Elan Lifts completes VT project in neo-baroque London building.
by Gary Cremin
Elan Lifts recently completed a six-car group destination control lift system at UK House, a neo-baroque building at the junction of London’s Oxford and Great Titchfield streets. Originally opened in 1906 as a department store, UK House is now a multi-tenanted office building, retaining some retail space on the Oxford Street side. In 2017, phased renovation work began, and included extending the building to include a residential penthouse floor and replacing the lifts.
Elan installed four new machine-room-less (MRL) firefighting lifts in 2018, before moving onto the main office lifts in 2019. The existing lifts, which served levels G and two through seven, were 1200 kg, 1.6 m/s and geared 1:1 roped, with rear counterweights and a conventional machine room. The new lifts serve additional floors and are a gearless MRL arrangement contained within the existing extended lift wells, with an increased duty of 1275 kg at 2.0 m/s.
The lifts were designed in house by Elan and manufactured in the U.K. using high-quality components.
Layout
The six lifts are contained within two concrete lift wells with trimmer steels, with a narrow lobby between the two wells. The car depths needed to be increased to suit Disability Discrimination Act requirements, and one lift was to serve rear entrances, which required moving the counterweight arrangement to the side. The position of the landing entrances needed to align with the new ground floor lobby tiles, which required modifications to the existing structural openings and meant that each lift was unique with a different offset arrangement.
Lift Cars
The dimensions were increased from 2,000 mm wide x 1,200 mm deep x 2,350 mm high to 1,800 mm wide x 1,500 mm deep x 2,700 mm high. The car finishes consist of polished high-gloss metallic panels curved in each corner. The panels were designed to be removable in case of damage to the paint. The suspended ceiling is fitted with a 1,200mm bespoke flush mounted dimmable light fitting. The doors are mirror polished stainless steel, and the full-height mirror opposite aligns with the doors. All wall and door finishes were coated with COTECH® to protect the finishes from corrosion and fingerprints.
The marble flooring pattern aligns with the ground floor lobby tiles and extends over a hidden sill to the car nosing.
The car slings were specially designed with diagonal pulley support steels to maximize the car width. They are fitted with VG safety gears, ELSCO roller guides and Schwartz pulleys with SKF bearings. Static balancing is fitted below, but this is minimal, due to the design and layout.
Entrances
The entrance dimensions were increased from 1,060 mm x 2,135 mm 2 panel center opening (PCO) to 1,100 mm x 2,400 mm 2 PCO. The structural openings needed to be increased to suit. They were made an additional 300 mm higher than required to allow the entrances to be raised in the future if computer flooring is fitted. The entrances were, therefore, fitted to steel frames anchored into the building fabric. The frames can be adjusted to enable the entrances to be raised in the future.
New openings were formed at levels one and eight, along with rear openings at LG and 8R on Lift E.
The entrance frames were manufactured by Meiller and consist of heavy-duty double-skin doors (mirror polished at the ground floor and car, with satin at other floors) and grooveless (hidden) stainless-steel sills. The upper floors were fitted with V-grooved architraves – 400 mm x 10 mm without bend radiuses; these were wrapped around the Meiller entrance frame and manufactured to resemble solid stainless-steel sheets.
Control System
The destination control system was manufactured by NEW-Lift. It operates via a serial LON bus. It was fully plug and play and required a single LSF trailing cable per lift. The six MRL control panels were installed remotely in the fifth-floor controller room, and measuring just 2.5 m x 1.5 m, they did not require a separate group control panel.
The control system interfaces with touch screens. Along with security access control and invasion control, special access control was developed to limit the number of passengers following the outbreak of the COVID-19 pandemic. Other features include entering a service code, which takes a lift out of group and parking at the car roof level with the landing entrance for safe access.
The Elevision lift monitoring system was installed, linking all the lifts in the building. As well as providing a large range of remote-monitoring features, this all-new, web-based system places an emphasis on predictive maintenance and availability statistics using cloud-access services.
Touch Screens
Each landing was provided with two TFT touch screens, which were flush mounted into the wall due to the narrow lobby. The faceplates were custom designed to align with the wall tiles, while maintaining EN 81-70-compliant features and dimensions. The screen layout was developed with the architect and contain the company logo and bespoke fonts.
The car touchscreen contains a feature to display the floor buttons when the lift is being used for servicing or maintenance. The car operating panel was laser cut to finish flush with the car wall panel and contains only the touchscreen, auto-dialer, and door open and alarm buttons. All lift information is displayed within the touchscreen without additional engraving. All screens are UPS-backed.
Drive System
The drive system consists of a Ziehl-Abegg SM210.70B 25.7 kW gearless machine, ZAdyn 4CS062 contactor-less inverter and ZArec4C recuperation unit, all located at the top of the lift well. The isolated machine bedplate and hitch steels consist of heavy-duty rolled steel sections spanning the lift well and built into pockets.
Environment
The lifts are fully BREEAM® compliant. Traffic analysis and energy consumption were calculated, and standby, LED lighting, variable voltage, variable frequency and regenerative drives were fitted.
Environmental waste was reduced by repositioning and extending the existing guide rails and retaining the counterweight filler weights. The new 2:1 counterweight frames and combination brackets were designed to suit the existing fillers.
This was a challenging installation, requiring precise design, manufacturing and fitting in an occupied building. Senior management at Elan, including Managing Director Michael Fernandez, Sales Director Tony Fillery and your author, took on active roles from concept to completion. The onsite installation team was fully trained by Elan and led by Danny Marshall. Testing was completed by Robert Moore.
It was a combined undertaking along with the client (Axiom), two architects (C&G and TP Bennett) and the lift consultant (Cundall).
Two additional lifts were fitted alongside the six-car group – a 40-person, two-stop cycle lift with high-end finishes and a construction lift serving the ground floor and roof level. The construction lift will eventually be converted into a residential express lift serving the new penthouse.
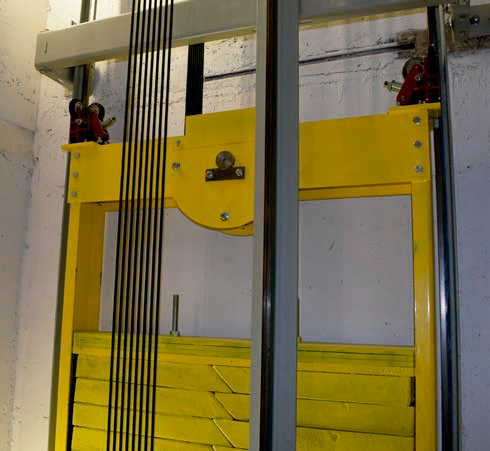
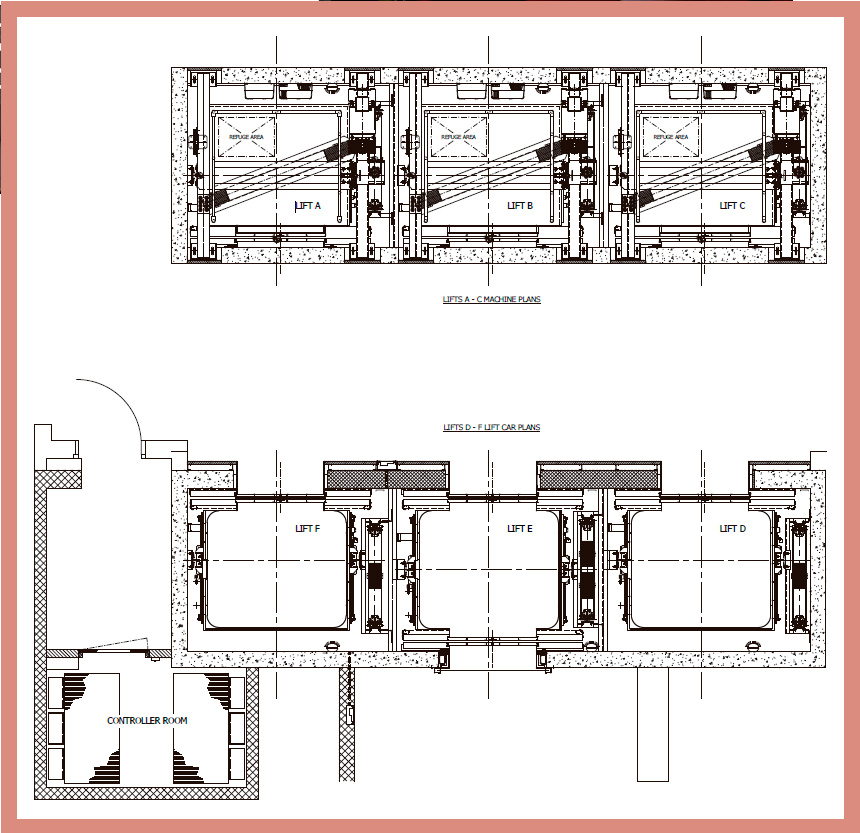
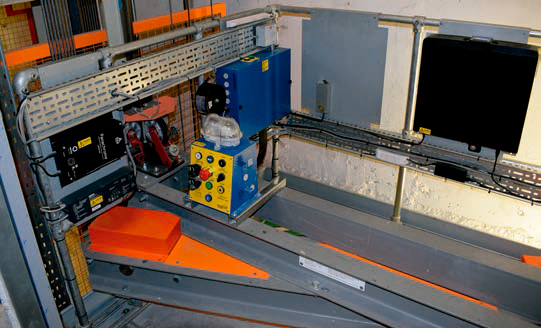
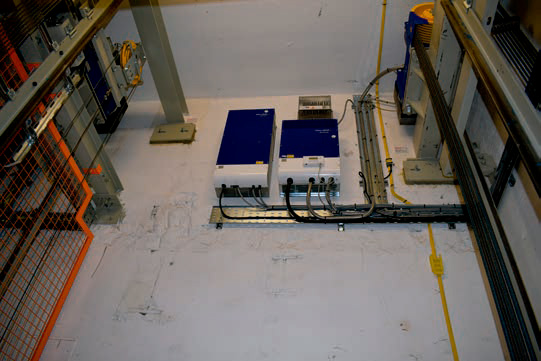
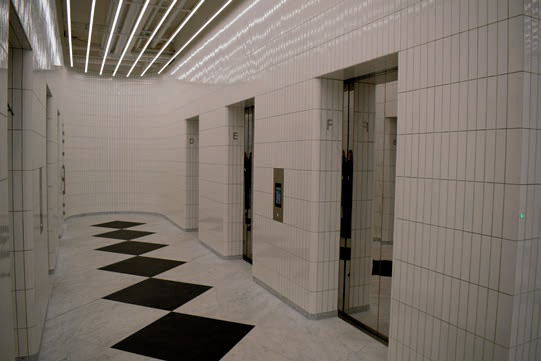
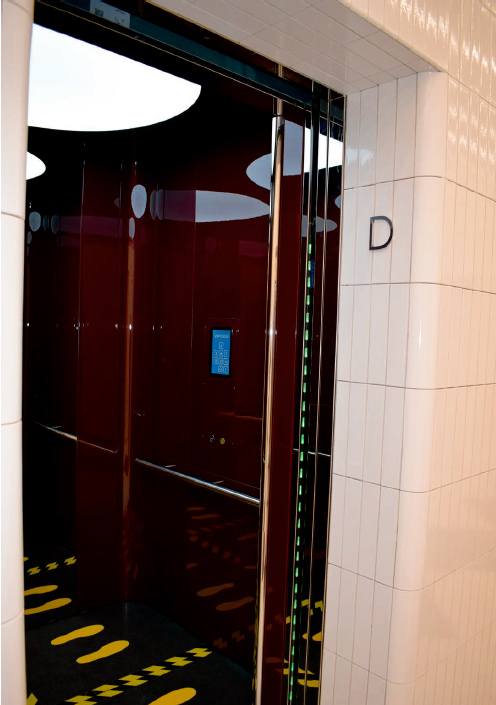
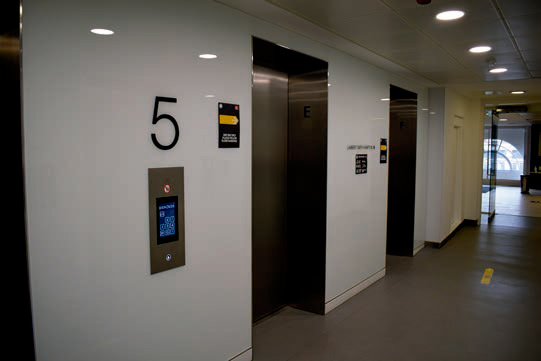
Get more of Elevator World. Sign up for our free e-newsletter.