Kleemann Energy-Efficient Elevator Study
Apr 1, 2012
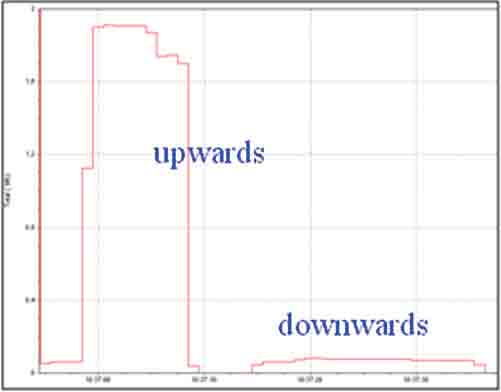
Highlights the actions Kleemann has taken to reduce energy consumption in hydraulic and traction elevators, while analyzing energy-reduction measures and results
In recent years, there has been a growing trend to consider the environmental aspects of new elevator designs, making them more efficient and environmentally friendly. The purpose of this article is to highlight the actions Kleemann has taken regarding the reduction of energy consumption in hydraulic and traction elevators, while presenting and analyzing energy-reduction measures and results. The article also focuses on the influence various systems have on elevator energy consumption.
An Increase in Energy-Efficient Elevators
Limited natural resources combined with increased energy demands have led to a global focus on environmental issues. Carbon-footprint studies, low-consumption cars, energy classes for home appliances, building efficiency rating systems and expansion of renewable energy resources are a few examples of the “green” movement. Furthermore, recent global legislation provisions attempt to reduce the energy consumption of the building sector. However, no such legislation provisions exist for elevators, though the elevator community has a shared interest, with a focus on energy consumption during elevator operation. Many elevator manufacturers have presented “green” products equipped with features for energy reduction during elevator travel and idling.
Until now, the elevator industry has focused on energy consumption during elevator operation, ignoring the unit’s total environmental footprint due to the principal interest of the final customer. However, the entire lifecycle must be taken into account.
Legislation and Normative Activities
No direct European legislation covering ecological issues in elevators exists. The Directive for Energy Performance of Buildings (2002/91/EC) and Energy Relating Products Directive (2010/31/EC) are the most relevant legislations, though, at this time, do not include elevators in their scope. There are also several normative activities regarding elevator energy efficiency. At the international level, ISO EN 25745-1/2 standards dealing with energy measurements and classification of elevators are under development. At the moment, the most prevalent standard is VDI 4707-1, which provides a method for energy classification in the “A” to “G” range (Figure 1).
Elevator Energy Reduction at Kleemann
Kleemann energy-reduction research is carried out through a collaboration of R&D and Research and Innovation departments. Research began in 2005 with a focus on traction and hydraulic elevators. To estimate energy savings from several actions, two models, a hydraulic and traction elevator, were initially measured. The basic specifications of those models were:
Hydraulic elevator acting indirectly | Geared traction elevator |
Rated load: 630 kg | 750 kg |
Travel: 6.2 m | 55 m |
Rated speed: 0.63 mps | 1.6 mps |
A typical hydraulic-elevator energy diagram is shown in Figure 2. In down movement, energy consumption is low, as the motor is not in operation during descent.
Results from the hydraulic model measurements:
- Energy consumption during a reference cycle (up and down with empty car): 58 Wh
- Standby power: 53 W
A typical energy diagram for a traction elevator is shown in Figure 3. In down movement, the energy consumed is higher, as there is a counterweight. The measurement was performed with an empty car.
Results from the traction model measurements:
- Energy consumption during a reference cycle (up and down with empty car): 135 Wh
- Standby power: 76 W
Hydraulic Elevator: Car and Frame Design
Without a counterweight, it is important to minimize dead weight to reduce energy consumption during up movement. In our test model, we redesigned the car and car frame to achieve a 9% weight reduction (from 650 to 590 kg).
New measurement results:
- Energy consumption during a reference cycle: 51 Wh
- Previous measurement: 58 Wh (12% reduction)
Hydraulic Elevator: Inverter Drive
By using an inverter to control motor operation during up movement, the hydraulic bypass function is avoided. Therefore, oil pumping is limited to what is necessary, resulting in reduced motor operation.
New measurement results:
- Energy consumption during a reference cycle: 37 Wh
- Previous measurement: 51 Wh (27.5% reduction)
It is important to note that the inverter results in an increase in total standby consumption. In our measurement, standby power increased from 53 to 85 W. Therefore, it is important to examine the necessity of inverter usage or find ways to shut down the inverter when the elevator is idle.
Hydraulic Elevator: Balancing Weight
Using a balancing weight, as shown in Figure 4, leads to significant energy reduction when the car is moving up. The balancing weight is limited to ensure minimum pressure of no less than 12 to 13 bars.
New measurement results:
- Energy consumption during a reference cycle: 22 Wh
- Previous measurement: 37 Wh (40% reduction)
Traction Elevator: Gearless/VVVF Instead of Geared Machines
It is widely known that the use of gearless machines can improve elevator efficiency, since the gear has a low efficiency ratio. Furthermore, the variable-voltage, variable-frequency (VVVF) drive leads to reduced motor losses and starting currents, and a near-unity power factor throughout the speed range.
The results are indicative:
Geared machine/AC2
- Energy consumption during a reference cycle: 135 Wh
- Standby power: 76 W
- Gearless machine/VVVF
- Energy consumption during a reference cycle: 73 Wh
- Standby power: 113 W
Energy reduction during the reference cycle: 45%
Traction Elevator
The type of car sling (central or cantilevered), partnered with the friction coefficient of guided shoes, plays an important role in total shaft efficiency. “L”-shaped car frames with guide shoes having a friction coefficient of 0.3 could increase the out-of-balance load by up to 70% (Figure 5).
Traction Elevator: Regenerative Drive
A regenerative drive can provide significant energy reduction, especially in buildings with intensive use. Still, elevator designers must take into account the regenerative device’s own energy consumption.
- Energy measurements of the traction model equipped with a regeneration unit:
- Energy consumption during a reference cycle: 51 Wh
- Standby power: 248 Wh
Previous measurement: 73 Wh (30.1% reduction)
Hydraulic and Traction Elevators: Efficient Car Lighting
Using LEDs instead of incandescent lamps for car lighting saves up to 90 W during car movement.
The reference cycle duration of a test model could be 30-60 s. Therefore, the relevant reduction in one cycle is low.
Lamp type | Luminous efficiency |
Incandescent | 10-18 W |
Halogen incandescent | 15-20 W |
Compact fluorescent | 35-60 W |
Linear fluorescent | 50-100 W |
LEDs | 30-150 W |
Hydraulic and Traction Elevators: Standby Consumption
Standby consumption plays a role in total elevator energy consumption, especially when the elevator is operated in residential buildings, as shown in Figure 6. Therefore, it is critical to reduce standby consumption after a specific idle time. In this case, the controller and inverter (if any) are put in low energy-consumption mode, with car and landing displays turned off and automatic doors in standby mode (sets the motor out of service).
Actions/steps | Energy consumption during a reference cycle | Standby power |
Conventional hydraulic elevator | 58 Wh | 53 W |
9% reduction of car and frame weight | 51 Wh | 53 W |
Use of an inverter for motor control | 37 Wh | 85 W |
Use of a balancing weight | 22 Wh | 85 W |
Use of controller with standby function | 22 Wh | 25 W |
Energy reduction | 60% | 52% |
Actions/steps | Energy consumption during a reference cycle | Standby power |
Geared/AC2 traction elevator | 135 Wh | 76 W |
Gearless/VVVF traction elevator | 73 Wh | 113 W |
Use of guide shoes with a coefficient factor of 0.1 instead of 0.3 | (Reduce the out of balance load 10%) | N/A |
Use of a regenerative drive | 51 Wh | 248 W |
Use of a controller with standby function | 51 Wh | 42 W |
Energy reduction | 62% | 44% |
Summary
For the hydraulic model with a rated load of 630 kg, travel of 6.2 m, three stops and a rated speed of 0.63 mps, Table 1 gives the energy reduction regarding every energy-saving action:
Table 2 shows the traction test model with a 750-kg rated load, 55 m travel, 18 stops and rated speed of 1.6 mps:
Conclusion
Potential energy savings relating to ride and standby energy demand of elevators exist. Since 2005, Kleemann has extensively researched elevator energy reduction. This research has led to significant energy consumption reductions during ride and standby. Until now, the elevator industry has primarily focused on energy consumed during elevator operation. However, a full-lifecycle assessment could provide a complete picture of the carbon footprint of elevators.
Get more of Elevator World. Sign up for our free e-newsletter.