Cut Back the Callbacks
Feb 1, 2021
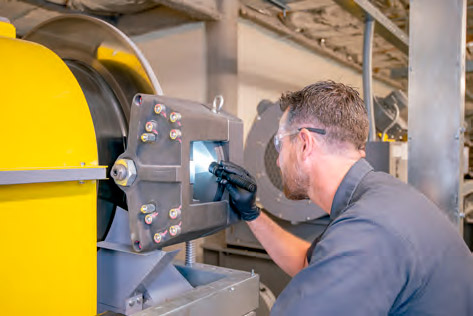
Mitsubishi Electric U.S. Elevators and Escalators Division executive says proactive efforts keep VT running safely.
by Matt Irvin
Elevator and escalator maintenance is vital for the safety of the riding public, and the vast majority of service providers take that responsibility seriously. Safety depends upon quality and proven components, but this is only part of the equation. Just as important are servicing equipment on a schedule and utilizing well-trained, dedicated service mechanics.
Mitsubishi Electric US, Inc. Elevator and Escalator Division service and labor relations department Senior Director John Faure says the company’s priorities on training of field personnel, its “proactive parts replacement” and a detailed preventive maintenance program have helped it lead the industry in terms of maintaining a low callback rate.
Training is an important part of the process. All of the company’s mechanics go through the National Elevator Industry Educational Program (NEIEP). “Additionally, we have our own training programs and strict service guidelines for technicians in the nuances of [our] equipment,” said Faure.
“Training combined with a dedication to thorough preventive maintenance helps to ensure a low callback rate.” Faure said Mitsubishi Electric U.S. equipment averages less than one callback per unit per year — this, in an industry that averages anywhere from two up to 15 callbacks per unit per year.
Faure added that field employees are encouraged to engage in continuing education internally and with NEIEP “for their knowledge and skill enhancement.” Elaborating on the company’s efforts, he noted:
“We provide specialized training in Japan and have certified master trainers who train and retrain trainers and workers locally. On-the-job training is applied for cross-training and expansion of employee knowledge. Safety training is extremely important and continuously provided.”
Another key feature is the “proactive parts replacement” program, in which identified parts, regardless of equipment manufacturer, are replaced “before they wear out.” While this procedure is impossible to make perfect, Faure says, it is “determined from service mechanic feedback and hands-on assessment, data analysis in conjunction with lifetime expectancy, tolerance criteria, and, at times, vibration analysis.”
He continued:
“These replacement parts can range from the timely replacement of batteries that are important for backup and emergency functions, testing of power outputs [and] replacement of enclosed switches, through to high-wearing parts associated with doors, including parts such as the guide-rail sliding inserts that affect noise and ride quality.”
The key to proper maintenance, Faure said, is having a detailed preventive maintenance program that allows the service provider to “address potential concerns and avoid problems.”
Get more of Elevator World. Sign up for our free e-newsletter.