by Fernando Guillemi and Alea Guillemi
This paper was presented at the 2022 International Elevator & Escalator Symposium in Barcelona, Spain.
Abstract
The concern about environmental degradation is growing by the day. The UN says this is a key year to try to curb the “disastrous” effects of climate change and urges countries to act now to achieve zero emissions by 2050.
Environmental degradation is defined as the process of deterioration suffered by the environment as a result of the depletion of its natural resources due to the overexploitation to which they are subjected, thus causing the destruction of ecosystems and their biodiversity.
Several of the activities carried out by human beings are linked to this degradation: in our case, industrial activity. Although we create a large number of jobs, that is one of the factors that creates the greatest negative impact on the environment. We generate large amounts of waste of all kinds, polluting the soil, the water and the atmosphere. We need to burn fossil fuels to generate energy, and some wastes are highly hazardous, which can cause a major environmental disaster in the event of an accident. From our sector, we must assume the commitment to care for future generations, and we have a lot to contribute if we take the right approach to the problem.
Elevators consume between 3% and 4% of the energy, out of a total of 14 million elevators installed worldwide. But perhaps that is not the right perspective to address the problem in which our sector negatively influences the environment. In this presentation, we will take a different approach. We are convinced that this is the right way to do our bit and slow down environmental degradation.
Introduction
Is the biggest carbon footprint generated by the elevator sector due to the use of the elevator or to maintenance, lubrication and inspection service when moving with a vehicle that consumes hydrocarbons? Should we be concerned about only the carbon footprint, or could it also be that we should eliminate as much as possible the pollution produced by some types of elevators? Could we do something to improve human resource efficiency and the sustainable manufacturing of equipment?
This paper will answer each of these questions and propose solutions to them. We will analyze how the negative influence on the environment can be reduced in each of the processes that we carry out in our companies from the moment we establish contact with a customer, to the salesperson’s assistance, the quotation, the sale, the project, the purchases, the manufacturing, the installation and the maintenance.
For us, the key points to answer these questions are the use of human resources, the choice of low-polluting equipment, the supplies and components used, the manufacturing methods and maintenance. All of them will be evaluated by making an analogy with the equivalent carbon footprint. In this way, we will be able to have an effective correspondence of the influence of each one of the processes in the ecological affectation of our environment, in order to draw true conclusions. We will analyze where and how in the whole process the environment is most affected, and then propose alternatives to mitigate the problem by making our contribution from the sector.
Development
We have seen many papers on energy efficiency in elevators, all based on how to decrease energy consumption. Much has been achieved recently. For example: the reduction of consumption when the elevator is in standby, LED lamps, inverters that stop consuming energy, position indicators that lower their intensity, automatic shutdown of lighting and fans, etc. But we forgot other aspects of the elevator equipment that were not taken into account. For example: pollution either by carbon dioxide emission or oil and grease spillage.
Later we will also address energy savings through efficient management of human resources and manufacturing systems.
Now we would like to point out the two most important factors to consider in order to collaborate with the environment.
1. Carbon Dioxide Pollution
In Argentina and perhaps in most of the western world, the typology of buildings is generally low rise and requires elevators with a relatively low load, six-to-eight-person capacity and moderate speeds. If we evaluate it according to the UNE-EN ISO 25745-2 standard:
- Elevators would be of a category of use between 2 (low) to 3 (medium) with an average of 200 starts per day. (Table 1)
- The average travel distance would be 49%. (Table 2)
- The nominal load percentage Q is 7.5%. (Table 3)
Table 1 – Classification by the number of trips per day
Usage Category | 1 | 2 | 3 | 4 | 5 | 6 |
Intensity/Frequency of use | Very Low | Low | Medium | High | Very High | Extremely High |
Number of trips per day (nA) (typical range) | 50 (< 75) | 125 (75 a < 200) | 300 (200 a < 500) | 750 (500 a < 1000) | 1500 (1000 a < 2000) | 2550 (≥ 2000) |
Table 2 – Percentage of average distance traveled
Usage Category | 1-3 | 4 | 5 | 6 |
Number of stops | Percentage of average distance traveled | |||
2 | 100% | |||
3 | 67% | |||
> 3 | 49% | 44% | 39% | 32% |
Table 3 – Average Load in the Cabin
Usage Category | 1-3 | 4 | 5 | 6 |
Rated Load (kg) | Percentage of Rated Load (Q) | |||
≤ 800 | 7.5% | 9.0% | 13% | 19% |
801 a ≤ 1275 | 4.5% | 6.05 | 8.2% | 13.5% |
1276 a ≤ 2000 | 3.0% | 3.5% | 5.0% | 9.0% |
> 2000 | 2.0% | 2.2% | 3.0% | 6.0% |
For this equipment, which is generally installed in residential buildings, the elevators are designed for loads of 450 to 600 kg and speeds of 1 m/s. The motors have power ratings of no more than 4.2 kW. They operate for 1.2 h per day with very low standby consumption and do not exceed 5 kWh per day. It is evident that having reduced standby consumption so much, during the remaining 22.8 h, we observe that the equipment does not generate a large carbon footprint.
If we take, for example, the numbers of the Argentine energy matrix, composed of thermal, hydraulic, atomic and some renewable energy, it has a ratio of kilos of CO2 produced for each kWh of 0.5. Therefore, the carbon footprint per equipment consumption is only 2.5 kg of CO2 per day.
According to statistics regarding the fuel consumption of our vehicles, to carry out the monthly tasks for elevators with claims, inspections, monthly lubrication, emergencies, audits of technical representatives, etc., they consume an average of 300 l of diesel per month each, which is equivalent to an average of 15 l per working day.
These work teams in cities such as Buenos Aires can only attend an average of four elevators per day. Therefore, we can estimate, in order to make a comparison and relate the different carbon footprints, that each elevator uses 3.75 l of diesel to be attended by our personnel and only to respond to claims. We would also have to take into account the lubricating equipment and the inspection vehicle. Therefore, we will average the result by multiplying it by two, since not all elevators have failures every month.
Now, to convert 3.75 l of diesel into CO2 emissions, we must make a series of calculations. To do this, we turned to chemical technicians who gave us a hand: 1 l of diesel weighs about 850 g. It is composed, among other substances, of 85% carbon, which means that in a liter of diesel there are 722.5 g of carbon; the atomic weight of carbon is 12. To form CO2 in the combustion, two atoms of oxygen are used for each one of carbon; and as the atomic weight of oxygen is 16, doing some simple math. It turns out that 1,927 g of oxygen are needed in the combustion. Adding the 722.5 g of carbon plus the 1927 g of oxygen, we get that, as a product of the combustion of 1 l of diesel, 2,649 g of CO2 are emitted. (Annex 1)
Each vehicle per day per elevator emits: 2.65 kg CO2 x 3.75 l, an equivalent of 10 kg, two vehicles 20 kg of CO2 against 2.5 kg of CO2 caused by the elevator for the consumption of electric energy from the grid. We are not counting the energy savings due to regeneration when the motor behaves as a dynamo or the injection of other types of energy such as that produced by photovoltaic cells.
In any case, the conclusion is obvious: Our after-sales service pollutes eight times more than the elevator itself.
2. Contamination by Oil Spills
The second most important contaminant in elevators is hydraulic oil. According to international organizations, each liter dumped into sewers contaminates 1.000.000 l of water.
Hydraulic elevators are a real time bomb. They are installed by the hundreds of thousands, and each one has no less than 200 l of mineral oil in their tanks and cylinders. Many of them are buried, and we cannot know the condition of the liners that contain them.
In addition, cylinder and pump unit manufacturers recommend changing the oil every 10 years. It is unknown what is done with the hundreds of thousands of liters of oil that are moved and replaced every year.
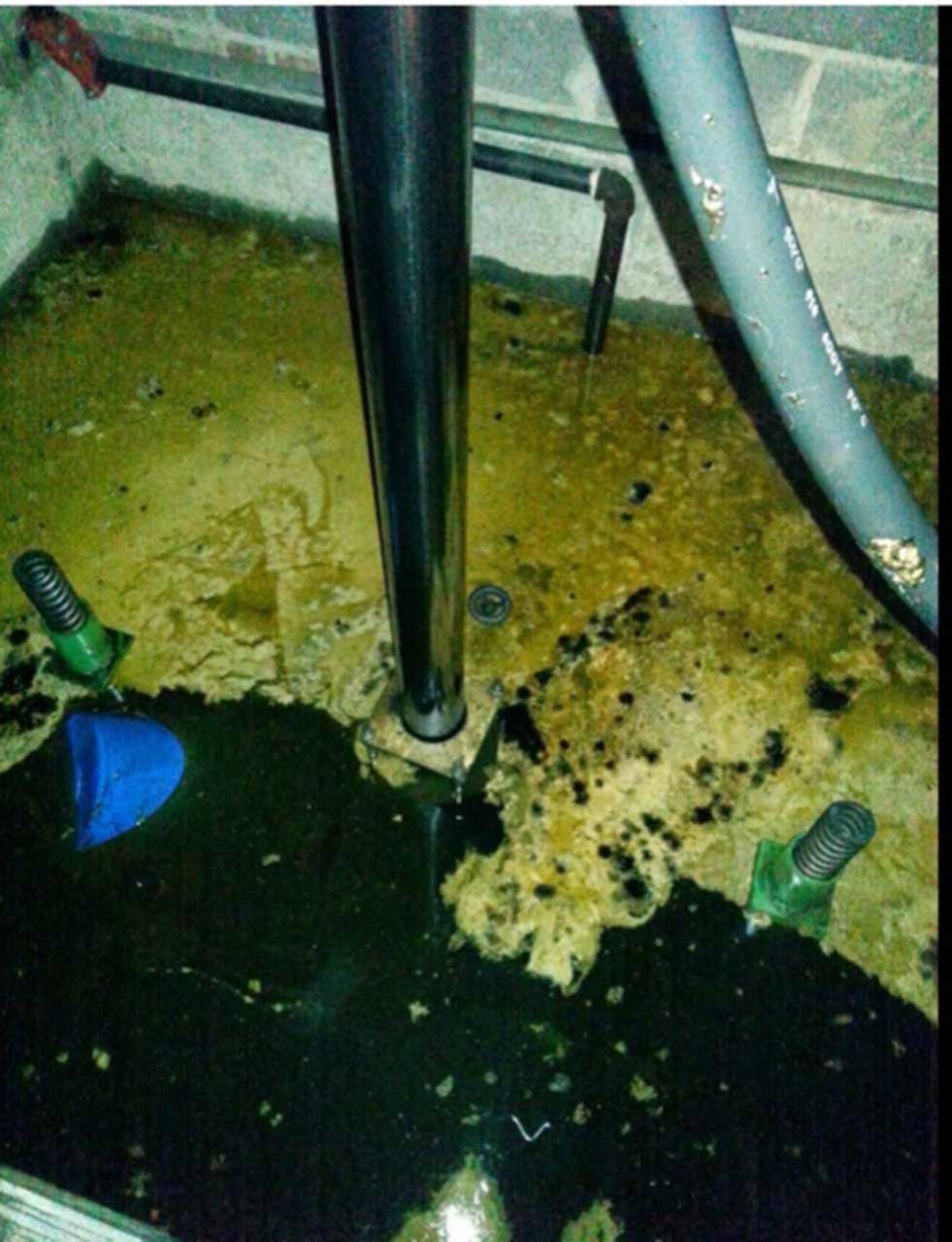
Hydraulic equipment not only has this serious problem of oil contamination but also high inefficiency since the pump requires a high-powered motor to lift the entire load, but also consumes the same energy whether it is running slow or fast, or whether it is carrying a large or small load. This is because the operation is based on a hydraulic circuit that, depending on the need, has valves that redirect the oil flow to the cylinder or to the reservoir tank because the speed regulation is done hydraulically.
In addition, although when the elevator descends it does not use energy from the power grid because it takes advantage of the potential energy of the ascent, this potential energy is transformed into heat in the oil when it finishes its downward ride. This effect does not allow it to recover energy as gearless equipment can, but in addition, in the event of heavy use, an oil cooling system must be added to the installation. This is of significant importance since the heating of the oil causes changes in its viscosity, which results in poor leveling of the floors and a high loss of oil lifespan.
As a counterpart to the heating of the oil due to high frequency of use, a problem of cooling of the fluid is generated by low temperatures and little use, causing a viscosity change effect also with the consequences mentioned in the previous paragraph. Of course, manufacturers have worked to solve all these problems: They have designed electronic valves, installed inverters, developed biodegradable fluids, etc., but it has not yet been seen much in the market due to its high cost.
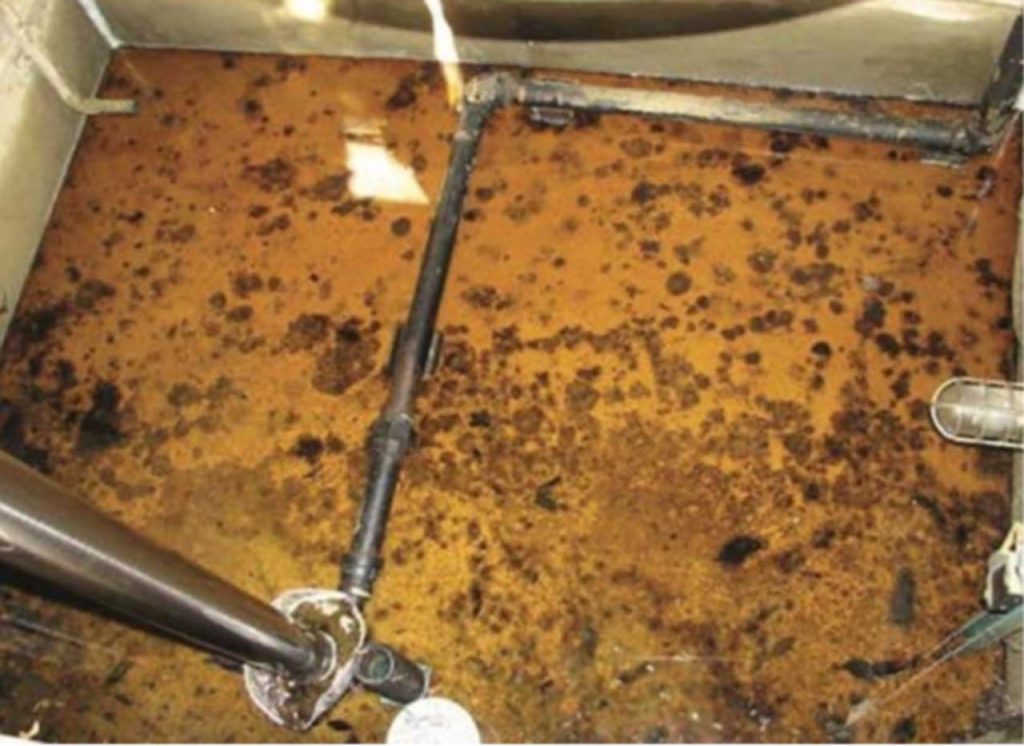
So, why use hydraulic equipment instead of machine-room-less (MRL) equipment? Because of its ease of transmitting efforts to the pit? MRL does this. Because of the possibility of battery-operated descent? MRL equipment not only descends on battery power, but it can also make several rides. Or is it because they can be accessed from three sides and take up very little space on a single shaft wall?
Well, it is time to present our development. An equipment MRL, which uses belts, occupies a single wall and requires the necessary space smaller than that of a hydraulic equipment; and the most important thing is that it is super friendly to the environment.
Product
To design our product, we established the following objectives:
- Low maintenance and claims requirements
- Longer service life of the elements
- Light and efficient machine
- Durable and less polluting components
- Easier and faster installation, systematization of the installation
- Industrialization of the equipment; Kanban system
- No need for lubricant or oil, or any other polluting product
- Easy adaptation for modernization of environmentally unfriendly equipment
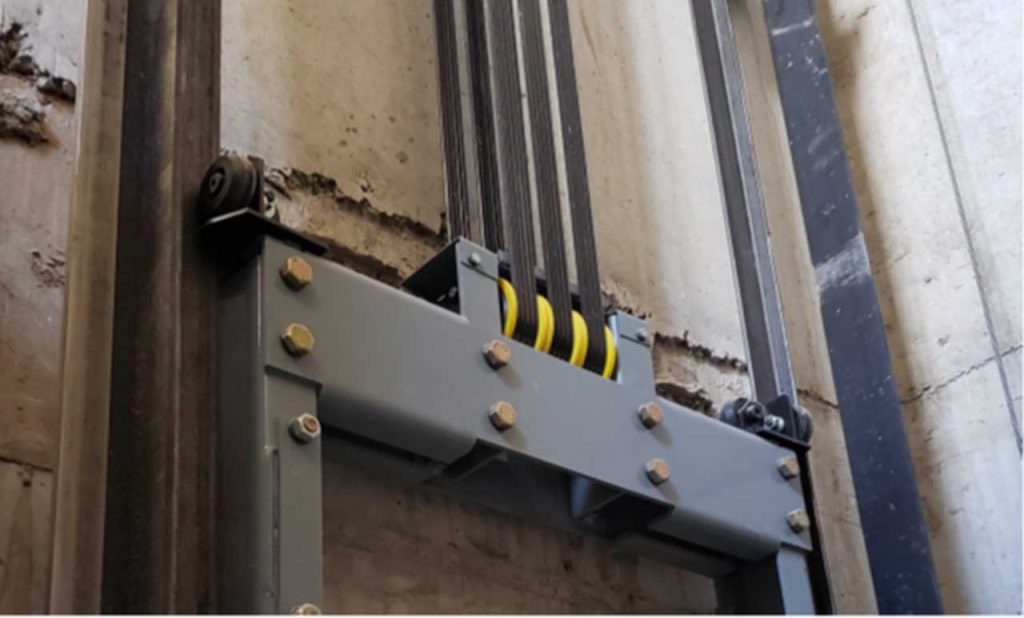
Therefore, we first started to search and study the different elevator traction belts in the world and the best machine to drive it. This is how we found a belt design that seemed to us to be very innovative and with qualities that surpassed the rest.
This belt has a design with grooves on both sides, which allows it to adjust well to both the traction sheave and the deflection pulleys. It does not slide to the sides, avoiding friction with the separators. In addition, having grooves on both sides works the surface of both sides.
Below are its characteristics and tests.
Drawing and Characteristics
Thickness measurement test in 10 million operations (See Annex 2, 3 and 4). Electrical resistance and thickness measurement test in 60,000 cycles in an experimental elevator (see Annex 5). The machine to which this belt is adapted is of compact design, with encoder type Heidenhain ERN1387, double reel disc brake and certified for involuntary movement.
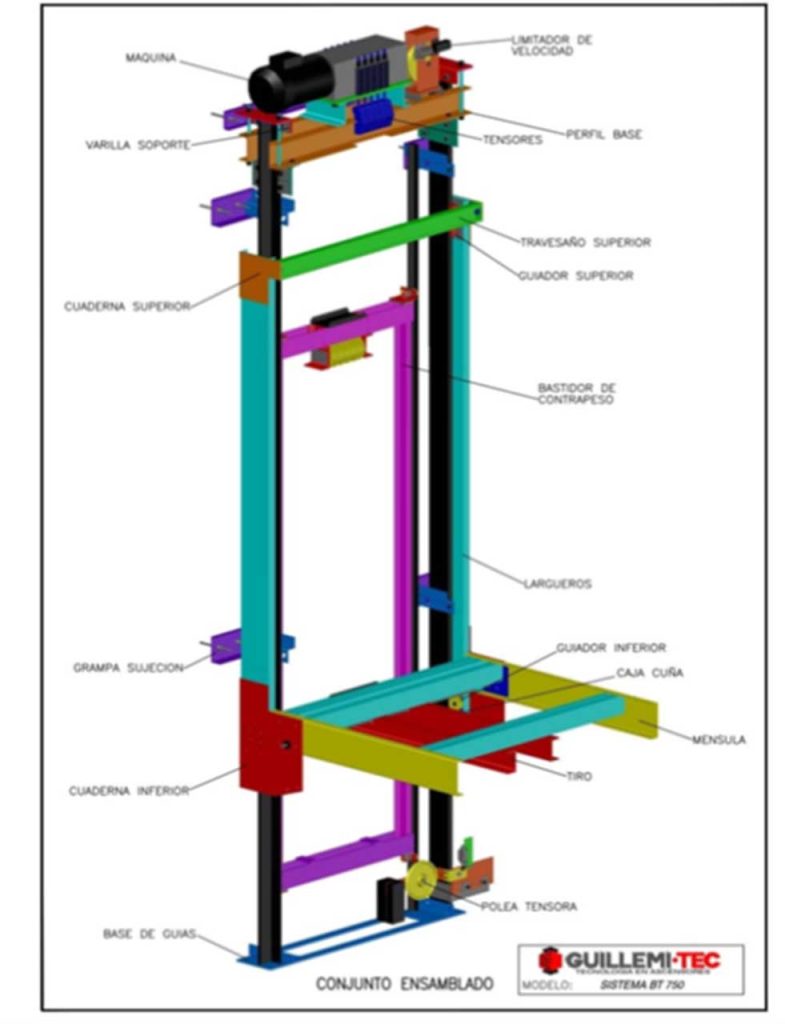
Machine
Testing of machine coupling at different frequencies and cycles of use (see Annex 6 and 7). Uncontrolled movement brake certificate (see Annex 8). With the basis of our suspension and traction element, we started looking for guides for the cantilever and the counterweight. We chose to use roller guides for both as it would allow us to have less frictional resistance, and we would not need grease or oil for operation.

Getting the guides for the counterweight was easy, but in the case of the cantilever, we had to go back to researching what we could find in the world. This is how we decided to install double wheel guides with an intermediate pivot — a great find. In regard to the parachute, we chose a conventional progressive one.
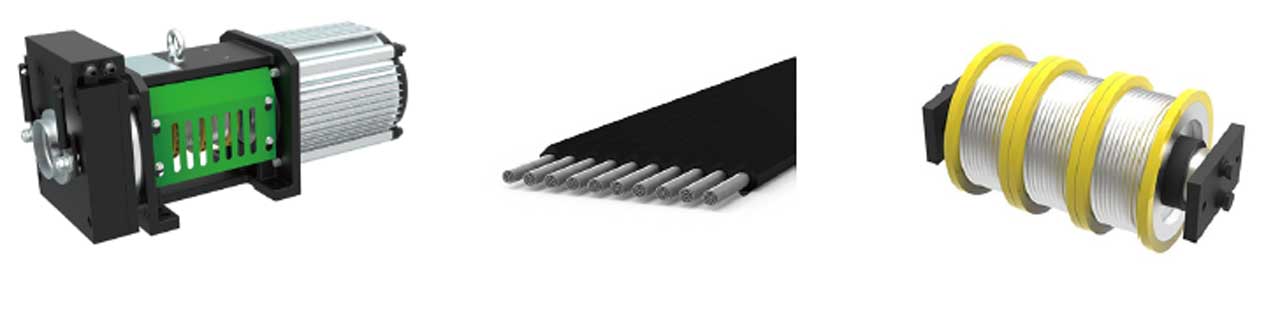
Car and Counterweight Rollers
Having all the components, we started the design of our cantilever together with Aeronautical Engineer in Engineering Elvio A. Heidenreich, PhD. We made all the resistance tests of both the cantilever and the machine base by means of the finite element method.
Finally, to complement the equipment and to be able to industrialize it, we contacted Wittur Argentina, and together we designed the complementary elements and the manufacturing systematization, using the Kanban system. Today, we can say that the equipment is produced with high manufacturing quality and express delivery.
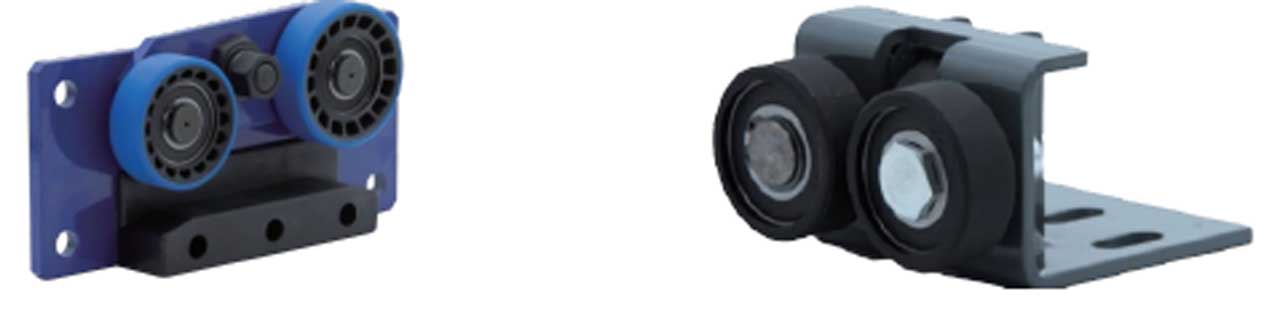
Human Resources
For several years, we have been working on a management and control system for the entire company’s operations regarding the complete cycle from sales to after-sales. During the 2020 pandemic, we accelerated our plans, and today we can say that this program is 90% implemented.
We estimate that we have reduced the carbon footprint caused by administrative human resources by 50%. Nowadays, salespeople, administrative staff, designers and technical representatives perform their tasks in half of their working time, and have the other half to dedicate to other activities.
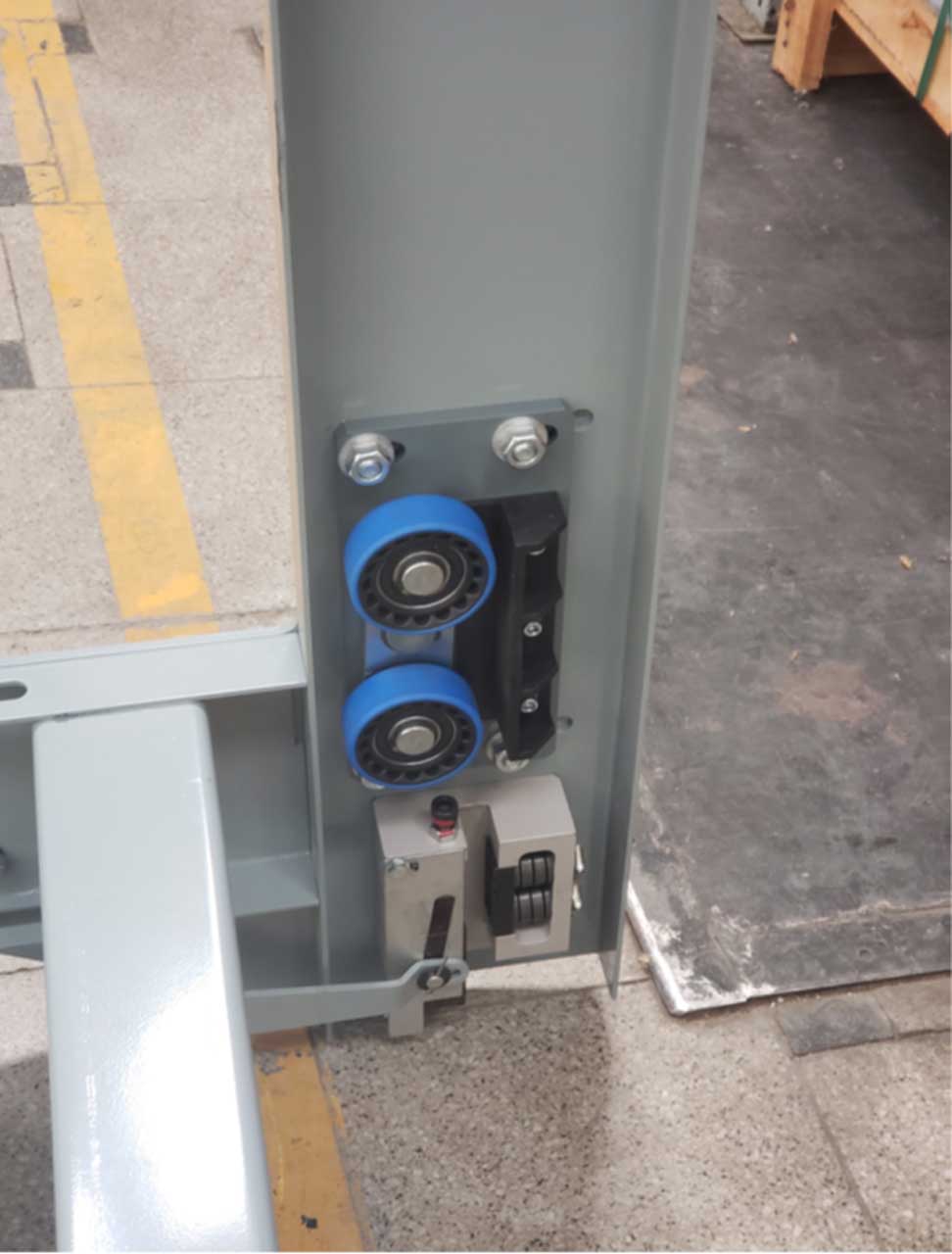
Savings
Administrative labor savings:
- 280% more quotations done
- 192% more contracts
- 63% time savings
- 98% error savings due to mistyping
- 50% WH reduction due to the increase in productivity
Kanban savings:
- 8% annual productivity increase
- 96% scrap saving thanks to nesting
Just in One Click
New Equipment
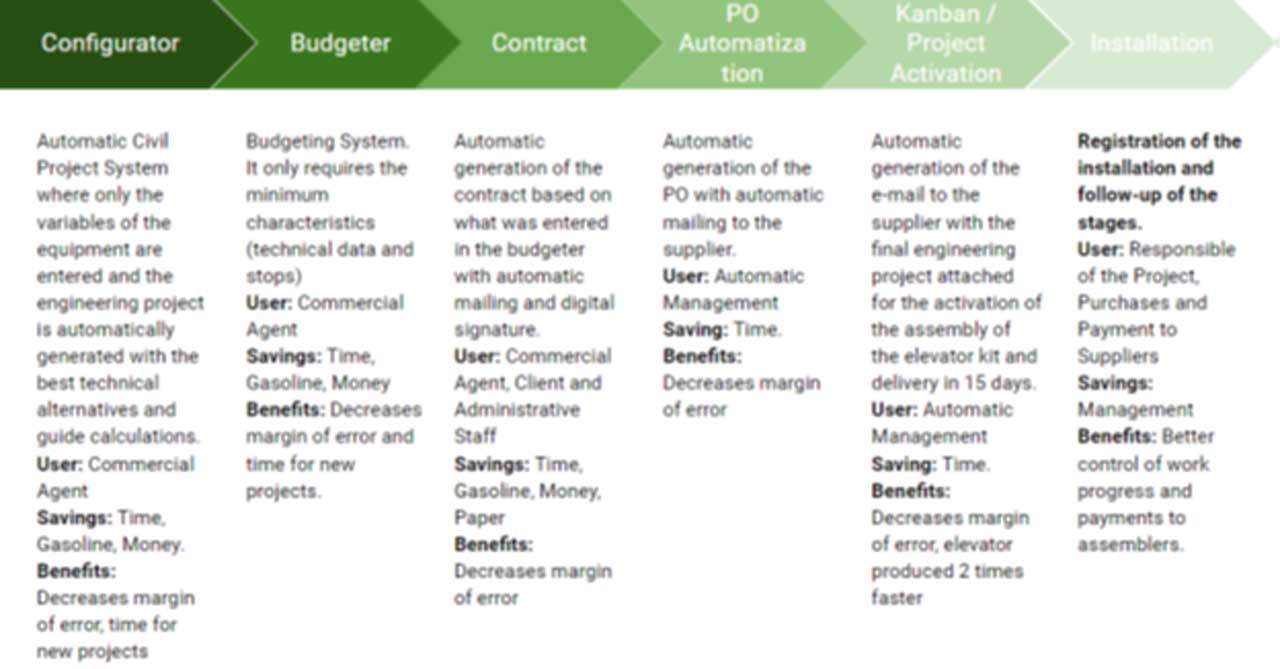
New Maintenance
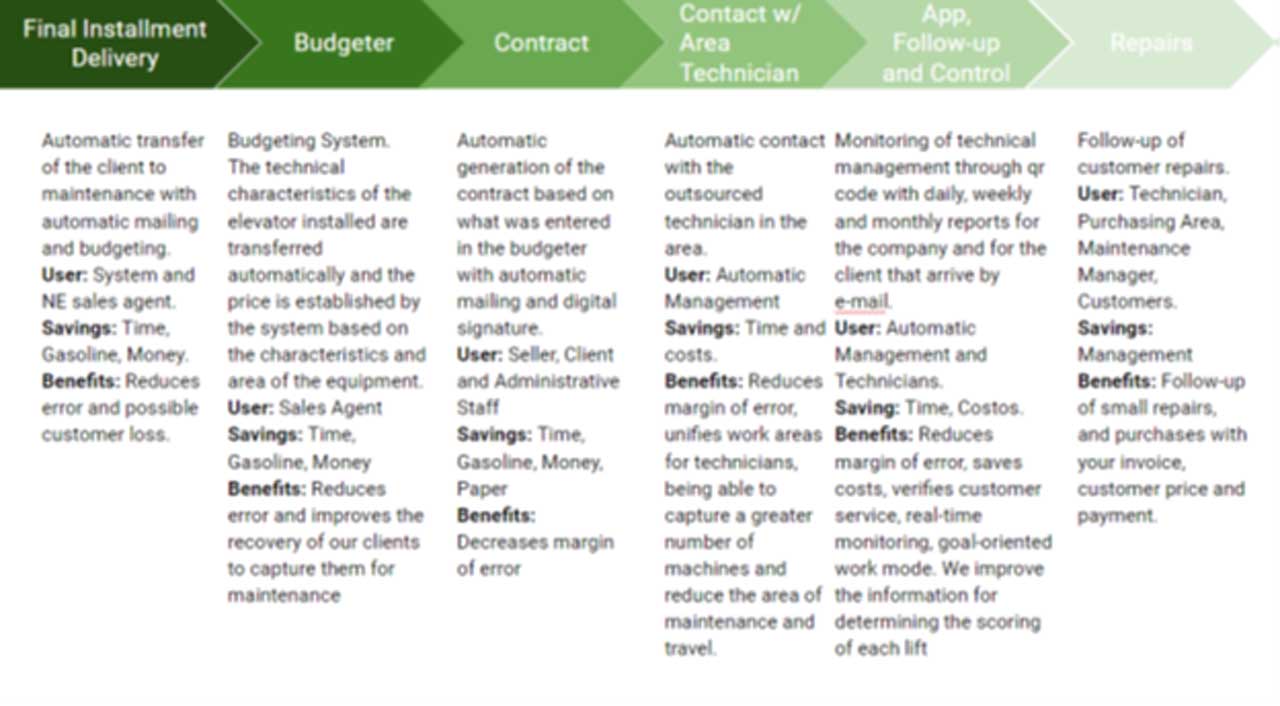
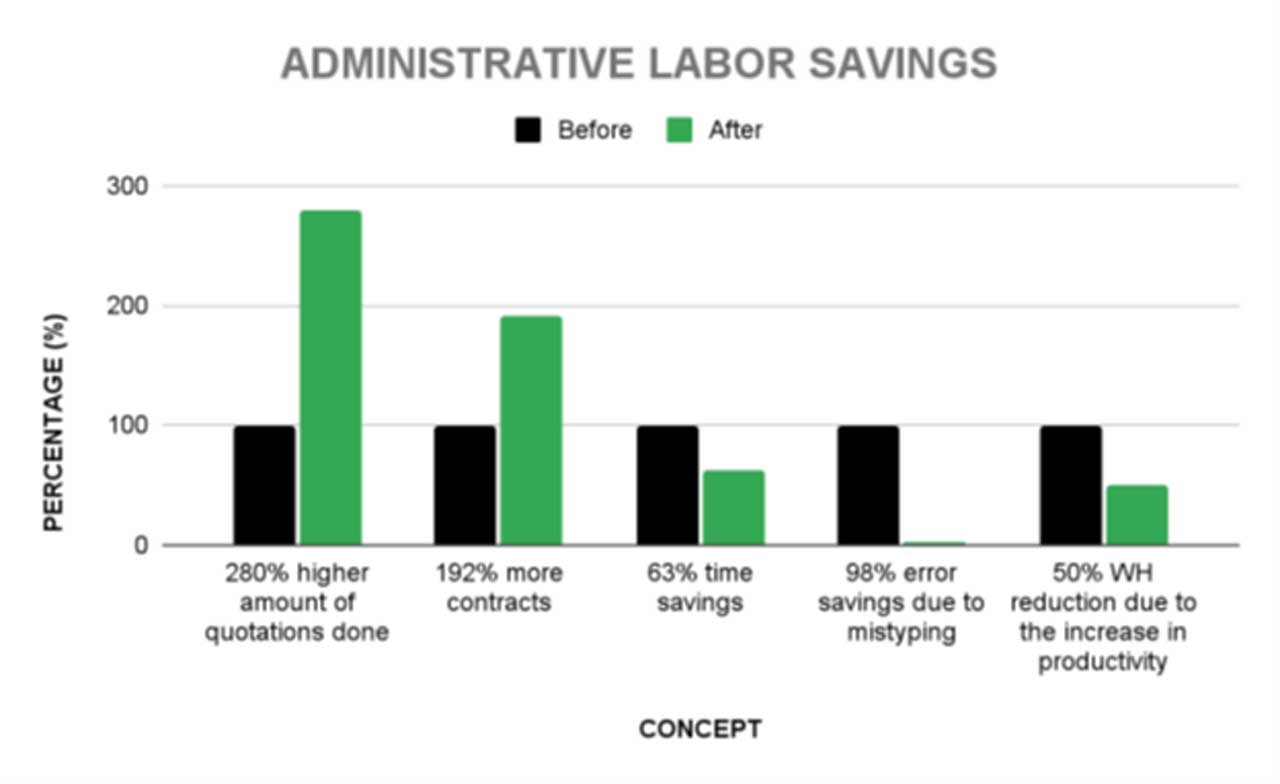
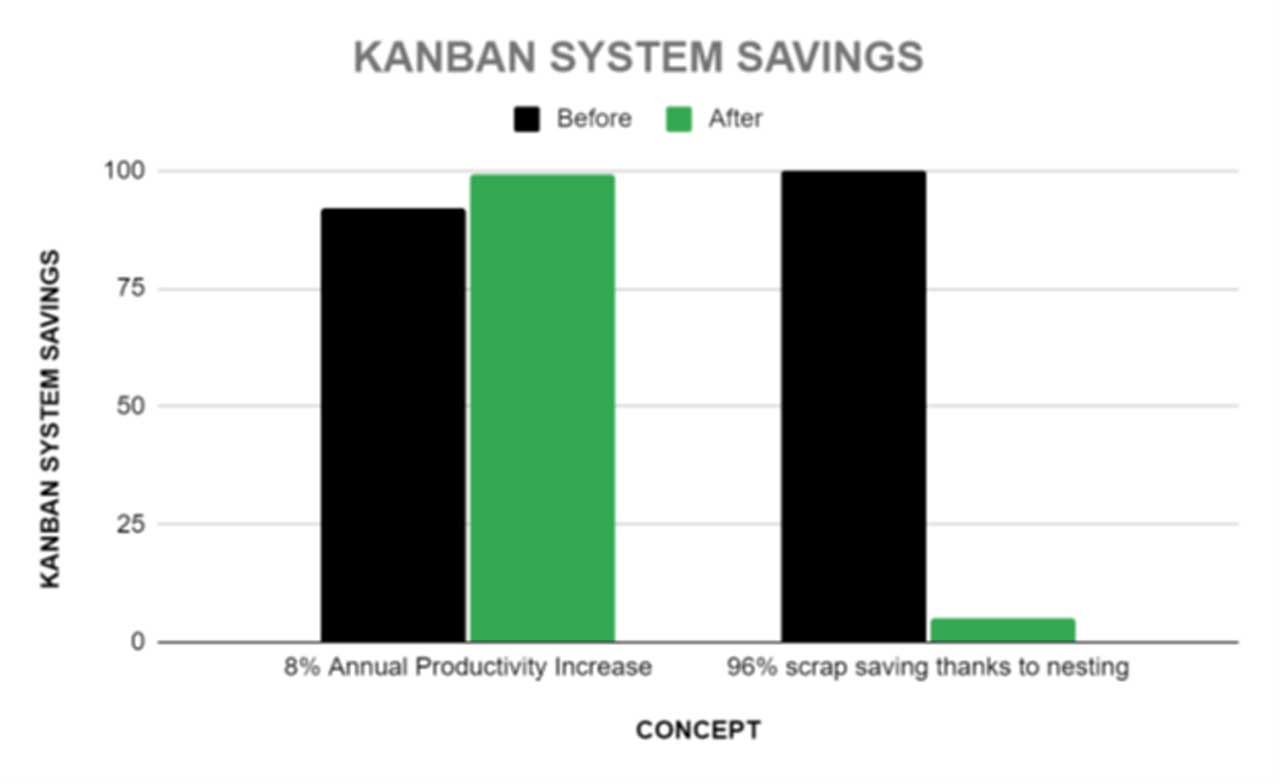
Savings by Digitizing Documentation: (engineering plans, works and maintenance budgets, signing contracts, work orders, purchase orders, payment orders, reports, etc.)
Digitalization savings
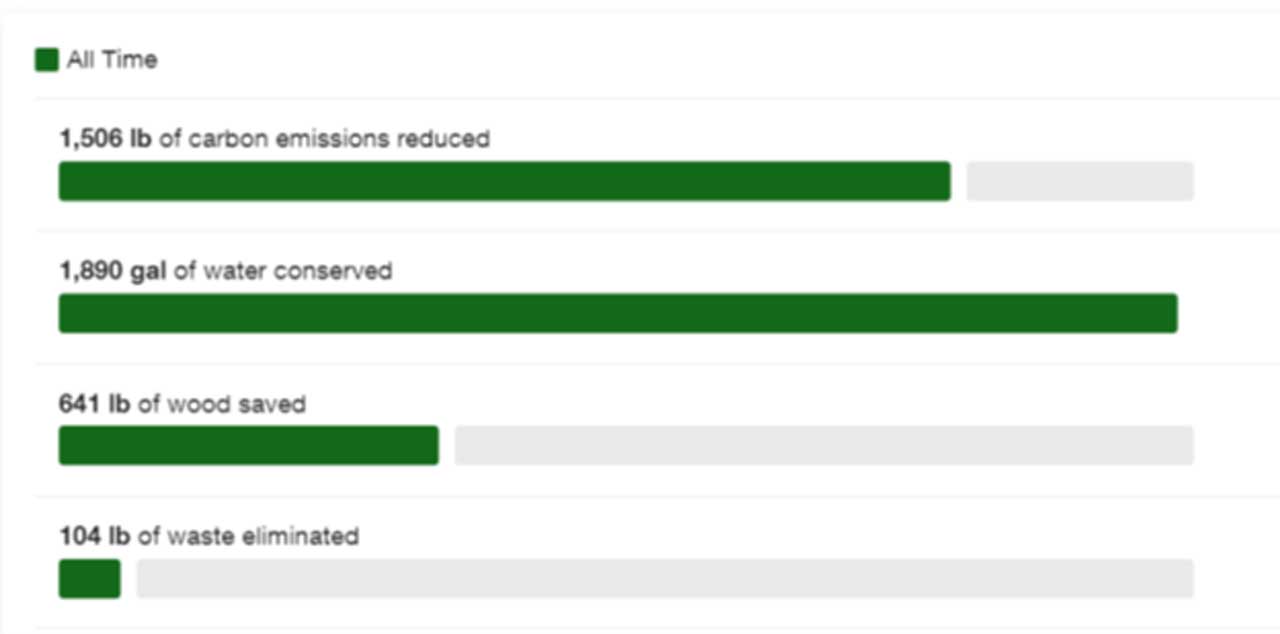
Conclusions
It is necessary to design and produce elevators with a low level of claim for damages, minimum maintenance, low polluting materials, adaptability to different shafts and suitability for mass-production. For all these reasons, it is imperative to use suspension means of the belt type with a much longer service life and safe monitoring compared to traditional traction cables, and the advantage of being able to use very small traction and deflection pulleys.
These traction belts allow us to use permanent magnet machines of light structure that facilitate installation, shorten installation time to one-third and require minimum space in the shaft, avoiding larger constructions with the consequent contribution to the environment by not requiring important concrete structures as it is a self-supporting system without a machine room.
Another fundamental issue demonstrated in the presentation is the importance of not using grease and oils to avoid the greasing of guides and lubrication of components. A great contribution to the environment, the system provides cleanliness in the shaft and minimum maintenance.
Hydraulic equipment should be adapted to new technologies so that they are environmentally friendly and do not jeopardize the future of the next generations. Those using hydrocarbon-derived oils should be banned; biodegradable fluids and more efficient systems must be developed to save energy.
We had great intelligence to build this civilization. Let’s use it now to save it.
Annex 1
Diesel Combustion
DIESEL DENSITY: 850 gr/lt.
DODECANE MOLECULE: C12H26
MOLAR WEIGHT:
- H: 1 gr/mole
- C: 12 gr/mole
- O: 16 gr/mole
Stoichiometry:
C12H26 + O2 → CO2 + H20
Equivalence: C12H26 + 37/2(O2) → 12CO2 + 13H20
Since we cannot divide the oxygen atom in two, we have to multiply the rest of the elements and the final formula would be:
2(C12H26) + 37(O2) → 24CO2 + 26H20
2(C12H26) → 850 gr
Now we need to calculate the molar weight:
2(C12H26) = 2(144 gr/mole + 26 gr/mole) = 340 gr/mole
24(CO2) = 24(12 gr/mole + 32 gr/mole) = 1056 gr/mole
CO2 Emission Per Diesel Liter
To calculate the equivalent in grams of CO2 emitted, the formula would be:
850 gr _____ 340 gr/mole
X _____ 1056 gr/mole
X= (1056 gr/mole * 850 gr)/340 gr/mole = 2640 gr = 2,64 kg of CO2 emitted per liter of diesel.
CO2 Emission Per Day from Maintenance Vehicles
*This analysis is carried out on page 2 where we develop the carbon dioxide pollution from an elevator vs. the one of the vehicles that maintains them.
1 elevator consumes 3.75 l/day (from one car)
1 elevator needs at least two visits per month
CALCULUS = 2.64 kg/l emitted * 3.75 l/vehicles/elevator * 2 vehicles/elevator = 20 kg of CO2 emitted per day from our vehicles assigned to the elevators.
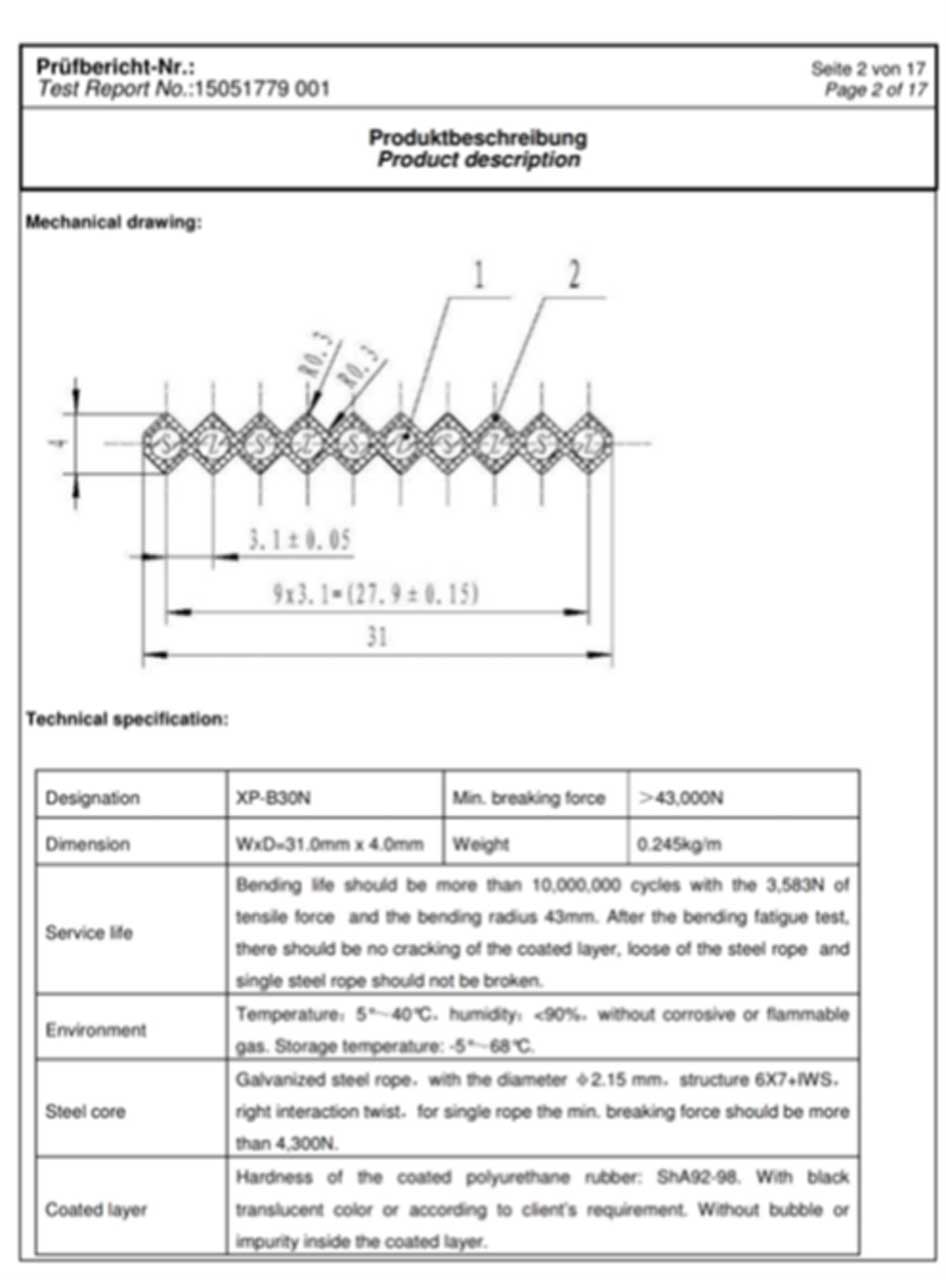
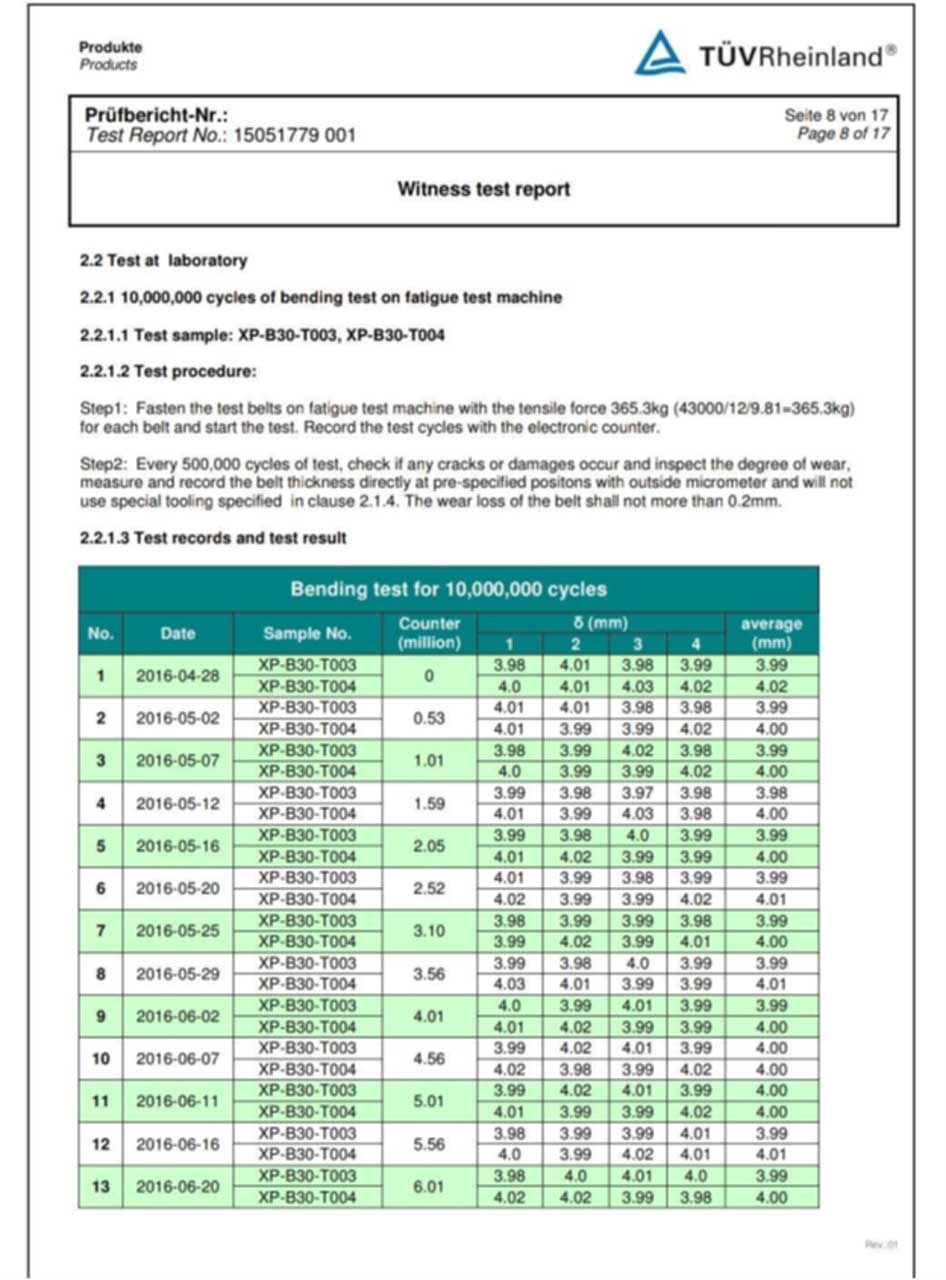
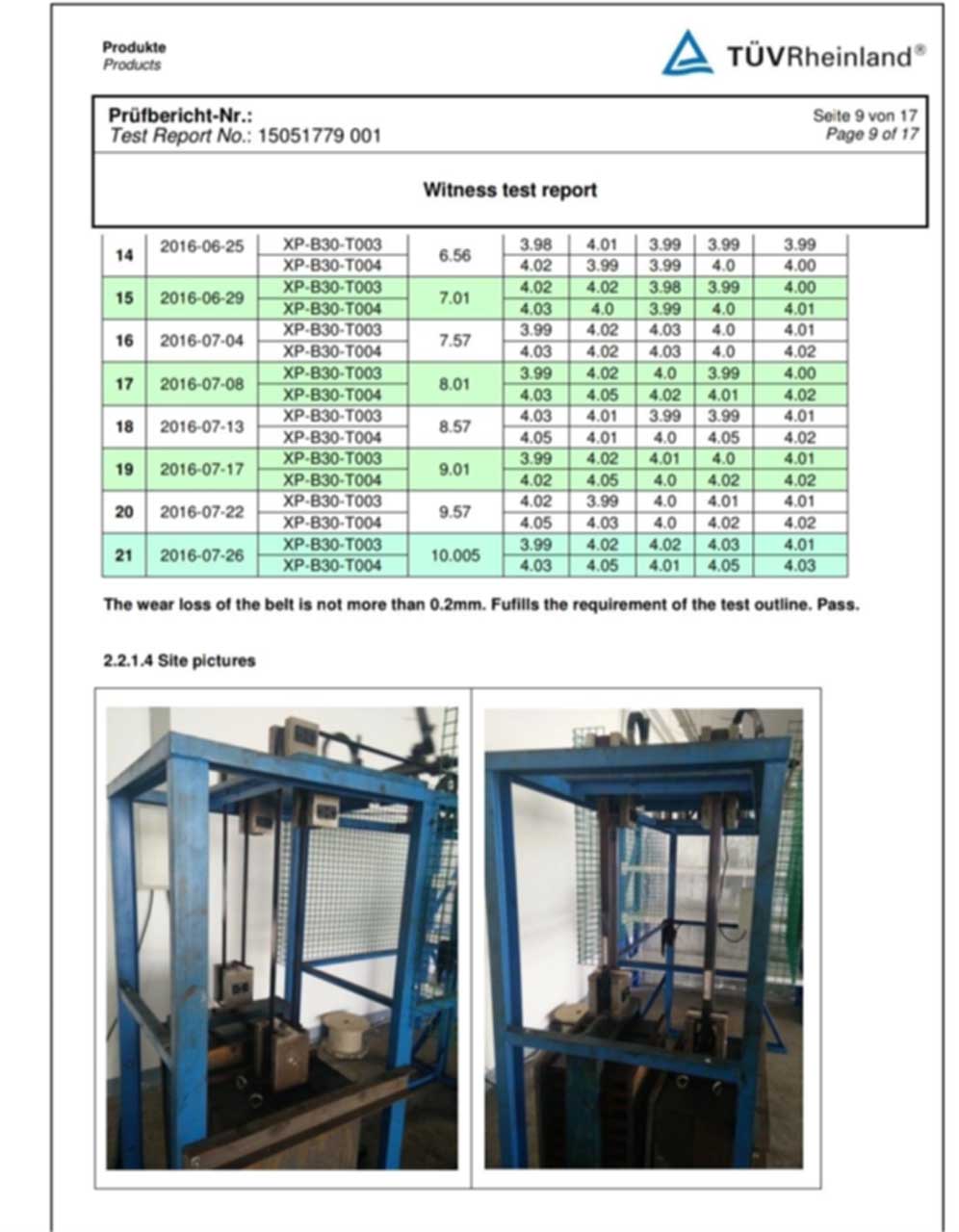
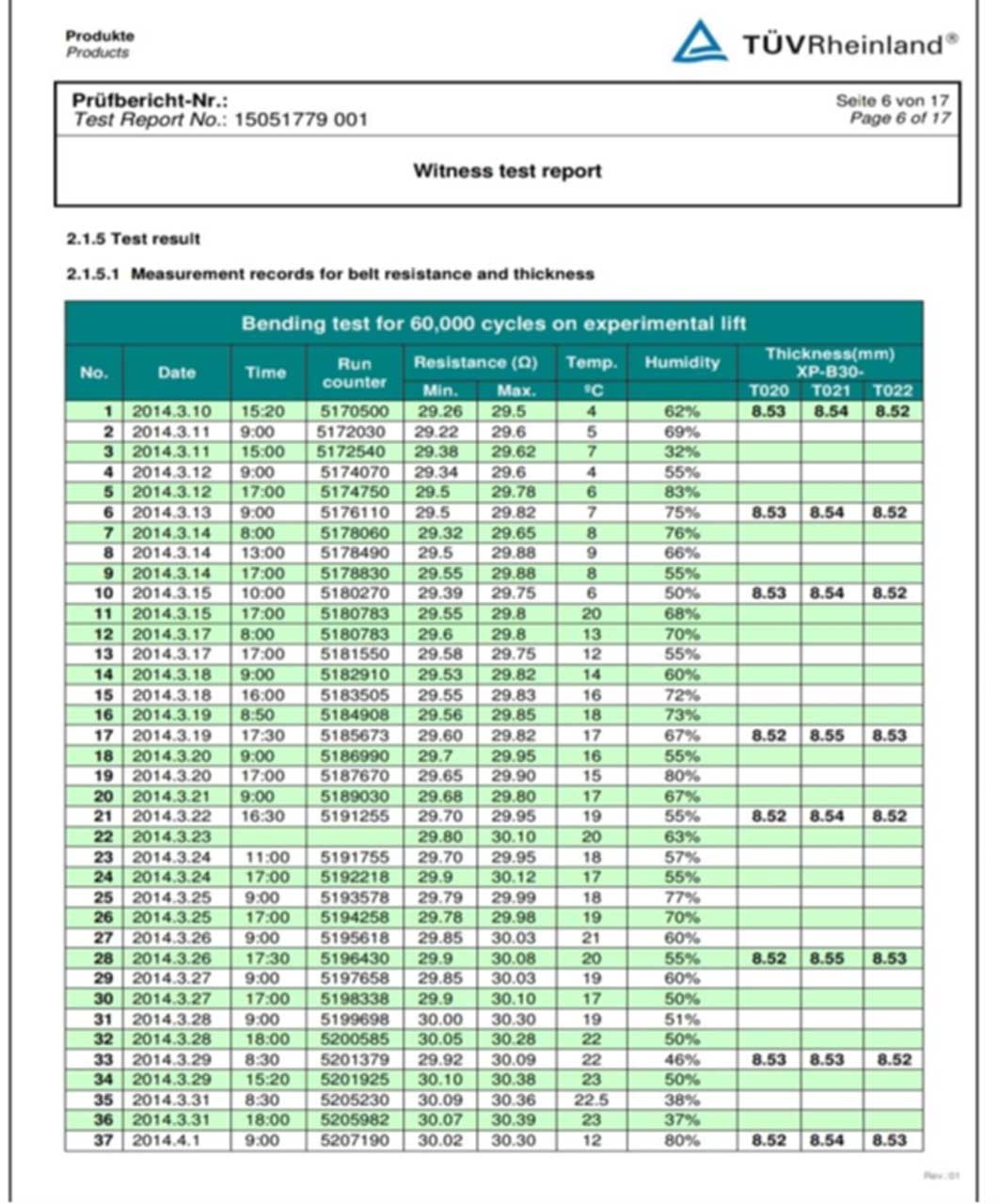
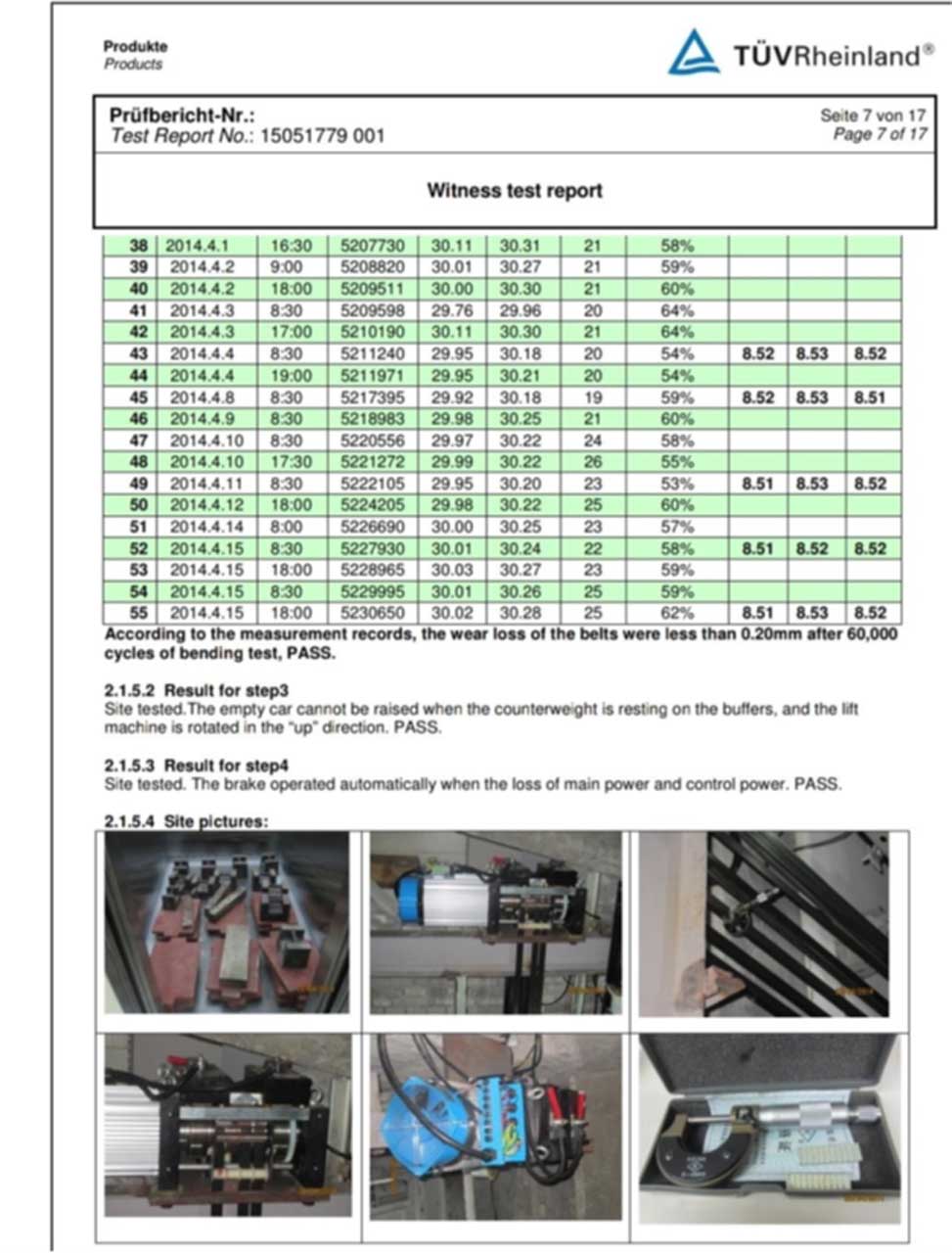
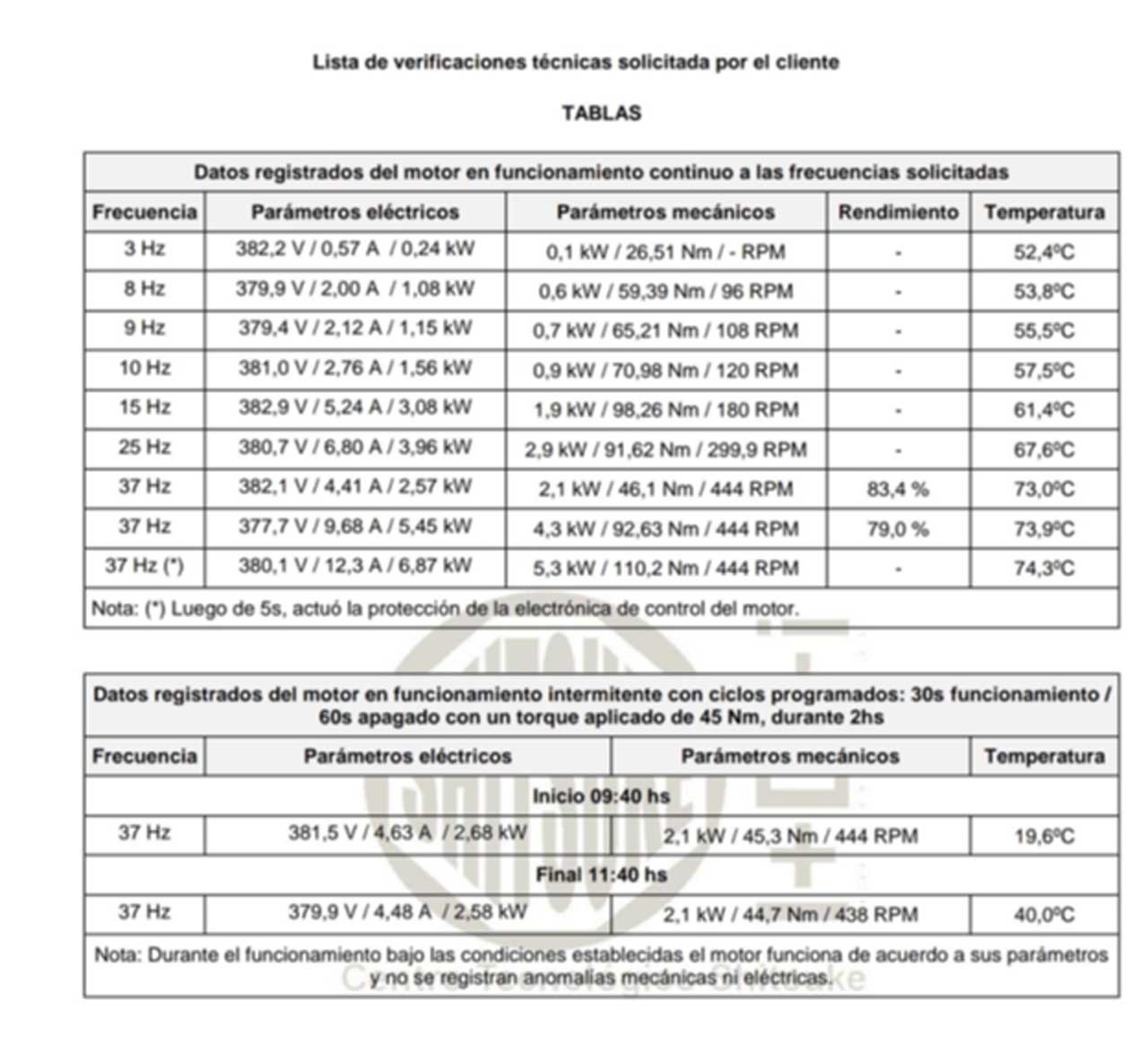
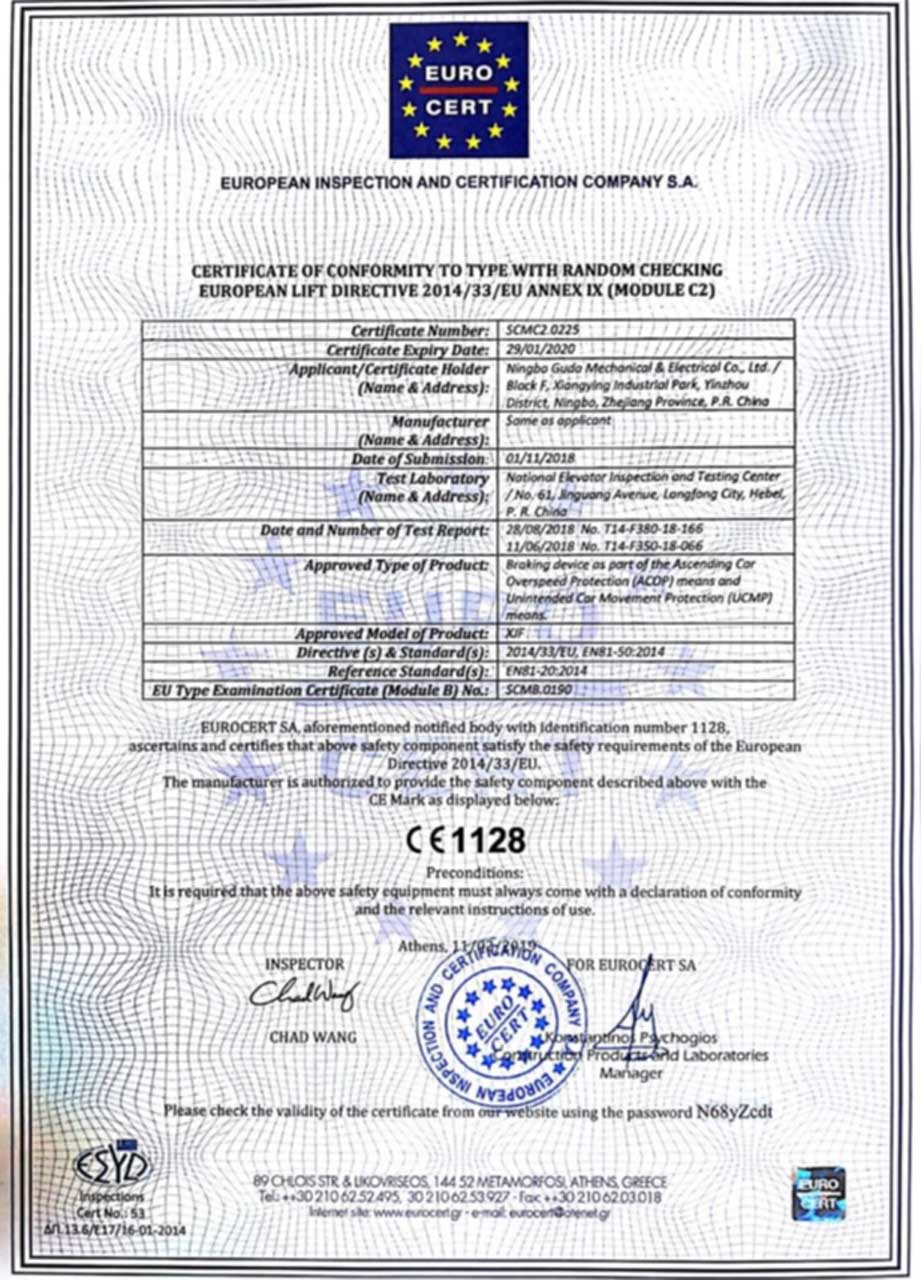
Get more of Elevator World. Sign up for our free e-newsletter.