What’s New in Modernization
May 1, 2019
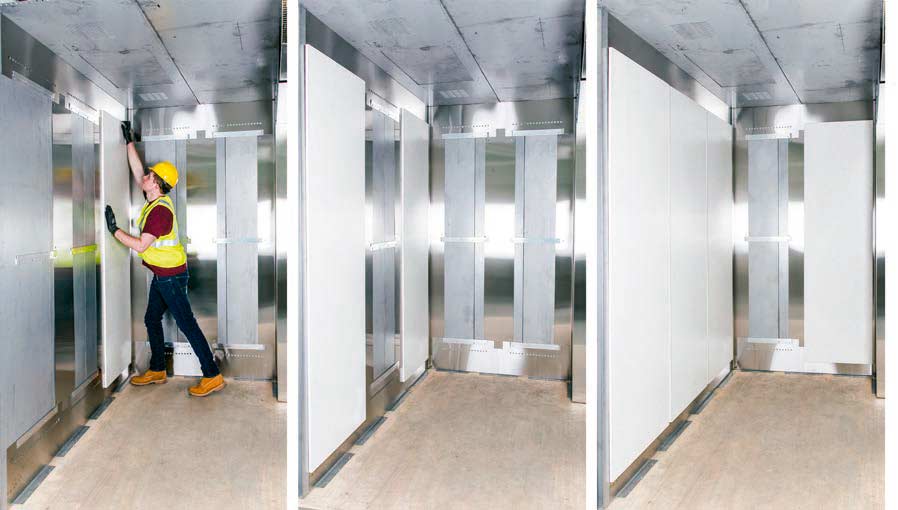
Columbia advances the upgrade of cabs.
In today’s real-estate universe, rising with the ever-escalating heights of today’s supertalls, is the incidence of elevator modernization, and there are numerous reasons why. Prominent among them is that these new structures and additional available space are creating competition for tenants and the market-driven need for landlords of existing properties to upgrade them to retain their current occupants and attract new ones. This is particularly true of the elevators and lobby, the components of the building with which its occupants and their visitors engage most frequently. Other drivers may be the desire to achieve energy and cost savings by upgrading to updated technologies or meeting accessibility requirements. Yet another may be changes indirectly triggered by code considerations: for example, as is currently the case in New York City (NYC), where there is a requirement to install elevator-door-lock monitoring systems on all automatic elevators by the end of 2019. While this code change addresses safety and has nothing to do with aesthetics, some building owners and managers, while being made to focus on changes to their elevator cabs, are also being moved into upgrading them to some degree. Even further, a code- compliance trigger of this kind can lead to a full-blown modification, with the building owner reasoning something like, “Hey, while we’re doing the door monitoring, we may as well use the opportunity to change the door operator, but as long as we’re doing that, maybe it’s time to hang new doors, and if we do that, then the walls and the front won’t look right, so let’s do the whole cab.”
The primary underlying cause, however, may simply be a function of the continuously growing nature of real- estate development, as Louis “L.J.” Blaiotta, Jr., CEO of Columbia Elevator Products Co. Inc., explains:
“Over time, new-installation equipment goes in every year, which, by deflnition, causes the overall installed base of elevator equipment to continuously increase. This base eventually grows older and in need of maintenance and upgrade. Elevators are not taken out of service unless the building comes down, and, until it does, there will be an elevating device in that building. Consequently, the pool of elevators needing to be modernized is expanding every year, fed on the front end by the steadily increasing number of annual new-construction installations.”
Modernization patterns tend to run in phases depending on the economic conditions of the time. During boom times, widespread new construction drives modernization, because landlords are improving their existing properties to retain tenants. During down economic periods, especially prolonged ones, a certain level of maintenance and modernization becomes necessary as installed equipment ages to the point of becoming “old” and in existential need of help. Glossing over the situation with incremental touch- up fixes can grow to become overbearing in terms of frequency, aggravation, downtime and cost, leading to a point when the best and most-e–cient course is to do what the elevator industry colloquially terms a “mod.”
Continues Blaiotta:
“When the economy is up, mod work and new construction both go up, with ‘new’ rising relatively faster. In a recession, both categories slow down, but the ratio between the two changes, as new construction decreases relatively faster, and we do a lot more mod work. As a manufacturer, we need to be sensitive to and properly positioned for these phases. But, big picture, no matter what the environment, demand for mod work is always high, and we at Columbia are perpetually looking for new ways to make it better for the installing mechanics: to deliver needed components ever more quickly and cost-e.ffectively, and to make the work as quick, safe and foolproof as possible to install in the fleld.”
In this regard, Columbia has announced major enhancements to its legacy XChangaCAB™ system, a revolutionary product that enables quick, cost-e–cient, in-place cab upgrades requiring only limited downtime and available in a virtually unlimited array of design options. Shipment of the original design to the jobsite included a metal template and rack system for installers to use in the field to help them know where to place clips on the walls, working off each wall’s centerline to position the hanging panels. Now, Columbia has innovated a much clearer and easier guidance methodology to facilitate this process, as Blaiotta spells out:
“What our next-generation system does, instead, is notch the reveals — the decorative pieces of stainless steel between the hanging panels — so that they, themselves, automatically become the template. Now, all that the mechanic needs to do when installing a mod is to glue the reveals onto the wall and into the corners, then install a frieze at the top. All these components are designed to align with one another, with the notches then indicating exactly where to place the o.ffset hanging clips on the wall. While initial measurements are, of course, still required to specify the size of the car, this does away with further onsite measuring and repeated repositioning of the XChangaCAB’s formerly used metal templates and racks, now unnecessary since this system facilitates precise positioning of the clips and panels.”
From its years of mod experience, Columbia learned that there were critical differences between building new cabs from scratch and modifying existing ones in the field. When creating an all-new cab in the factory, the company can build panels exactly to size and place the mounting clips exactly where they need to go. When performing a mod in the field, however, it was discovered that sometimes the cabs — especially in older installations — were not square, which required some level of flexibility to properly fit new panels into the existing environment. This flexibility was created by slightly varying the reveals separating the panels, with differences of appearance between the walls so minor as to be imperceptible to the eye. The reveals are oversized, and the panels are bigger than the reveals, which enables the panels and reveals to be overlapped. By using offset clips rather than a single hook or hanging-panel “button,” the materials can be placed on the clips and slid left and right to whatever degree required to most attractively set up each respective wall. This ability to slightly adjust each panel’s position effectively masks discrepancies when old equipment is not exactly square or the exact dimensions specified when the cab was originally built — perhaps decades earlier — were not precise. This approach to flexibility is su–ciently forgiving to “cover up” many irregularities routinely found in existing, older installations to produce an apparently flawless new look.
To make installation as foolproof and intuitive as possible, there are numerous other aspects to Columbia’s new system, Blaiotta explains:
“We make all the pieces unhanded and reversible, so there is no way to install them incorrectly. All o.ffset clips are the same size to avoid confusion and time flguring out what to use where. For precise guidance, the top frieze and base are notched to indicate exactly where to place the center reveals, clearly identifled as such by being notched on both sides. Corner pieces are clearly identifled by being straight on one edge and notched on the other, with the notch later obscured from view by the hanging panel or even coved to hide unsquared corners.”
According to Blaiotta, Columbia applied considerable thought to adapting this approach to incorporate ventilation as required by code. The bottom base is oversized, as is the decorative metal frieze at the top. Inside the frieze, around the edges, is a hole pattern indicating to the installer where to drill, with the number of holes calculated and factory-specified to the size of the cab. In the final installation, these holes in the frieze are not visible to riders, because the panels are offset from the walls, and the holes are positioned in the space behind the panels. This slight but invisible space is created by relieving the panels, allowing air to flow behind them from the bottom to the top. Code requires there be no straight-through passes, to prevent riders from inserting objects through any holes in the cab and contacting anything in the shaft. The offset panels obscure the ventilation holes, thereby rendering the openings inaccessible and the installation code- compliant.
Blaiotta notes that another key matter to consider in enhancing Columbia’s XChangaCAB system — and the cab’s appearance following a modification — involves the floor. Over the years, the flooring treatments in an older car may have been redone several times, with the floor becoming unlevel. Under these circumstances, making the entire installation relative to the floor which was how it was routinely done by using templates that started at the bottom of the cab — threw the entire thing at least somewhat out of kilter. Columbia observed that, even on jobs where the floor is a “mess,” the cab’s cartop has never been touched. As the cartop is level, the best outcome would be achieved by installing all else relative to the top of the car. The installation is done so that the bottom edges of the base wind up about 1/4 in. off the floor. This creates a dark groove in a shadow at the bottom that makes any irregularities unnoticeable. While straight 90° corner reveals can be used when the car is reasonably square, most such installations benefit from the use of radius or “coved” corners, the curved nature of which serves to obscure that the panels are slightly off. Coved corners do not have the center seam that, in straight-angled reveals, acts as a frame of reference for true vertical.
his approach to flexibility is sufficiently forgiving to “cover up” many irregularities routinely found in existing, older installations to produce an apparently flawless new look.
In many mods, the aging cab-side doors are damaged and unattractive. Columbia’s QuikDoor™ program uses single-skin doors that are much lighter than the dual-skin doors they typically replace. If the operator is being upgraded at the same time, the door can be made to close at a significantly faster rate without violating kinetic-energy requirements. QuikDoor features a Unistrut® at its top. This is a universal channel that allows attachment to any manufacturer’s door operator equipment, again eliminating the need for intricate measuring. The door comes with a plate on the back and the top Unistrut for the pendant bolts, allowing attachment to all brands of operators. Shaft-side, fire-rated doors are available, as well, either fitted with a Unistrut or, with extended delivery time, custom.
Recent additions to Columbia’s mod services have required overcoming challenges to traditional solutions for the installation of suspended ceilings and the recladding of car fronts, both among the more di–cult things to accomplish at a jobsite, Blaiotta said:
“When building a car in the factory, it’s fairly simple to drill holes in the proper places and mount a suspended ceiling. But, in the fleld, where the task is to mount such a ceiling into a cab made decades ago, potentially serious problems can arise. As you drill holes up through the canopy to install the hanger rods, you can interfere with or damage things atop the car, including electrical wiring and various mechanical objects. Columbia’s solution is to go to the top of the car and drill down, staying away from previously installed car-top equipment. While the holes need to be a certain number of inches from the edge of the car, there is no other requirement as to where to position them. We tell you how many holes to drill, in any space you can flnd that doesn’t interfere with existing infrastructure. Then, inside the car, we have you mark the center point, where the wall meets the ceiling. We provide a channel bracket, including a long leg with a notch in it, which is placed at the top of the car with the notch lined up to the previously marked center line. This channel has a continuous pattern of holes in it, one of which is bound to line up with holes you previously drilled, and you drop a bolt down through that hole from the top. The channel bracket contains a hinge point, to which the ceiling unit is attached and swung up into place. This is so much easier and safer than requiring four mechanics to lift a heavy ceiling into place and much easier to wire up the ceiling, install lighting, etc., when everything is open and exposed before swinging it up. The substrate we use is aluminum honeycomb, which is extremely light and avoids adding undesired weight to the car, and it is flre rated, as opposed to the older wooden ceilings these installations often replace.”
The most challenging part of any cab modernization is likely the upgrading of the car front. It is so di–cult to “reskin” the multitude of surfaces in the field that many designers simply choose to remove the existing car front and replace it with all new construction. Because this is a much longer process than cladding the existing car front in the field, Columbia developed a simpler and more foolproof way to accomplish this. Like its wall solution, Columbia’s forgiving cladding method does not require all the exact sizes, so the cladding of car fronts can be accomplished by knowing only a couple of simple-to-measure dimensions. An additional benefit is that the existing car front remains in place, avoiding the need to take the car out of service for an extended period. Instead of attempting to cover existing car fronts with metal cladding or “skins” fabricated exactly to size — which would require exacting field measurements — Columbia devised a much more forgiving “oversized” cladding solution. Using shimming to eliminate any/all transom projections, they convert all car fronts into “partial-transom” designs that incorporate floor-to-ceiling return and/or strike panels, plus “inset” transom heads over the door opening. This configuration eliminates the need for the di–cult field measurements. Also, to help compensate for “out-of- square” field conditions, the return and strike claddings further incorporate radiused/coved interfaces with the side walls, similar to the coved corner reveals used to conceal out-of-square wall conditions.
There are several issues for building owners and managers to ponder when considering an elevator modernization. Much depends on the size and scope of the building and its elevator system’s age, appearance, budget and impact on the building while the replacement work is underway. Finally, there must be a meaningful reason for doing it. The mod can range anywhere from an aesthetic brightening to a structural or functional upgrade. It is widely held that a properly maintained elevator can enjoy a useful lifetime of at least 15 years, but, during its lifetime, there may arise compelling reasons to upgrade. The elevator may visually deteriorate, its style may become outmoded, certain parts may fail, and/or it may become unreliable and subject to recurring downtime that damages tenant relationships.
In our rapidly evolving world, beyond merely aesthetic considerations, elevator modernization will become an ever-more- relevant factor as demographic and cultural changes take hold. Younger generations are concerned, as has always been the case, with style and safety, but also increasingly with e–ciency, infrastructure, and health and environmental issues. Interest in machine-room-less and other green elevator designs is on the rise as global urbanization and associated commercial construction continue to grow, and the modernization market will generate more and more work.
Concludes Blaiotta:
“It is Columbia’s mission to keep making life as safe, easy and efficient as possible for the people who will be doing this work by continuing our legacy of innovation begun in 1965. The way replacement equipment is brought in, installed and placed into service is something we care passionately about.”
Get more of Elevator World. Sign up for our free e-newsletter.