The Use of IoT Technology to Enable Earlier Identification and Monitoring of Faults on Lifts
Jan 1, 2021
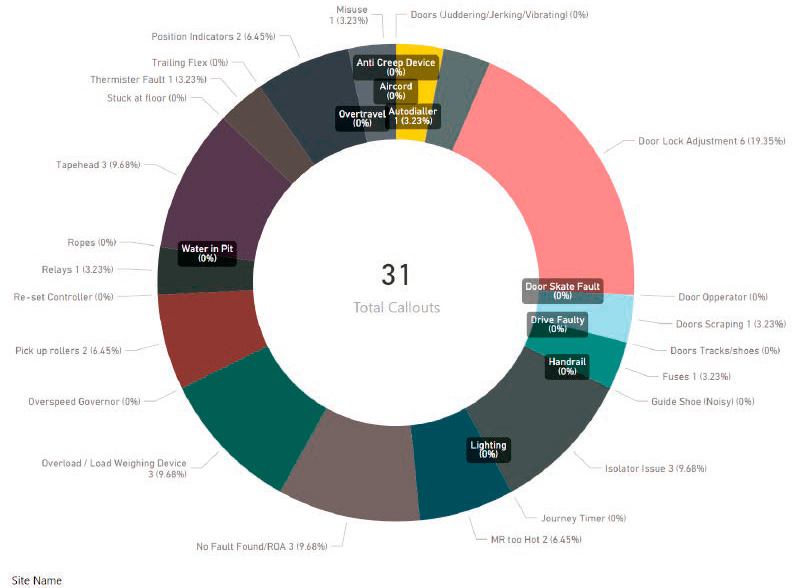
A summary of the second-winning dissertation from the inaugural Alex MacDonald Award
by Paul Clements
The intention of this document is to provide a summary of the works carried out from November 2018 to September 2019 reflected in the 138 pages of the dissertation, which was held at the University of Northampton.
When applying an IoT solution on a lift, sensors can be set up on key components, which then transfer data to the management device. The management device will then be connected to the internet via a 4G router or ethernet port that sends the data to the cloud-based platform. The data can then be analysed and managed via the internet through a computer or mobile device where script writing can be used to program notifications when the condition of the lift is out of set parameters.
Motivation
Since the introduction of the first known ‘Smart Device’ in 1982, where students of Carnegie Mellon University, Pittsburgh, Pennsylvania, installed micro switches on a Coca-Cola machine to check the stock levels and temperature of the refrigerated drinks (Smith G, 2015); the Internet of Things (IoT) technology had huge potential in all walks of life.
Now, IoT technology has developed so far that various devices from household appliances through to heating, ventilation and air-conditioning systems (within commercial buildings) are using radio frequency identification (RFID) and transmission control protocol/internet protocol (TCP/IP) to connect wirelessly to a network and provide vast amounts of data without human intervention.
With lift equipment, there is an enormous amount of data that can be collected, analysed and used to improve the reliability of the equipment and with maintenance techniques.
Currently, data is predominantly collected by lift maintenance companies and clients through the maintenance contractor’s call centres; the data is then analysed, and judgement made on how to prevent repetitive calls. This technique is otherwise known as corrective maintenance, which can prove to be an expensive approach for both the client and contractor.
It is understood that the lift industry is moving towards using IoT technology, with various key players, such as KONE, Otis, thyssenkrupp and Schindler, all developing their own business strategies using IoT.
These developments guided me to the hypothesis: the use of IoT technology will enable earlier identification and monitoring of faults on lifts.
Aims
The aims of this study were as follows:
- To investigate the history of IoT technology and its developments
- To investigate how IoT technology can be used within the lift industry
- To investigate what IoT is currently being used for within the lift industry
The overall aim was to investigate the above topics to establish the effectiveness of IoT technology and its relation to fault identification/monitoring.
Objectives
The following objectives were set out for this research paper:
- To analyse callout data for a portfolio of various ages/types of lift equipment
- To identify common faults within the sample of data obtained
- To identify uses of IoT technology and establish a connection/link between lift faults and IoT monitoring approaches
- To implement small-scale experiments whereby IoT technology is used to monitor common faults found within the callout data obtained
- To explore how IoT technology is currently used within the lift industry.
- To analyse data obtained from the contractors that are piloting this technology
Key questions that have been answered are:
- What is the age of the equipment the data has been collected from?
- What types of callouts are being recorded and can these be categorised?
- Can current IoT technology be used to monitor the faults that have been found within the data?
- What are the benefits to key stakeholders (e.g. equipment owners, maintenance companies)?
- Are there any further improvements for maintenance regimes/types that can adopt IoT technologies?
Methodology
This study required a methodical approach in order to be able to identify common callout types and whether IoT systems could be suitably used for condition monitoring and earlier fault identification. The methodology used to enable the successful completion of this dissertation is as follows:
Data collection
Data used was collected monthly by the maintenance contractors through the use of their call centres and different data-capture systems. This data was then provided to the client each month to allow analysis of how they were performing. Overall, data was collected from four different suppliers across 48 different sites and a total of 114 lifts.
The data contains information of the date/time the breakdown callouts (calls) were received; the detail provided on the call; the fault found whilst on site; any further action required; the date and time the call was completed and the call reference number.
The data collected was from a 13-month period, between 1st December 2017 and 31st December 2018, which provided a large enough data set for analysis.
Fault Identification and Analysis
The data collected from the client was analysed and details extrapolated to identify the various call types and analyse any trends that have been noted. The information collected has provided a vast amount of data, which, in itself, can be classed as “big data.”
A software package called Microsoft Power BI (Rouse, 2019) was used for the analysis of this callout data. This Microsoft-based system uses data that was compiled into an Excel spreadsheet to visually represent the different callout types and trends that have been gleaned from the information received.
The data collected from the client and lift suppliers was analysed and reviewed with the intention of identifying various call types that can occur within a lift system. These call types were then used to identify where IoT technology can assist with identification of the faults prior to them occurring.
Questionnaire
Further data was collected through a survey. This questionnaire was sent to lift maintenance contractors and lift consultants to answer.
The survey was created using SurveyMonkey™ (FinancesOnline, 2019), a portal that allows bespoke surveys to be created and distributed via a link that can be used multiple times. The system collects the answers to the questions and allows for analysis of these answers. This also shows details of response rates, average time spent answering the questionnaire and picks out any trends in the answers.
The questionnaire was sent to seven lift maintenance companies and one consultancy company. Of these companies, six allowed the distribution of this to their wider teams.
The purpose of this questionnaire was to obtain details from competent persons within the lift industry of:
- Common faults experienced
- Typical resolutions to the common faults identified
- Knowledge of IoT technologies
- Where IoT technologies could assist with the detection of the common faults noted
Experiment
A small-scale experiment was undertaken on some lifts. This experiment used the outcome of the data collection and analysis to pinpoint common faults and employ IoT technology to monitor parameters that can assist with the earlier identification of these faults.
Low-cost IoT sensors were purchased for the purpose of measuring various parameters and automatically alerting the author when faults potentially had been identified or the condition of the lift/environment could cause a failure. Following the positive identification of a fault, callouts were raised with the maintenance supplier and the issue resolved.
Along with IoT sensors, an IP camera was also purchased, which allows remote access through desktop and mobile applications.
The below sensors were used throughout the experiments. The justifications for this choice were:
- Through the knowledge gained by reviewing developments in IoT technologies, it was identified that temperature, humidity, moisture, movement and light can be monitored through the use of low-cost devices.
- It was identified that these devices were relatively easy to program and create coding to provide notifications.
- The total budget for this study was restricted, and the sensors bought were of a relatively low cost.
The IoT technology used within this experiment was bought from a website called wirelesstags.net. These “tags” can connect to the internet and collect different data like tag movement, infrared movement, contact, temperature, humidity and moisture.
The data is stored on a cloud-based system that can be accessed from anywhere in the world.
Wireless Tag Products
The wireless tag system works by using an Ethernet-based “tag manager.” This device connects to the internet via an ethernet cable and is powered by a microUSB. The router connecting to this device must allow “10Base-T” and a “DHCP server.” The firewall must allow “outgoing HTTP (port 80) and port 6667 connection.”
A single tag manager can allow up to 40 separate sensors to connect and send data through to the cloud-based system.
The tags available on wirelesstag.net are shown in figures 5-8:
- Figure 5 shows a Wireless Sensor Tag Pro ALS, which can monitor changes in ambient light, temperature, humidity and movement.
- Figure 6 shows a PIR KumoSensor, which can detect motion and timeout of no movement within a certain amount of time. This sensor can also monitor temperature and humidity.
- Figure 7 shows a Reed KumoSensor, a contact-based sensor that monitors when doors/windows are open/closed along with temperature and humidity.
- Figure 8 shows a wireless water/moisture sensor, which monitors water levels and the presence of water in a dry or moist area. This sensor also monitors temperature and humidity.
These sensors operate at a maximum range of 210 m in the line of sight to the tag manager; provide a battery life ranging from 2 to 7 years; operate between ‐40°C and + 85°C; provide accuracy readings of up to +/‐ 0.4°C and have a light sensor with 0.1 ~ 200,000 lux range. Full details of the technical specifications for these sensors can be found in appendix C.
The data captured by these sensors has been made available through smartphone and web-based platforms accessed with a username and password for security measures.
The results of the data analysis and questionnaire survey provided details of various faults that typically occur on lift systems. The knowledge of what can be monitored using these sensors allowed informed decisions to be made on where sensors could be used to assist with condition monitoring (i.e. temperature, humidity, moisture, etc.), and thus provide earlier identification of faults.
Conclusions
Although IoT technologies have been around more than 30 years, developments in this technology over the past 10 years have seen smaller chipsets and low costs; off-the-shelf sensors are now available for use by everyday consumers. The lift industry has developed significantly over the past century with various advances in control-system technology and maintenance regimes, with recent developments focusing on implementing IoT technologies into the standard packages that the major lift manufacturers supply, along with retrofitting these systems to lifts under maintenance portfolios.
Major lift manufacturers have large budgets available to develop their own systems to collect large amounts of data that can be analysed and used to develop smarter, more insightful maintenance regimes. This would allow them to predict and even preempt potential faults with the goal to identify individual component life expectancies. Although this development in technology will assist the client in the long run, these manufacturers are focusing more on the internal benefits to their organisations rather than the benefit to the client, which may be one of the reasons it has taken longer for the lift industry to adopt this technology.
Independent lift maintenance companies do not have such large budgets to develop these systems. However, the latest developments with IoT technology means that with the use of a few sensors, a system can be implemented at low cost to monitor the condition of various components and analysis of the data collected used to assist with early identification of faults.
Analysing callout data collected over a 13-month period shows there are an array of faults that can occur on lifts. However, these can be grouped together into different sections of the lift system, making it easier to understand where problems occur and assist with pinpointing what could be monitored by sensors.
A questionnaire issued to various stakeholders within the lift industry has confirmed the findings within the callout data analysis and assist with understanding common faults that occur and how IoT technologies can be used to assist with condition monitoring and earlier fault detection.
Experiments using off-the-shelf IoT sensors, a camera, a small understanding of script writing and 4G routers have proved that low-cost solutions can be implemented by key stakeholders such as independent lift companies, consultants and even clients to provide real-time data regarding lift condition. Assumptions can be made using the data gathered to assist with detecting and resolving faults earlier.
With some site preparation, such as installing additional ethernet ports and power supplies within the lift motor room and shaft, temperature, humidity, moisture and movement sensors can be installed around the system to provide this information to the key stakeholders who could be located anywhere in the world.
Where ethernet ports are not available, 4G routers can be supplied. However, as the experiments and major suppliers have been identified, there are potential issues that can occur with signal strength that should be considered during the installation of these systems.
Other items to consider when installing these types of systems are:
- Placement of the sensors: what data is being obtained?
- Lift design: these can be different, and sensors may need to be installed in different places to obtain the same type of data on different equipment (e.g. movement of a sheave, a contactor pulling in or vibrations within the motor).
- System integration: whether the system will work together with components such as 4G routers allowing access to the correct ports allowing systems to get online.
- Signage: ensuring all stakeholders are aware of the technology used so they do not accidently disturb the sensors.
- Battery life of sensors: understand the limits of the devices and how to optimise the battery life by changing settings such as notifications.
- Data usage: when using 4G routers for specific applications, consider the data usage required.
Fault analysis of a sample set of lifts combined with confirmation of said faults from industry experts (using a questionnaire) have been utilised to identify that 70% of callouts recorded on the sample set could be identified by low-cost devices that monitor temperature, humidity, moisture and movement.
Overall, this study has successfully identified that IoT systems can be used to monitor the condition of lifts and assist with early identification of faults. The IoT systems used result in reactive responses to faults that are automatically reported by the devices. This provides a benefit to both the client and maintenance contractor.
The major lift contractors mentioned throughout this study are applying these systems to their maintenance portfolios and, additionally, are applying analytics to the data collected. They are trying to achieve a system that can predict when a breakdown is going to occur so they can attend to and resolve the problem before it occurs. Machine-learning techniques are being implemented by data scientists and lift engineers, which requires large investments.
Before machine-learning algorithms can be used, data must be collected. The data collected throughout this study could be analysed by data scientists in the future when analytic packages become available to the independent lift industry.
There are various benefits to using the IoT system within this study in comparison to the systems implemented by major lift suppliers:
- Costs are significantly lower compared to the systems being implemented by the majors.
- Major suppliers are focusing on installing their systems on their own, new equipment first. The system in this study is adaptable for any manufacturer’s equipment.
- The IoT system noted in this study can be used as a permanent solution for condition monitoring and fault detection and as a temporary solution to identify the root causes of intermittent faults such as overheating.
- The system within this report does not require a client to be locked into a specific contract whereby only the installer of the equipment can use the system.
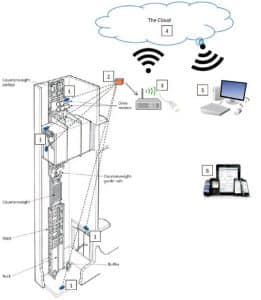
- Figure 1: Typical setup for an IoT system on lifts
- IoT sensors (1)
- Sensor management system (2)
- Router or ethernet system (3)
- The Cloud (4)
- Computer interface (5)
- Mobile interface (6)
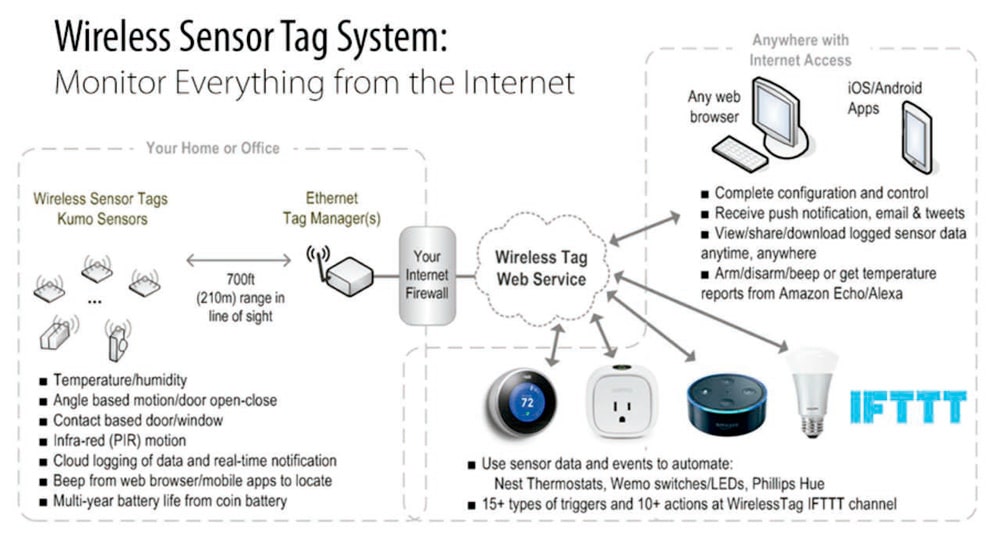
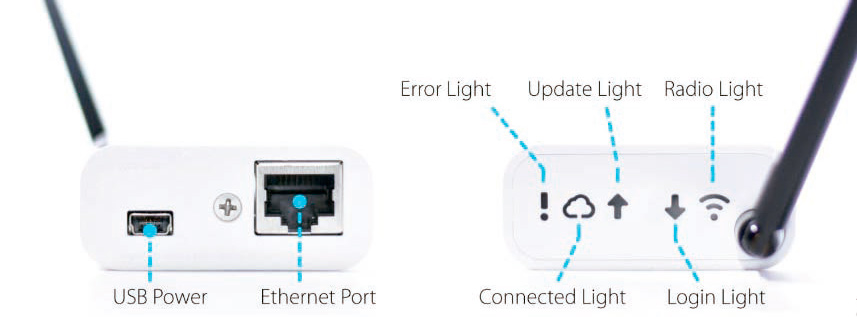
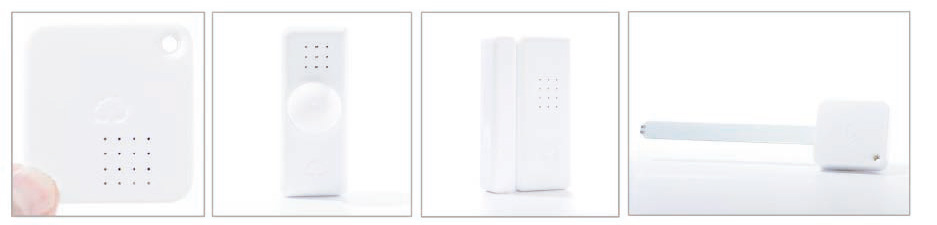
Get more of Elevator World. Sign up for our free e-newsletter.