“World’s First Composite Lift” Unveiled
Mar 1, 2017
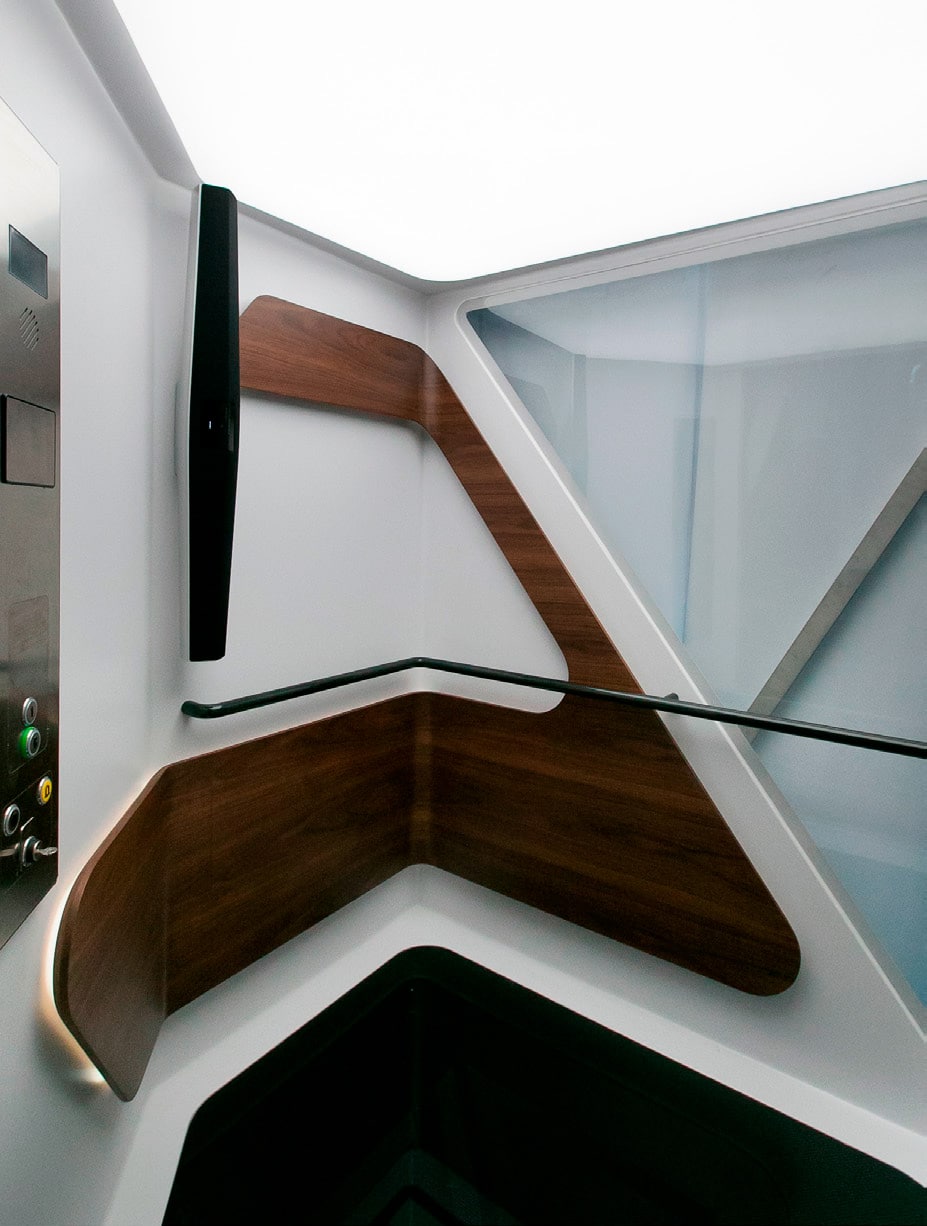
Singapore-based consortium says innovation will be a game changer.
The world’s first composite[1] lift, 8, was unveiled on January 11 by Singapore Lift Co. (SLC), a joint venture between Far East Organization, Woh Hup Pvt. Ltd. and Pronus (HK) Ltd. Made of lightweight composite materials used in place of steel in industries such as aerospace, Formula 1® racing, electronics, yacht building and deep-sea exploration, 8 is “a game changer in its field, having the potential to revolutionize the overall building and construction industry,” SLC states.
8 has three applications — disabled, home or passenger lifts – using four different drive options: small ropes, V-belt, rigid chain or hydraulic. With a minimum 1,400 mm turning diameter, it is the only lift, according to SLC, designed to enable a sufficient turning radius for wheelchairs. For home lifts, it allows for customized interior design and other technical fittings. Energy efficient with remote monitoring, 8 is initially available for installation in low-rise buildings, and will eventually be extended to serve buildings with up to 20 floors.
SLC Managing Director Alister Bennett tells ELEVATOR WORLD cabins will be manufactured at its facility in north Singapore, with other components sourced from various countries such as Germany and Italy. The facility’s initial annual capacity is 1,000 units, and SLC hopes to design and build all components in Singapore within the next five years.
Following the introduction of 8, SLC intends to expand its capabilities to the design and installation of lifts of any stipulated size into lift shafts with just a minimum of 25 mm clearance on all sides.
Largely assembled offsite, 8’s cabin weighs 150 kg, compared with a traditional lift of the same capacity that weighs 1500 kg. It does away with the need for complicated shaft designs and the number of concrete walls and/or steel supports to bolt-on brackets for guide rails and landing doors.
Aside from cost and time-efficiency benefits, easy installation of the lift means that specialized skilled labor will no longer be required.”— Alister Bennett, SLC managing director
The lift offers a “breakthrough solution” to the problem of limited cabin space, vis-à-vis the lift shaft size, due to the position of counterweights and guide rails in traditional lift shafts. Using only one structural face for support, the shaft design has been considerably simplified, with no or shallow pits and low overheads. This is in contrast to traditional lifts, which require construction of deep pits and high overheads. With 8, the cabin space has been considerably enlarged to enable it to carry a larger load, due to maximizing the shaft size, overhead and pit.
The potential overall savings to be realized through enhanced productivity in construction and faster installation times allow for better materials to be used and a safety system to be incorporated into the lifts without pushing up overall costs, according to SLC. 8 is compliant with to EN 81-41 and EN 81-20:50 standards by Liftinstituut.
Bennett observes:
“8 has far-reaching implications beyond just the paradigm shift away from using steel in the manufacture of lifts and its accompanying requirements in shaft design. We see great potential for our product in the building and construction industry, as well as the retrofitting industry.
“Composite material is not new, but its use in our lifts is groundbreaking. Aside from the cost and time-efficiency benefits, easy installation of the lift means that specialized skilled labor will no longer be required. There are currently an estimated 61,000 passenger lifts in Singapore[2] with only an estimated 2,000 lift technicians.[3] With this innovation, any person can be trained and certified to be fully qualified to install the lift, and this would reduce, to a certain extent, the labor issue for lift installation and the cost of maintenance.”
While traditional lifts require, on average, five to seven days for installation of a single floor, with 8, that can be reduced to a minimum of one floor per day, Bennett states. There is also no necessity for welding or heavy-lifting equipment, which can make it a safer, less labor-intensive process. “In the building and construction industry, any small amount of savings in labor and time can go a long way towards lowering overall building costs,” he says.
While Bennett says Singapore currently does not possess the knowhow for the design, engineering or manufacture of composite lifts, SLC intends to build up this industry by leveraging the existing skills and capabilities of its highly educated workforce.
SLC selected Singapore as its base due to its “skilled, efficient and productive” workforce, Bennett states, adding:
“We hope that we can build up the composite lift industry here so that, in time, Singaporean companies will be able to provide innovative solutions for this nascent industry to the rest of the region and, eventually, the world. We also aim to work with local tertiary institutions to develop skills in the design and engineering aspects of lift components for the composite industry in general, so that Singapore will eventually become a hub for the industry.”
References
[1] Composites UK (compositesuk.co.uk/composite-materials).
[2] Heng, Janice. “BCA Encourages Lift Owners to Modernize Existing Lifts for Better Reliability,” Straits Times, September 16, 2016.
[3] Heng, Janice. “Lift Sector Facing Shortage of Engineers, Technicians,” Straits Times, August 1, 2016.
Get more of Elevator World. Sign up for our free e-newsletter.