Escalators and Moving Walks for Amsterdam’s North-South Metro Line
Aug 1, 2019
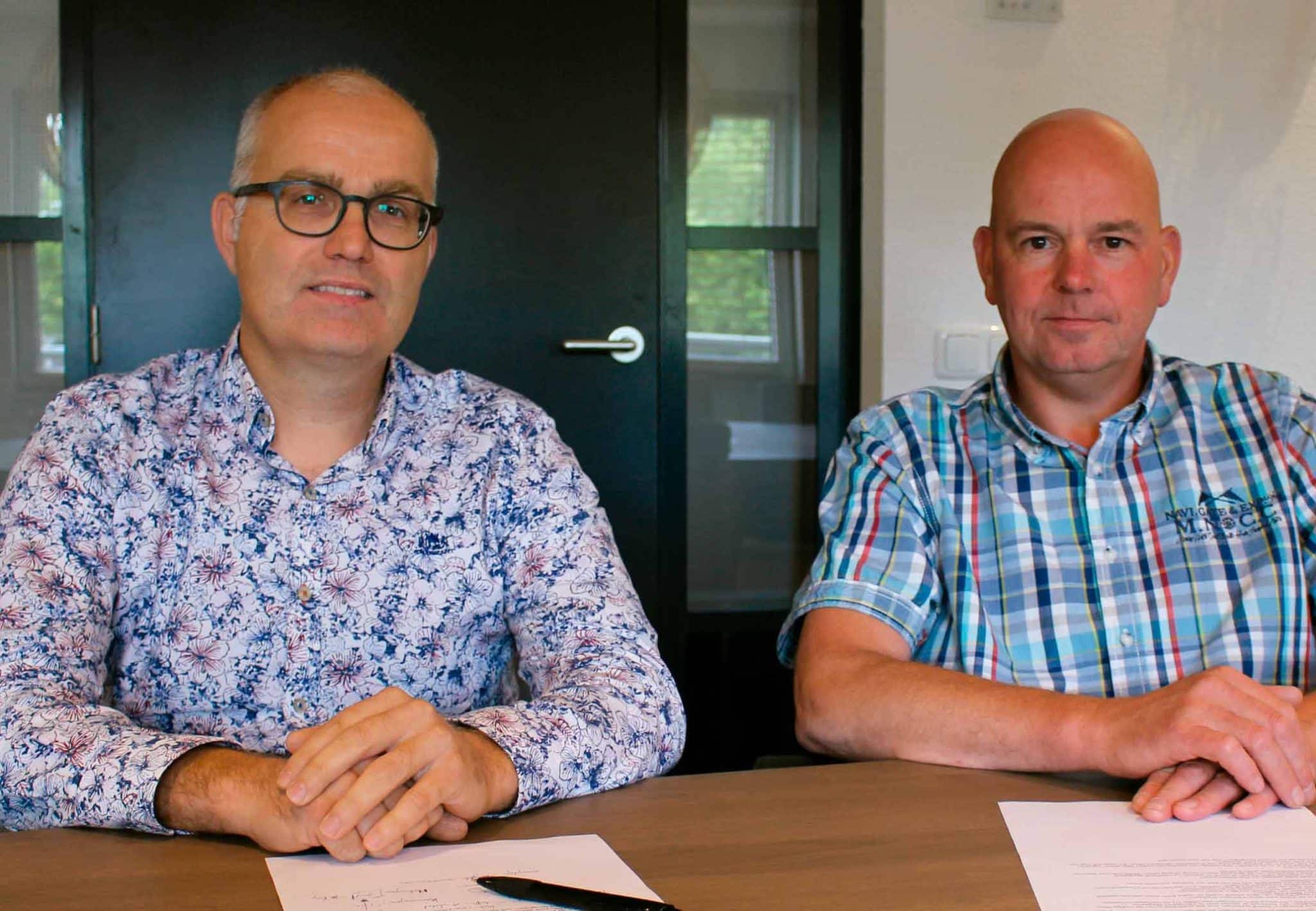
Liftinstituut demonstrates high-energy-performance requirement of thyssenkrupp escalators based on a series of measurements.
The North-South metro line in Amsterdam, which has many lifts, escalators and moving walks, recently began service. Liftinstituut carried out energy-performance-certificate (EPC) measurements and commissioning tests for all 91 escalators and the four moving walks. Your author talked about the measurements with Harry Beukeveld, project manager for escalators at thyssenkrupp, which held the contract for the project. He also spoke with Carl van den Einden, product manager for machines at Netherlands- based Notified Body (NB) Liftinstituut, who is in charge of the technical operations involving these measurements.
The municipality of Amsterdam had requested the measurements in its specification for the project. Beukeveld explained they are:
“. . . related to the energy performance of the installations and specify that the maximum total energy consumption of the escalatorsand moving walks was allowed to be 1,500 MWh. If this were achieved, the structural contractor would get a substantial discount on the contract total. Our factory had to demonstrate this to the contractor beforehand based on calculations regarding the energy performance for the escalators and moving walks. These calculations later proved achievable in practice, too. The energy consumption ended up even a little lower than the consumption calculated.”
Beukeveld is proud that:
“This is the highest energy performance level achievable with the current state of the art, although we might have been able to save another 8 or 9 MWh. However, at a certain point, we stopped measuring, as we had met the requirement. All 27 lifts achieved energy label A in the measurements, as well.”
Basis for the Measurements
While Liftinstituut received instruction for the EPC measurements in 2015, work started in October 2017. The basis for these measurements was standard ISO/DIS 25745-1:2008.
Meanwhile, an update of it had been published, but the specification dated back to 2011.
Therefore, the 2008 version applied, which stipulated the escalators had to be in operation for some 800 h before the measurements were taken. All measurements were carried out on empty upward-moving installations. The duration for each energy level measurement was 5 min. Van den Einden explained: “We then converted the results to 60 min, then multiplied this figure by 20 (20 operating hours per day) and again by 365 (365 days per year). For 91 escalators and four moving walks, the results came to 1,498.3 MWh — so, nicely below the 1,500 MWh stipulated.”
A Few Adjustments Required
Asked whether thyssenkrupp had made any adjustments to the standard-traffic escalators to reach a lower energy consumption, Beukeveld indicated each escalator is provided with a full-load frequency converter. This device is suitable for starting and stopping the escalators while fully loaded. As a full-load frequency converter has been developed further than a regular frequency converter, its energy consumption is very low.
The emergency escalators have a “slow stop” switch system, so that, in the event of an emergency, they will slowly come to a halt when there are people on them. This will minimize the chance of people falling, and the nonmoving escalator can then be used as an escape route. All escalators are provided with energy-efficient switch systems, too, reducing their speed from 0.65 to 0.2 m/s when there are no people on them. This saves power while they are not being used. The escalators are only turned off at night. Furthermore, the skirt band lighting is not switched through the escalator but is switched on and off remotely. However, it still operates as lighting in emergencies, as it is connected to the metro building’s uninterruptible power supply (UPS). This UPS is an emergency power supply with several large batteries that kicks in when voltage shuts down in the event of a power failure. Due to the connection to the UPS, skirt band lighting stays on for another two hours.
“This is the highest energy performance level achievable with the current state of the art.” — Harry Beukeveld, project manager for escalators at thyssenkrupp
Challenge
Van den Einden remarked that this was Liftinstituut’s first large-scale EPC measuring project for escalators. “So, it was quite a challenge,” he said. “In total, 130 measurements were carried out.” Beukeveld was convinced from the start that the measuring results would be positive:
“As I knew about this specification requirement, I had already arranged for a number of escalators to be measured in the factory during a factory assessment test. The client attended this a number of times, too. The results were really favorable.”
Execution
All measurements were carried out by Roy Bahadoer, product specialist for escalators at Liftinstituut. Van den Einden indicated why:
“Bahadoer has a lot of experience with this and is familiar with all the ins and outs. From time to time, his planning needed tweaking, but, thanks to the operational support from Liftinstituut colleague Marian Kool, it was possible to get his availability every time.”
Beukeveld is also happy that all the measurements were carried out by Bahadoer, noting, “Sometimes he had to work really long days, but he was always flexible and on time. It was also good to have just one point of contact.” Beukeveld is also pleased with the support received from Liftinstituut with respect to structural issues and risk analyses, commenting, “It was definitely an advantage to work together with an NB.”
Looking Back
Beukeveld looks back on the North-South Line project with pride:
“This project has been a true technical highlight, not just for us, but for our subcontractor Mulder Montage, too. Compared with large metro stations abroad, this has only been a small project, but by Dutch standards, it has been a huge project — and not always easy, either. In particular, De Pijp Metro Station, with two lines superimposed, was a technical challenge. As many as 60 lifting lugs were required to install just one escalator here. This was complicated further by the fact that no external machine rooms were possible near the escalators, as the design did not enable this; the control cabinet had to be located in the turnaround area. Luckily, a few design issues were ironed out over time, and some deviations were allowed, although it took a fair amount of time and effort to get there. But, the end result is stunning.”
Van den Einden also feels positive in retrospect and is impressed by the way the stations look, remarking, “It is a clever construction and a major technical achievement.”
Get more of Elevator World. Sign up for our free e-newsletter.