NEIEP Holds JAC Seminar and Lab Showcase in San Antonio
Oct 1, 2013
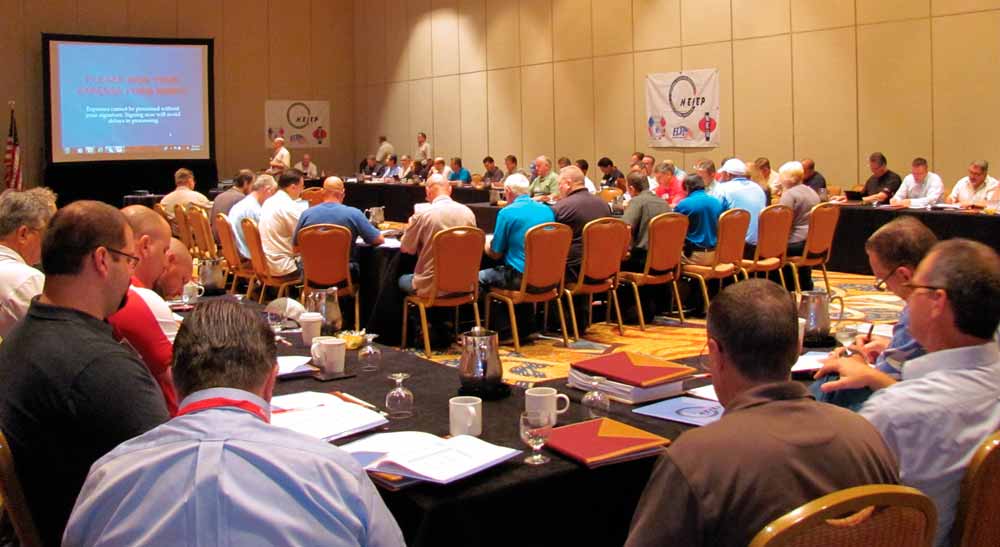
The National Elevator Industry Educational Program (NEIEP) plays host to its Joint Apprentice Committee (JAC) Seminar and Lab Showcase in June.
The National Elevator Industry Educational Program (NEIEP) held its Joint Apprentice Committee (JAC) Seminar and Lab Showcase on June 17-20 at the Marriott Rivercenter Hotel in San Antonio. Each day showcased identical content, which allowed local unions and companies to choose the day they could attend. Members of the International Union of Elevator Constructors (IUEC) and the National Elevator Industry, Inc. (NEII) were also in attendance. According to Mike Shelton, NEIEP liaison for the San Antonio area, the entire week saw strong attendance, with 76 professionals on the last day.
Each morning kicked off with breakfast and welcome remarks from several members, including NEIEP Executive Director John O’Donnell. Attendees participated in standing for the Pledge of Allegiance and took a moment of silence for a few industry members who had recently passed away. Within minutes, your reporter knew she was in excellent company. Following the opening remarks, attendees passed a microphone around and introduced themselves and the unions they represented.
The seminar then shifted into a video overview of JAC and the makeup of the committee. Discussions on annual committee contracts, JAC responsibilities and standard agendas were also discussed at length. It was emphasized that the JAC plays a pivotal role in the way it educates industry members. Next, the NEIEP website (www.neiep.org) was reviewed in an effort to familiarize attendees with its content, outreach and recruitment procedures. The review covered the application process, dissemination list and volunteer information. In addition, a brief explanation of the Elevator Industry Aptitude Test was provided. Though there were several members taking turns presenting different information, it was clear attendees were on the same page and appreciated the content.
Tim Daly, NEIEP area coordinator in Kansas City, explained to your reporter that NEIEP provides a “job fair”-like atmosphere, but many companies are not aware of NEIEP programs, so they are not utilized to the extent they should be. According to O’Donnell, NEIEP’s mission is to provide a program of continuing education and training in the basic, intermediate and advanced skills necessary to maintain a knowledgeable workforce to promote safety. The purpose of this event was to demonstrate which educational offerings exist and how they can benefit the industry. According to O’Donnell, the nature of educational models is changing, and NEIEP strives to change with it in order to provide the best training and education possible. “Learning by doing is the best approach,” O’Donnell said.
During portions of the seminar, your reporter was given a tour of the exhibit across the hall, which featured multiple hands-on learning and training labs, all of which were explained in detail by program developers. Lester White, NEIEP program development manager, provided hands-on demonstrations for nearly every lab available. He provided a thorough explanation of how the labs work and what students are required to do to complete the courses. According to White, the equipment and labs are built by instructors with extensive electrical and mechanical backgrounds.
Among the displays was a virtual lab, which provides students with a virtual elevator site, where they can identify problems and select solutions. Ron McKay, another NEIEP area coordinator, walked your reporter through the process, which is very similar to a video game. Students enter the elevator lobby and are given a problem to solve. They are then able to explore the site based on where they think the problem is located (i.e., machine room) and are given an extensive menu with tools to solve the problem. The virtual lab is so detailed, students can use tools to detach wires, etc. to find or solve malfunctions. A learning management system allows instructors to grade students based on the virtual solutions they select to solve various problems. The lab is available to students in both classrooms and their own homes. There is no word on when the virtual program will be available to the industry, but it will doubtlessly be beneficial and convenient for students.
Following the virtual lab, several program developers provided an overview of some of NEIEP’s newer learning labs, including “Advanced Hydraulic Valve Operation,” which covers the design, functioning, operation, adjustment and testing of two of the most-used hydraulic valves in the industry (from Maxton Manufacturing Co. and Elevator Equipment Corp.). The valve-simulator lab provides students with hands-on experience for valve adjustment, as well as instruction on cutaway valves used as visual reference aids to apprenticeships and continuing-education courses. The course is meant to be used by those with prior experience in the field or those who already have a good understanding of hydraulic systems. The course is comprised of three lab books and hands-on training, all of which stress the importance of safe practice.
O’Donnell and David Aranda, Region 5 NEIEP area coordinator in Austin, then took your reporter offsite to tour the program’s traveling welding lab, which has been providing courses for four years. The training is offered in five large trailers, which travel to different locals in need of welding certification, and four onsite permanent classrooms in Chicago, San Francisco, Salt Lake City and Minneapolis.
The training provides a practical hands-on assessment for certification, and according to O’Donnell, students can receive their welding certification in 40 hr. NEIEP partners with welding manufacturer Lincoln Electric, which provides much of the coursework materials. “Once everyone in a certain local is certified [who] wants to be, the trailers move to the next local,” O’Donnell explained. The trailers are diesel powered, and the welding units are equipped with heavy-duty filters that eliminate 95% of the fumes and hazardous materials. An air-handling unit addresses the remaining materials. O’Donnell also explained each trailer is dedicated to fallen industry members. During our own walkthrough of the welding lab, a representative from the Texas Department of Labor was also receiving a tour to ensure it met local and federal labor regulations.
A tour of NEIEP’s virtual escalator lab followed that of the welding lab. The escalator lab was in design stages approximately three years ago and was created because students needed hands-on training for escalators; however, the previously designed units were too large to transport to classrooms. With the virtual escalator course, students can explore the complex inner workings of an escalator through an interactive 3D computer model. The course highlights structure, function and troubleshooting.
White then guided your reporter to several of the other NEIEP training labs, including the pipe and wire lab, which allows students to follow a print to pipe out a board with the same materials and procedures they would encounter in the field. In addition, the lab includes a diagram to wire the switches.
The line-starter and motor lab was also thoroughly explained. With this lab, elevator contractors have the opportunity to put the theory they have learned into practice by wiring relay logic circuits and soft starters. High- and low-voltage configurations are also explored in this course. In the Peelle Freight Door Operator Lab, students are trained to work with mechanical and electrical components of the door system, and learn new ways to safely and efficiently approach freight-elevator door work.
Your reporter went across the hall to check out the remaining seminar discussions between lab tours. These included a presentation on how to conduct interviews and new-hire procedures for apprentice programs. In addition, committee members were walked through the sections of the NEIEP website that provide information on how to monitor an apprentice’s progress. The NEIEP apprenticeship program requirements were explained, as well as an overview of NEIEP’s continuing-education offerings. Following the seminar, attendees were invited to lunch, then “released” into the training exhibit, where the learning began.
To gain an elevator company’s perspective of NEIEP, O’Donnell introduced Larry Leadingham, director of Health and Safety, and Allen Ashby, safety director for the Southwest region, both of ThyssenKrupp Elevator Americas. Leadingham and Ashby provided good insight into how companies find NEIEP’s offerings useful. According to Ashby, who sets up NEIEP training for ThyssenKrupp Elevator employees, the feedback from the in-field training is 100% positive. “We care about the safety of our people and the industry, so we encourage constant training,” Ashby said.
From an IUEC point of view, James Bender, assistant general president, said the main focus for the program is to keep up with technology and learning apparatuses. Bender believes the hands-on training helps keep students enthusiastic. He said:
“A better-educated industry creates a safer workforce and equips professionals with the skills that help them focus on the dangers around them in the industry. The training is a long-term investment.”
Your reporter also had the pleasure of a one-on-one conversation with IUEC General President Frank Christensen, who talked about his history in the elevator industry. Christensen got his start in the business as a “helper,” a position now commonly known as “apprentice.” He has served in various officer and leadership roles, and was elected IUEC’s general president almost one year ago. Christensen explained his vision of NEIEP’s future and his involvement: “I truly believe my main goal and focus [are] about safety and education.”
Following the interviews with IUEC, you reporter returned to the lab exhibits. It was clear attendees were fascinated with the level of hands-on activity available. Your reporter asked White the main difference between NEIEP’s offerings and other continuing-education programs, and he said many classes teach the theory of the courses, whereas NEIEP is heavily focused on the application, which is learned through a lot of hands-on training. According to Assistant Director Joe Devlin, who was also involved in the discussion and provided much valuable insight regarding industry training and education, “The eye will buy more than the ear will hear.”
Get more of Elevator World. Sign up for our free e-newsletter.