Mission Accomplished
Mar 1, 2018
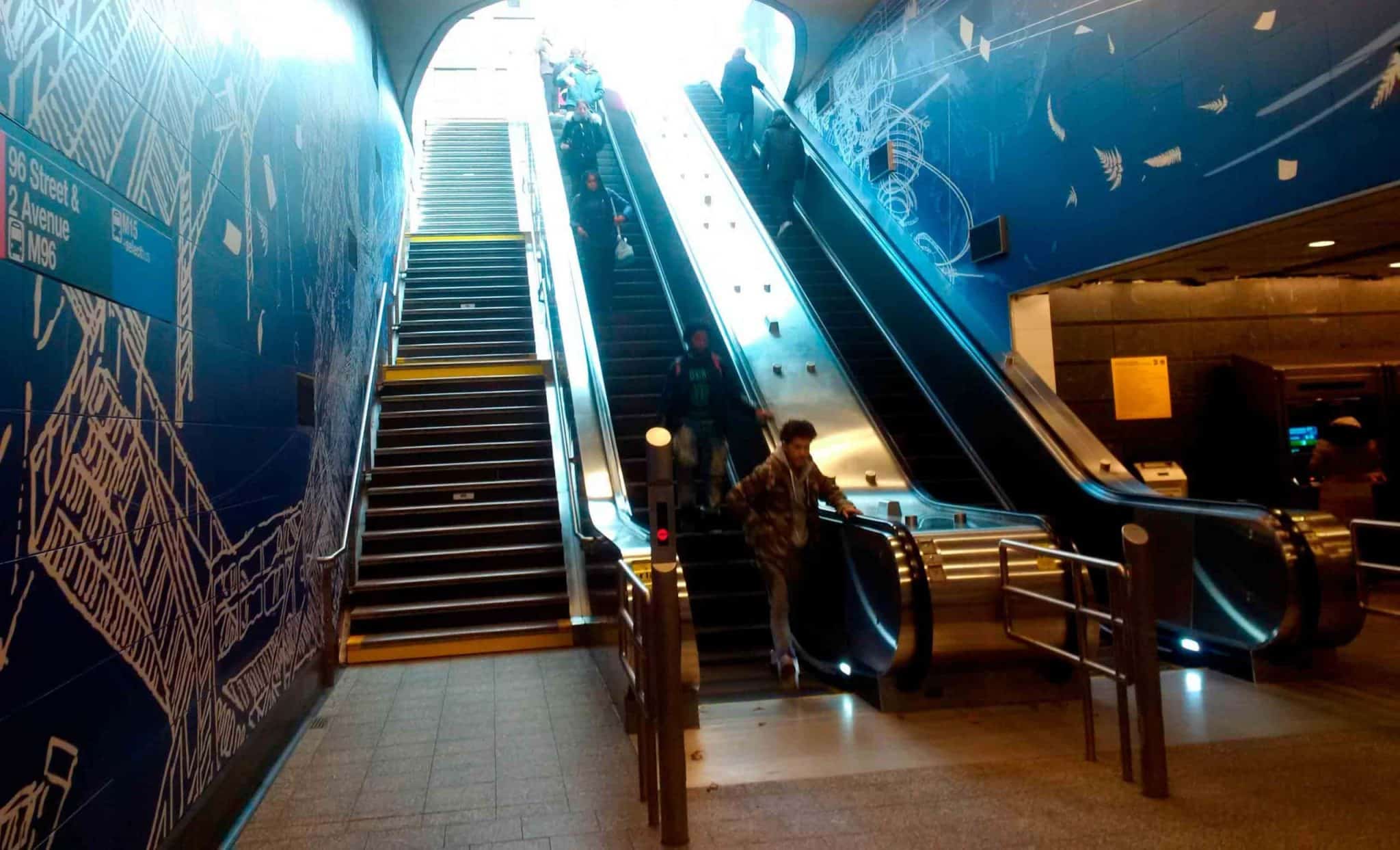
EW gets an inside look at the amazing KONE escalator systems in stations along NYC’s Second Avenue Subway extension and at Hudson Yards.
One hundred years from now, descendants of those who were on the Second Avenue Subway Construction Management Committee in New York City (NYC) will be able to see the names of their forebearers on several plaques erected by New York Governor Andrew Cuomo to mark the completion of key parts of the Metropolitan Transportation Authority’s (MTA) new Second Avenue line, names that include MTA officials, general contractors and employees of vertical-transportation (VT) companies such as Schindler and KONE who were instrumental in bringing the projects to fruition. Providing a connection between the Upper East Side and the rest of Manhattan, the line is the result of a century of planning, “a few fits and starts, and a race to the finish line.”[1] — a race in which the VT industry played a critical part. From KONE, players included Executive Vice President for KONE Americas Larry Wash, Installation Manager Joseph Connolly, District Manager Justin Tomasino and Construction Manager Gerry Matawa. ELEVATOR WORLD was recently treated to an exclusive, in-depth tour of the escalator systems by Matawa at 34th Street/11th Avenue (Hudson Yards), and 63rd, 86th and 96th streets.
The systems, each in subway stations that are literal works of art in themselves, represent an intricate, monumental effort that unfolded somewhat like a symphony orchestra. The process had many parts and players, from company executives and high-ranking politicians to construction helpers. A variety of trades — welders, pipefitters, carpenters, electricians, riggers, logistics and information-technology specialists — had to coordinate precisely for the projects to be a success.
The tour began at the Hudson Yards station (separate from the Second Avenue projects), which boasts a pair of inclined lifts that are highly unusual in a U.S. public-transit system, five high-rise escalators that include two of the fastest in the subway system at 120 fpm (versus 90-100 fpm), two low-rise escalators and several elevators.
At this station in particular, installations involved a remarkably high level of ingenuity and perseverance. They called for problem solving on a level rarely seen: Seemingly unreachable deadlines were met, nearly 100 escalator truss sections weighing approximately 19,800 lb. were carefully and precisely lowered to depths the equivalent of a 14-story building, and, in the case of the inclined lifts, details had to be worked out to coordinate the shipment of components from Italy to NYC and wed Italian hardware with an array of components and software made in the U.S. KONE Construction Foreman Don Vitale calls it “the most challenging but also the most rewarding” job he’s worked on in his 30-year career.
Matawa states:
“Its units were bigger than what had been done in a very long time and went into a station that was much deeper than usual. The logistics were extremely difficult, and had it not been for the hundreds of meetings I had with the frontline team, which included general contractor Skanska, this project wouldn’t have turned out as well as it did. We brainstormed with Skanska to look ahead and plan weeks in advance. It’s like a Rubik’s Cube: If you don’t turn every piece the right way, then all the colors aren’t going to line up. The key was communication, cooperation and everybody pulling on the same side of the rope.”
A Neighborhood in Flux
The station will serve the Hudson Yards development (p. 136) on the far West Side. This transformative project will bring multiple skyscrapers and tens of thousands of people to an area regarded as an emerging “city within a city.” Development is already spilling out from the boundaries of Hudson Yards proper, as existing buildings in Hell’s Kitchen and beyond are being renovated, or torn down and replaced.
Matawa said when KONE was first awarded the job a few years ago, he failed to understand why the two main escalators needed to be so big and travel so fast. He elaborates:
“I was concerned about the elderly folks and how they were going to transition on and off. [Members of a strategic planning team] pointed out there are going to five, 50-story-plus buildings here, but it still didn’t register. Then, once we finished this job, and they started ripping down this and putting up that, and I realized the [nearby] Javits Center is about to double in size, I said to myself ‘Oh, my gosh. There are going to be thousands of people infiltrating this area who are going to use this VT system to go wherever they need to go, every day.’”
The support system for the inclined lifts consists of 11 bolted-together sections, each weighing 3,800 lb. Lying flat, each section is 200 ft. long. Fully assembled, the support system weighs approximately 42 T. The system is powered by 100-hp machines manufactured by Hollister-Whitney with yellow steel bases custom made at the KONE factory in Coal Valley, Illinois. The huge trusses, also manufactured by KONE, were lowered into place using a custom hoist ordered by Matawa from the U.K. and a wheeled dolly system he had built at the Coal Valley facility.
Matawa said coming up with that system was one of several times he had a feeling akin to those involved with the Apollo 13 space mission — doing something that seemed out of the realm of possibility. He states:
“There were a lot of people behind that concept, and they kept saying to me, ‘Are you sure this is going to work?’ And I thought, ‘It has to work; there is no other way to get them down there. Remember, you’re in a tube, a tunnel. A whole bunch of people said, ‘Gerry, what is Plan B?’ I said, ‘I don’t have a Plan B, because Plan A has to work.’”
For many months, Matawa endured sleepless nights, going over the process in his head like a video. When the day came in September 2015 that the system was put into action, it worked unbelievably well, he said, almost like “poetry in motion.”
Italy/U.S. Hybrid
The Hudson Yards station feature that grabbed the most headlines was the inclined-lift system, with cars manufactured by Maspero of Italy. The custom-designed pair of units evoked a few unfortunate descriptions, including “mutt” and a “Ferrari with a Chevy engine and Ford transmission.”[2] Although they had issues along the way, including failing the first factory test in Italy in July 2014 following initial integration of the U.S.-made parts, the units have run well since they debuted.
Matawa and Vitale feel they are a success and that any derision is undeserved. The decision to use parts from U.S. manufacturers was based on the MTA being able to easily get replacement parts. Had they come from Italy or elsewhere, the process would be far more complex and longer. Each lift holds five wheelchairs or 15 standing people, and represents a model of handicapped accessibility in a system often criticized for lack of it. Like the high-rise escalators, the lifts are powered by Hollister-Whitney machines, but these are 40 hp. They travel considerably slower than the high-rise escalators, at approximately 100 fpm.
Those who built the inclined-lift system went the extra mile as far as damage prevention and emergency management were concerned. The cabs are outfitted with discrete security cameras and an invisible vandalism-prevention material: Up to five sheets of clear, heavy plastic cover glass surfaces and are removed, sheet by sheet, after regular (or intentional) scrapes and scratches occur, leaving the glass as good as new.
If evacuation is necessary due to a power outage or terrorism threat, a software program developed by Winslow Soule’s IDS/LiftNet of Chicago (p. 116) stops all down escalators and leaves certain “up” ones running. Using battery-backup power, the inclined lifts can make up to eight round trips to evacuate wheelchair users, rather than the typical one or two trips, Matawa says.
Unconventional Cable System
In conventional elevators, all power and signal information is transmitted through traveling cable mounted in the hoistway. But the inclined lifts are no traditional elevator system, so a different solution was in order, Matawa says, pointing to a 200-ft.-long structure in a trough between the two lifts that looks and moves like a giant biomechanical black snake. Those involved in the project call it “the caterpillar.”
Vitale observed the caterpillar is very involved, elaborating:
“We basically had to build a shelf and track system for it that would hold 20 different cables. It was very time consuming, because each cable has 10-20 different wires. Unlike a traditional traveling cable system, the ‘caterpillar’ is attached to the elevator itself and rolls with it.”
Machine Rooms
Matawa and his team are proud of all of the stations’ machine rooms (some of which aren’t rooms at all), noting the symmetrical pipework, which, in the Hudson Yards station, looks more like an Art Deco architectural element than a utilitarian system. Matawa states:
“Richie Coursin (since retired) and his helper, Frank Lucci, were the masters of the pipework on this project. Coursin was replaced by Pat Kopf, who is doing equally well. The pipes that we are talking about are 2-in. conduit. They are not only large, but thick, heavy and hard to bend. You need special equipment, but there’s an art to it. You are essentially plugging in cables, piping and wiring to make the thing work, but that doesn’t mean it can’t be neat and clean and have some sort of symmetry to it.”
A Look at Stations to the North
The KONE escalator team handled installation at the 63rd, 86th and 96th street stations simultaneously.
The three high-rise escalators that serve the 86th Street station are as big and powerful as those at Hudson Yards, but its machine “room” is something else altogether. Because of space constraints, three pairs of 50-hp machines had to go in the escalators’ upper pits. “Picture a very small, compact version of the Hudson Yards station’s machine room,” Matawa says. “Those powerful motors were built in the upper pit, so the pits had to be very long. We squatted them and made them lengthy.”
So much is special about the new stations — the stories from the people who worked on them and their uniqueness. The walls (and, in some cases, ceilings) of each are decorated with colorful mosaics by world-renowned artists that represent “the largest permanent public art installation in New York state history.”[3]
“It’s so cool,” Matawa says of the stations’ design. He points out artist Jean Shin’s glass mosaics at the 63rd Street station that used historic photos to create an homage to the elevated girders that were dismantled in the 1940s and 1950s. At 86th Street, he points out a mystifying feature of the mosaic portraits by Chuck Close that look abstract to the naked eye but snap into sharp focus when viewed through a camera-phone screen.
Each station to the north of Hudson Yards presented its own challenges. Dating to the 1960s, the 63rd Street station is among the subway system’s deepest at 155 ft., and its latest upgrades, completed in January 2017, involved propping up and stabilizing a high-rise building above it. The station is outfitted with six escalators. 86th and 96th streets boast 10 escalators each for three entrances/exits, and all stations have elevators, bringing them into compliance with the Americans with Disabilities Act of 1990.
Back at the Hudson Yards station, Matawa points to the massive beams supporting the inclined lifts. All the people who worked on the job signed their names or initials to commemorate the job’s completion. He pauses to snap a picture of the initials “S.P.M.” for his wife, Kathy. They were written by the couple’s son, Stephen, an escalator installation expert-in-training who passed away unexpectedly in 2017 at age 42. He is glad his son got to see the completion of this one-of-a-kind project but sad he won’t be involved in future ones.
As 2018 rolls along, so does the city and its many major projects. These, of course, include VT, and Matawa is excited to continue to be involved. These days, he can likely be found having sleepless nights over the escalators that will be in the new Moynihan train station, which will be bigger and grander than Grand Central. “When you see a project like this in its infancy, where there’s just a big, empty hole, then how you get from here to there, it’s pretty amazing,” he says.
The KONE team’s work on the Second Street Subway extension earned praise from many people, including Wash, who said:
“I’m incredibly proud of KONE’s NYC district team for efficiently completing the Second Avenue Subway addition. The team received personal thanks from local officials for completing the project on an escalated schedule. KONE is proud to enable a new, smooth commuting experience for hundreds of thousands who traverse the Second Avenue Subway station every day.”
Heroism on the jobsite
A few weeks before Christmas 2017, during rollcall for the daily meeting of the KONE team working on the 86th and 96th Street station escalators, approximately half the team members were missing. As 7 a.m. turned into 7:30, installation expert Gerry Matawa began to worry about the always-punctual employees and set out to investigate. He found Fred Guzman, James Montario and the rest of the men in a nearby diner that was, at this point, filled with medical and police personnel. That’s because Guzman and Montario had just saved a waiter’s life, performing the Heimlich maneuver and resuscitating him after he began to choke. “[Guzman] was in the military and served tours in Iraq and Afghanistan, and [Montario] was a member of the Massapequa Fire Department, so the two of them knew exactly what to do,” Matawa says.
Their efforts earned them kudos in both the KONE and International Union of Elevator Constructors newsletters, as well as a promotion for Montario from assistant to chief of the fire department. Matawa says the recognition was very well deserved, stating:
“In the midst of the intensity of trying to get to the finish line and meet the governor’s promise to the public, two heroes arrive. We get calls on the weekend and in the middle of the night. We’re always busy doing something, but these guys are also still plugged into society and the community at large, and stop and do what they can to help.”
Get more of Elevator World. Sign up for our free e-newsletter.