The Elevator Designs of Jeddah Tower
May 1, 2016
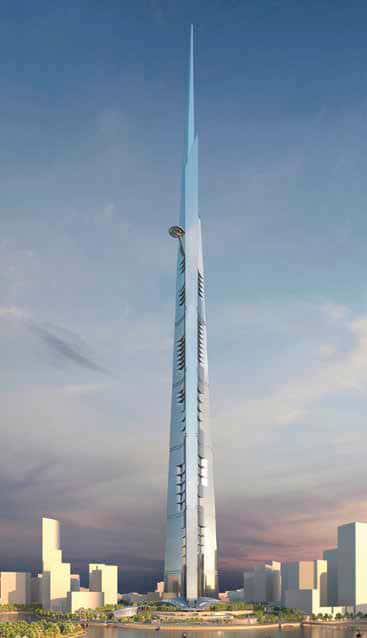
Designer of Jeddah Tower elevators outlines technology and in-depth planning going into the elevatoring of the future world’s tallest.
When it is completed in 2018, the mixed-use Jeddah Tower (formerly Kingdom Tower) will become the new world’s tallest tower. It will contain multiple, stacked mixed-use population zones, including subterranean parking, building entry/amenity/retail floors, office floors, hotel levels, serviced apartment floors, six residential zones and two rooftop observatory/sky-terrace levels served by double-deck elevators. Each of these zones will be served by its own sets of local and express high-speed sky-lobby (SL) shuttle lifts. The project will be equipped with 36 gearless and 22 machine-room-less (MRL) elevators and eight escalators serving the estimated 4,000-5,250 tenants/occupants. The elevator groups will be provided with the most advanced, all-digital destination dispatching, motor and motion controls. Lift safety designs will include “lifeboat” evacuation capabilities, seismic and high wind designs, world-class lift-car ride qualities, and high car pressure (windage) mitigations.
Elevator Design Considerations
The new multiuse Jeddah Tower will contain the following key occupancies (in ascending order):
- Two levels of subterranean parking for about 2,205 automobiles to be served by dedicated office, hotel/amenity/serviced apartment, and residential parking shuttle elevators
- Two levels of main-floor entry points for the office, hotel, serviced apartment, residential, observatory, and hotel amenity (ballroom, meeting rooms, restaurants, etc.) floors. These levels are to be served by the various local and SL shuttle elevators and escalators.
- A seven-story office portion containing approximately 22,500 m2 of diversified tenancy types
- A 200-room luxury hotel located on seven levels
- A 121-unit serviced apartment zone located above the hotel floors on 11 levels
- Six zones of dedicated residential units with 439 units containing one, two, three and four bedrooms, sub penthouse, penthouse and super penthouse (royal) suites
- Building top observatory/restaurant viewing decks (the world’s highest public viewing area at 630 m)
- Communications/high-definition TV spire (service to top floor level 230 at 922 m)
Because of the extreme building heights and required elevator distances, the best way to provide elevator services to the various building segments is the use of dedicated, multi-zone local and express elevators, plus SL shuttles and inter-zone upper transfer floors. We have also separated each type of traffic by zone and function, and provided multiple vertical-transportation (VT) equipment cores, so that the various tenants, visitors, employees and service requirements are separated from one another, while permitting their own private building entrance and exit points. The use of multiple SL and transfer floors makes the building cores more efficient, as many of the local elevator cores can then be stacked vertically on top of one another.
The midpoint transfer floors are necessary for the dedicated fire/service/transformer/medical emergency elevators, because the present state-of-the-art maximum practical vertical height for high-speed elevators — single- or double-deck and passenger or service elevators — is about 550-600 m. (The highest present elevator rise is 504 m in the Burj Khalifa.)
The elevators have been designed to incorporate state-of-the-art, cutting-edge technologies such as “lifeboat” emergency evacuations, destination dispatching with integrated building-security lobby turnstiles and green Leadership in Energy & Environmental Design technologies. However, the present VT equipment designs utilize proven, present-day elevator technologies that have previously been provided in some of the world’s existing tallest towers, including the Burj Khalifa, Taipei 101, Shanghai Tower and the Ping An Insurance Tower. The Jeddah Tower VT equipment-tendering construction documents were set up to encourage competitive bidding. At the end of the lift-tendering process, KONE was awarded the VT equipment contract and installation.
Offices
The seven-story office floors are to be located on top of a four-level entry, retail and hotel amenity complex. Based on the projected 22,500-m2 gross floor area, the total office population could be in the 1,900-person range. Based on these projections, a group of five single-deck passenger elevators would be sufficient to meet the “World Class A” office-building tenant VT requirements. The 21,725 m2 of net rentable area indicates that at least one dedicated service elevator should be provided for office tenants.
Hotel Spaces
The 200-room luxury hotel is to be located above the office floors on levels 20-26. The hotel will be served by a three-car group of guest passenger elevators shuttling between the first-level entry/reception floor, the second-level hotel/restaurants floor, the fourth-level hotel spa and guestroom levels 20-26.
Serviced Apartment Spaces
The 121 serviced apartments will be located above the hotel and are to occupy tower levels 27-37. They are designed to be rented to short-term expatriate workers and will serve as overfill hotel rooms during peak periods. The serviced apartments’ three-passenger-elevator group will share the first- and second-level entry/reception areas with the hotel guests, stop at the 20th-floor hotel executive lounge, then run express to the serviced apartments levels 27-37.
The hotel and serviced apartment floors are to be served by a combined group of two dedicated service elevators with stops at levels B2 and B1, B1M, 1, 2, 4 (spa), 20 (executive lounge/back-of-house and marshalling areas) and guestroom floors 21-37.
Residential Spaces
The remainder of the Jeddah Tower is to be devoted to six groups of residential units. The Group 1 residential portion is to contain 21 levels with 159 units and be served by three, top/up local passenger elevators operating between the 42nd SL and apartment floors 44-55 and 58-66. The Group 2 residential portion is to be provided with 61 units, located on levels 73-83 (11 floors) and is to be served by three, top/up local passenger elevators, operating from the 43rd-floor SL with a Group 2 to 1 transfer floor at level 66.
The Group 1 and 2 residential local apartment zones are to be served by a three-car passenger double-deck SL shuttle group with express service between levels 1, 2, 42 (SL) and 43 (SL). By utilizing double-deck SL shuttles, the number of shuttles required is reduced, while providing segregated, exclusive entry/exit floors for the Group 1 and Group 2 apartment residents.
The Group 3, 4, 5 and 6 residential units are to be served by a combined three-car local passenger elevator zone. The Group 3 residential portion is to contain 40 apartment units located on levels 87-94. The Group 4 residential portion is to contain 58 apartments located on levels 99-103 and 106-120. The Group 5 residential portions will contain 90 units located on levels 125-143, and the Group 6 residential portions will have seven units located on levels 148-154.
The three elevator combined local lifts will be dispatched from the 84th-floor SL with a load of 1350 kg at a speed of 7 mps and stops at levels 84 (SL), 87-94, 99-103, 106-120 and 125-154, and restricted/special service to the observatory at level 158. The three express-shuttle lifts are to provide SL service to the local Group 3-6 residents with a load of 1350 kg at a speed of 9 mps, and stops at levels 1 (entry/exit) and 84 (SL).
Service/Firefighter/Medical Emergency/Goods Lifts
To meet the International Building Code requirement, as seen in Table 1, to have at least one elevator serve every building level for firefighters and medical emergency service, the tower will be provided with three separate groups of single-deck, dedicated service/firefighter/medical emergency high-speed elevators. Because of the extreme vertical distance, these firefighter/service elevators must be divided into a low-rise group (three units), a high-rise group (one unit) and a super-penthouse group (one double-deck unit). When required, inter-Group 6 transfers would also be possible at levels 154-158 onto the top deck of lifts S3 and S2, then transfers between elevators S3 and S2 (upper decks) at level 43 if OB1 and OB2 are out of service.
These elevators will normally be utilized for residential service functions to Groups 1-6, such as maids and cleaning-crew movements, tenant deliveries, move-ins/-outs, tenant unit fit-outs/improvements, and transporting repair/support personnel. These cars will also be available for safe lift (transformer core) replacements, the observation/Sky Terrace 157th level and the 159th upper observatory floor replenishments, firefighter/evacuation service, any required hotel (food, service/maids, etc.) residential service deliveries, and employee shift changes between the B2 loading dock and upper-floor marshalling areas.
Observatory
The world’s tallest observatory/Sky Terrace floor is to be located at level 157 (630 m), and the upper observatory level 159 (638 m). These floors are to be served by two express, double-deck, high-speed shuttle elevators. Because of the extreme loads (1600 kg at 10 mps) and long journeys, the elevators are to be equipped with KONE UltraRope carbon-fiber synthetic hoist ropes. Large observatory visitor queuing areas are to be located away from the main tower building entry floors at level 1 for loading the arriving visitors on the top deck of the elevator, while simultaneously unloading of the departing passengers occurs at level B1 from the bottom deck.
It is envisioned that the OB1 and OB2 decks will load and unload simultaneously. Local transfers between Observatory Levels 157 and 159 will be available for handicapped persons by using two 1350-kg, 1.75-mps local passenger lifts.
Subterranean Parking Service
The office tenants, hotel guests, serviced apartment guests and residential tenants are to be provided with separate sets of parking-shuttle passenger elevators and ballroom escalators.
Destination Dispatching and Integrated Building Security
The latest elevator designs for mega-high-rise towers are also integrating the office-building entry-floor lobby security turnstiles with the elevator destination-dispatching strategies so building tenant and guest security cards can access both systems simultaneously. It is possible to devise a similar system for the residential-zone tenants, particularly the Group 6 VIPs — to provide them with hierarchical modes of selective dispatching if desired.
Emergency Tower Evacuations via Elevators
Many modern high-rise towers are being designed with “lifeboat” Phase 3 Firefighter Elevator Evacuation capabilities on selected group lifts. The maximum time to completely evacuate a building’s tenants and visitors via the emergency-exit stairs and elevators has not been set by any building codes. However, an appropriate model has generally been established at one-half to two-thirds of the building fire rating (2 hr. X 50% = 60 min.; 2 hr. X 66% = 80 minutes), or less than the time it took for One World Trade Center to collapse after the airplane impact on 9/11 (102 min.). A time of 60 min. or less has been selected for ideal evacuation utilizing the Jeddah Tower lifeboat lifts.
Building area-of-refuge floors, as required in the Middle East, are generally located roughly every 15-20 floors on vertical centers and placed so that building tenants can use the emergency stairs to access these “holding” floors. It is assumed that evacuating tenants can walk up approximately five to 15 floors and down approximately 15-20 floors to reach a nearby refuge floor. It is also becoming standard practice to have the building emergency-evacuation stairs recycle at each refuge floor to permit walking tenants to rest at the refuge floors before reentering the exit stairs to continue their trip.
Some of the psychological and physiological assumptions used for the “Jeddah Tower Lifeboat Evacuation” study that would likely prevail during an actual building emergency are:
- It is extremely difficult, if not impossible, to completely evacuate any 150–200 story building via the exit stairs during the allotted time.
- There would typically be a number of elderly, infirm and handicapped persons (an estimated 1-2% of the population), particularly those in the residential zones, who would not be inclined or agile enough to use the exit stairs to walk down 100–150 floors.
- Most present building codes have been designed to address building fire emergencies and evacuations only via the exit stairs or to direct tenants to a refuge area, where they are then ordered to wait for further instructions.
- After the events of 9/11, building tenants will likely not be content to wait in the affected building or accumulate on refuge floors and wait for further instructions. Instead, they would welcome the opportunity to be safely and quickly evacuated from the refuge floors via the lifeboat elevators.
- Selected elevators should be designed and equipped with special lifeboat operations so they can be utilized in the building evacuation, probably with onboard human monitors or firefighters running the designated lifts on attendant service and manually controlling the car-door opening and closing operations. Other hall monitors would likely be stationed at each upper refuge floor in assigned muster stations to assist with crowd control and tenant queuing to expedite an orderly evacuation process.
- The higher an occupant is located in the tower during an emergency event, the less likely he or she is to utilize the exit stairs, and the more likely he or she is to walk to a refuge floor, where quick elevator lifeboat evacuation operations would undoubtedly be welcome.
Following are the typical operations that have been specified for the designated lifeboat lifts to be operable:
- Before double- or triple-deck elevators are to be used for Firefighters’ Phase 2 or 3 evacuations, the lower deck(s) must be cleared and shut out of service. After clearing, only the upper decks can be used for phases 2 or 3, as only one set of cab doors can be visually observed and controlled from the upper car by the single onboard lift emergency attendant. It would be possible to utilize all decks for lifeboat evacuations only if they were all equipped with attendant operations and inter-cab communications.
- All special lifts to be used for evacuations are to be equipped to operate continuously on the building emergency generator on standby power in case normal power is lost.
- All special evacuation lifts are to be equipped with Phase 3 operations, attendant service and preassigned hoistway clearing operations (not required for fire-induced evacuations), utilizing car-top closed-circuit TV cameras and lights and test runs before lifeboat operations begin.
- All special-operation evacuation elevators are to be equipped with onboard paging, firefighters’ sound-powered phone jacks, an intercom system, attendant operations (constant-pressure door-close and hall-call bypass buttons) and refuge-floor special arrival/loading lanterns and crowd detectors. The elevator platforms must also be designed for ASME A17.1 — 125% of the nominal car loads (capacity rating) — so the lifts cannot easily be overloaded and “stuck” (until someone gets off) by onrushing, panicked passengers. These proposed Jeddah Tower lifeboat systems and emergency-elevator evacuation operations closely parallel those specified by Phase 2 and installed by Otis on the selected Burj Khalifa lifeboat elevators.
Lifeboat capabilities and special operations have been added to the Jeddah Tower SL shuttle elevators, the two observatory shuttle elevators and the main service elevators. Calculations show that by using these selected lifts in the lifeboat evacuation mode, the various zone building populations can be completely emptied within 4-54 min.
Elevator Hoistway Venting and Stack-Effect Mitigations
Since the adoption of the first elevator design codes, there have been provisions to provide the top of high-rise elevator shafts with hoistway venting directly to the outside air. The vents consist of approximately 3 sq. ft. (0.3 m2) of open area with the intended purpose of venting hot smoke and gasses that may accumulate at the top of the hoistway during a building or pit fire and to prevent a flashover “ball fire” from reigniting after the main building fire is extinguished.
With the development of modern elevators — equipped with car and counterweight roller-guide shoes running on milled-steel rails — the older greased and oiled solid guide shoes, sometimes running on wooden rails, were no longer used. The application of roller guides and steel rails dramatically reduced the accumulation of combustible materials in the elevator pits, which then eliminated the frequency of pit and hoistway fires and, therefore, the need for hoistway vents.
As tall-building designs continued to evolve, the fully sealed and air-conditioned building became commonplace. The hoistway venting requirements did not change, except when energy costs increased, necessitating the addition of motorized or spring-operated shutters added to the vents to minimize the loss of normal building heating and air-conditioning.
Building “stack effect” normally occurs in high-rise buildings located in northern climates when the cold outside air entering the building at the ground floor(s) flows into the elevator shafts and escapes through the upper levels (often through the hoistway smoke vents) to outside air.
Some building codes permit the deletion of the hoistway smoke vents if the hoistways are fully sprinklered (usually not permitted in buildings provided with overnight sleeping quarters). Though the Jeddah Tower is located in a desert climate, with summer temperatures approaching 120°F, it was estimated that due to the extreme building height, the outside temperature at the building top could be 15°F less than at the bottom. If the elevator hoistways were to be equipped with normal smoke vents, it was feared that a reverse stack effect could occur with anticipated outside building temperature variations, causing the building cooling to flow out of the building. Therefore, it was decided to not use any hoistway venting but, instead, provide each elevator hoistway top with a building fire sprinkler head that is responsive to heat and smoke. The elevator machine rooms have similar sprinklers and are also to be equipped with shunt-trip devices that prevent the sprinklers from being energized until electrical power is removed from the lift hoist machines.
Sustainability Features
Sustainable elevator designs require that the Jeddah Tower lifts be provided with selected “World Class A” performance and group design criteria. These provisions may require slightly higher capital costs but often result in reduced equipment, operational and maintenance costs. Green elevators are designed to efficiently transport building tenants and visitors to and from their destinations within an optimal time. The proper lift-design selections often result in increased tenant productivity, as reflected in reduced waiting times, faster call response, quicker floor-to-floor performance times and hoist-equipment dynamic braking, while using less energy to transport the passenger loads.
The following sustainable features were included in the elevator equipment designs and bid specifications. All of the Tower’s 58 elevators are to be equipped with the latest, high-tech, selected group-demand destination dispatching, digital motor and motion controls and “World Class A” floor-to-floor performances. The technology includes:
- Elevator group destination dispatching: passengers going to the same or contiguous floors are assigned to the same elevator, and the elevators only “move” in response to registered hall and/or car call demands or assignments.
- Reduced average group waiting times and quicker times to destinations
- All elevator hoist machines are to be equipped with permanent-magnet, synchronous motors and ACV3F power-conversion units and corresponding technologies.
- All lifts are to have regenerative operations and dynamic braking (i.e., they pump electrical power back into the building’s electrical grid and hold the elevators back when running in an “overhauling” mode).
- Observatory passenger shuttles elevators OB1 and OB2 will have double-deck duties of 1600 kg with speeds of 10 mps and are equipped with UltraRope carbon-fiber hoist ropes, which reduce the required hoist-motor sizes and electrical power demands.
Get more of Elevator World. Sign up for our free e-newsletter.