Art in Motion
Nov 1, 2020
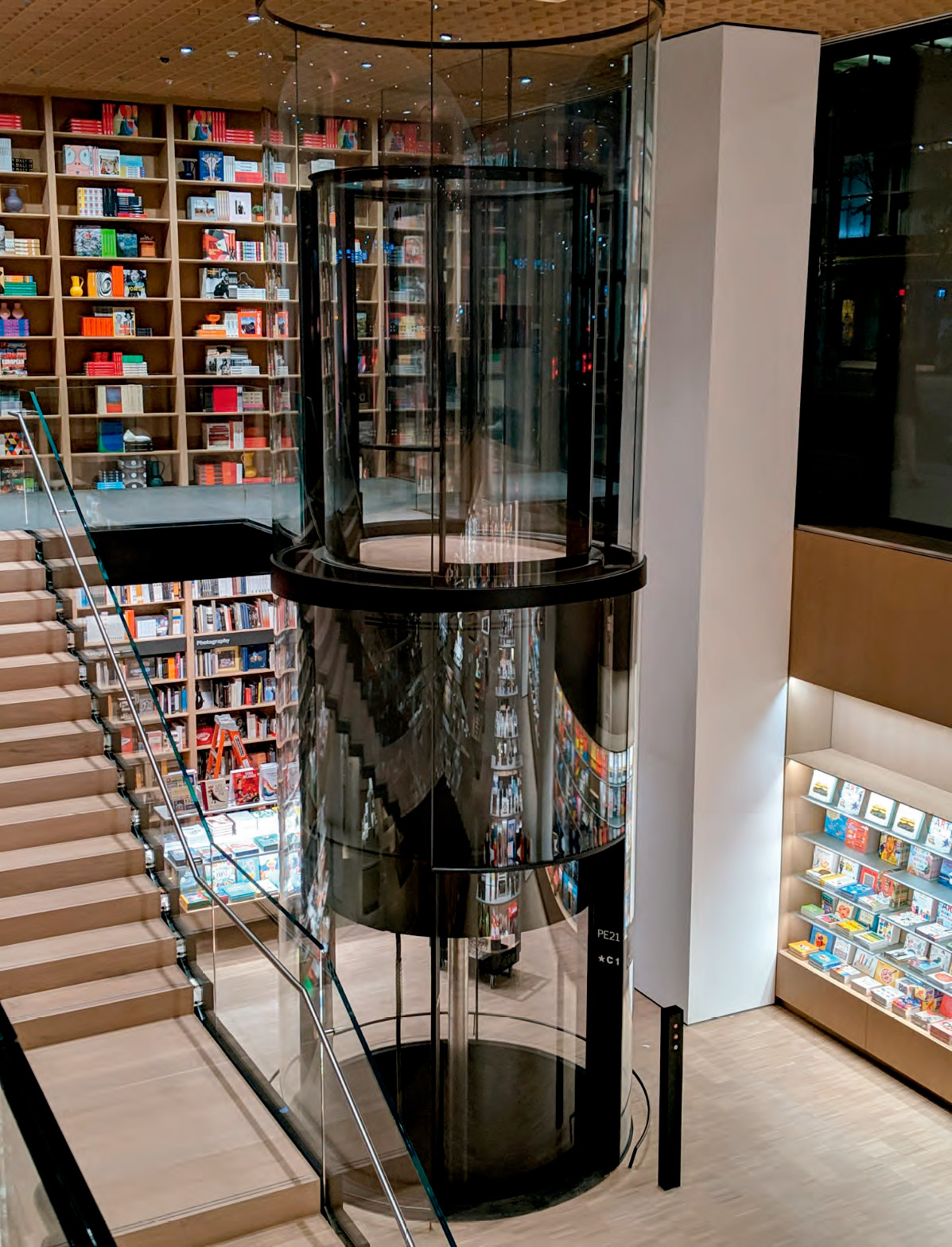
by Farid Waleh
Every once in a while, an architect requires a design that challenges the elevator industry. One such job was the Museum of Modern Art (MoMA) expansion in NYC. Originating in fall 2016, with the elevators delivered in late 2019, the job involved a trio of custom units serving a revamped retail area. While two of the elevators are remarkable in their own right, the star of the show is a two-stop, round, glass elevator with front and rear openings.
Rather than just another round elevator, architect Diller Scofidio + Renfro (DSR), working with principal architect Gensler, envisioned it with a freestanding shaft, its only support from a walkway on the second landing. All three units were designed and manufactured by San Diego-based Custom Cabs Inc., with Liberty Elevator Corp. of Paterson, New Jersey, handling installation and VDA® serving as consultant. An array of suppliers was also involved.
Two square cab elevators grant access to MoMA’s six floors, from lobby to terrace café. If they were works of art, they could be compared to the work of minimalist painter Philip Rothko. Liberty observes:
“These lifts are [sleek] with a monochromatic oxidized black metal finish with recessed LED lighting to give a true minimalist experience. Unlike the impressionist paintings of Monet or thick paint strokes of Van Gogh on the fifth floor, the elevator cabs are completely flat noir with a smoked glass wall, allowing the slightest hint of the duplex separation with the adjacent elevator shaft. Each elevator landing has custom-painted doors and matching fixtures to pair with the museum’s strict color palette.”
The project is a source of pride for all involved. Liberty, for example, calls the elevator “a true piece of art in motion” and the first thing one notices upon entering MoMA’s renovated lobby. Liberty states:
“The custom elevator has a glass cab that surrounds you as you transcend from the mezzanine to the lower-level bookstore, providing a floating feeling as the transparent cylinder smoothly transports you between floors. All mechanical aspects of the elevator, including door operators, are hidden underneath the cab floor, giving a minimalistic appearance, while maintaining its. . .technology in a shroud below. The round glass doors and glass ceiling allow for uninterrupted views of the lobby and gift shop.”
Freestanding Design
The freestanding shaft has no way of supporting the rails and car as it travels. The shaft is mostly glass with a small frame. Rail support is provided by vertical tubes behind the rails. The tubes are only supported at the pit and at the middle ring. Otherwise, they are freestanding. The architects wanted all square corners on the outside of the tubes, so they had to be specially ordered and made out of stainless steel. The walls are extra thick to be strong enough to withstand the rail loads. The tubes were ordered with zero tolerance, as there was no way of getting the rails aligned in case of twists or the misalignment present in regular tubes.
The rails are attached to the tubes, while the tubes themselves are attached discreetly to the supports behind and below the first landing and on the pit floor. Those are the only supports for the tubes.
The pit is covered by thick, blackened, rounded stainless-steel panels that cover it from the floor to the first landing. The rest is glass with minimally blackened stainless steel. There is a structural ring at the second level that ties the shaft to the bridge at the rear opening. The ring was especially difficult to model and make, as it tapers from the bridge to the other end. It had to be made in two, rounded pieces and welded together with the tapered edge in line. There is a small ring at the top of the shaft to hold the glass, and the top is open.
The jambs and headers on the entrances are made of 1-in.-thick, flat, blackened stainless-steel bars. The hall stations and hall lanterns are on pedestals.
While the stainless steel was rounded and blackened by Custom Cabs in its shop, Cristacurva, which has locations in Houston and Mexico, provided the glass, and Wayne, New Jersey-based Elevator Products Corp. provided components for fixtures, such as buttons and fixtures. The faceplates and assemblies were made by Custom Cabs.
Complexities Multiply
This is a small cab, with a diameter of 73 in. and a capacity of only 2500 lb. To make things more complicated, it has front and rear openings with Custom Cabs’ exclusive under-platform door operators on both doors. Due to the size of the car, we had to stagger the door operators under the platform so that we could fit both in the small space. The openings were at an angle from one another, which affected the location and pivot points of the door operators.
The entire cab structure is below the cab; the only parts one sees at the top floor is the glass-and-steel cylinder popping up. The steel part is minimal, consisting of a top ring, flat bar jambs and header, and a pedestal-type car operating panel. The rest is clear glass.
The entire shaft and cab (with the entrances) was modeled in 3D software. This is how these projects are designed and manufactured to look exactly as the architects envision them.
We manufactured the pit shroud, the ring and the rest of the shaft enclosure in our factory and assembled it there for DSR to observe how it looked and functioned before packing and shipping it to the jobsite.
Final Installation Is Critical
The final installation is critical: you can have the best design and workmanship and take all the care to properly package and ship the product, but, if the installation crew is not careful or properly trained, they will damage it, and all previous work will be wasted. Fortunately, Liberty’s professionals did a fantastic job.
The project is also a source of pride for VDA. Senior Vice President and project manager Michael Muñoz states:
“The design architect really pushed us — the elevator consultant and structural engineer — to come up with a solution that would meet their vision. While that was difficult to get done, the end result is that being pushed to think outside the box really did result in a beautiful end product.”
Get more of Elevator World. Sign up for our free e-newsletter.