVATOR WORLD, September 2012).
According to Grace Y. Greco, Columbia’s Marketing manager and Northeast account executive:
“XCC just makes it easy. It’s easy for our customers to get a price, by phone or using our website. XCC is easy to install, with the cab and ceiling installation usually complete in about 12 team hours. With such low downtime, building owners can obtain a completely new, upgraded look in record time. Design options are virtually unlimited, with our customers able to select any standard materials, such as Wilsonart, Pionite®, Formica® laminate, textured metals and real wood veneers, with standard or custom designs available.”
Due to the demand driven by the improving economy and competition from more new buildings, interest in XCC among existing building owners is increasing. Greco explained:
“The end user wants to know the easiest, most economical way to change the high-visibility, interior components of the cab: the panels, handrail and ceiling. When sales representatives are hit with their customers’ requests to ‘instantly’ make their cabs ‘brighter, more colorful, more classy, generally more attractive,’ we at Columbia are ready with an immediate solution.”
“It is certainly not the boom times of the past, but, right now, we are pleased with and prepared for the growth in demand we are seeing in 2013,” Blaiotta said.
Get more of Elevator World. Sign up for our free e-newsletter.